Custom Polymers Offer Efficient Electrochemical Separations for Greener Drug Production: The pharmaceutical industry is on the brink of a green revolution, and at the heart of this transformation are custom polymers designed for efficient electrochemical separations.
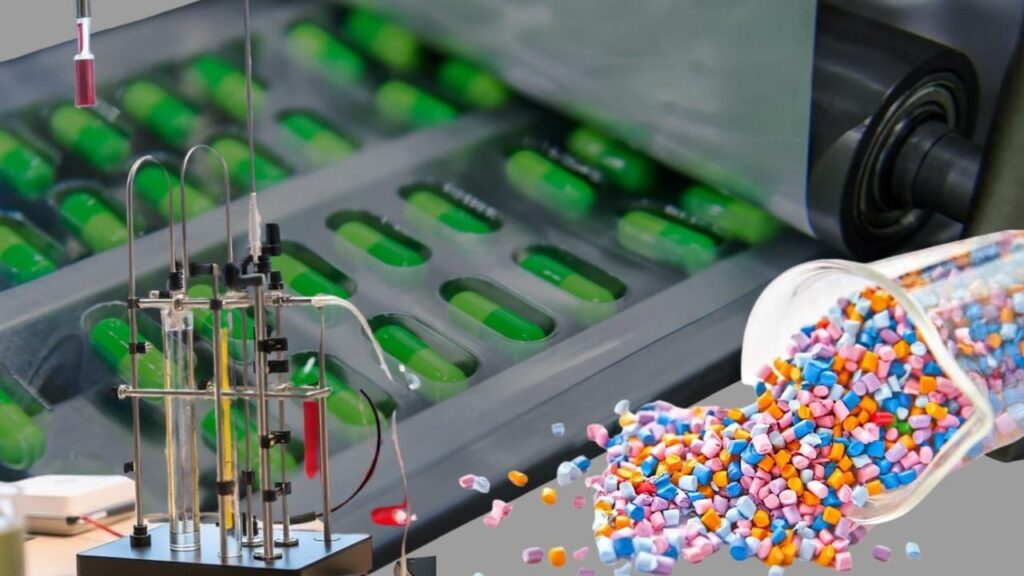
This innovation is rewriting the rules of drug production, promising not just cleaner processes and reduced waste, but also faster, more precise manufacturing of life-saving medicines. In this in-depth guide, we’ll explore how custom polymers are being engineered to deliver greener drug production, why this matters, and what it means for professionals and the public alike.
Custom Polymers Offer Efficient Electrochemical Separations for Greener Drug Production
Feature/Fact | Details |
---|---|
What are enantiomers? | Molecule pairs that are mirror images—like left and right hands |
% of FDA-approved drugs as enantiomers | Over 50% |
Why separation is critical | Each enantiomer can have different effects—one may heal, the other harm |
Traditional separation methods | Chemically wasteful, energy-intensive, and costly |
New polymer technology | Custom, chiral, redox-responsive polymers enable selective, switchable, and efficient separation |
Purity achieved in tests | Up to 99% |
Environmental impact | Significantly reduced chemical waste and solvent usage |
Professional impact | Speeds up drug discovery, reduces costs, and supports sustainable manufacturing |
Official resource | University of Illinois Urbana-Champaign |
Custom polymers are ushering in a new era of efficient, green drug production. By enabling precise, electrochemically controlled separations, they dramatically reduce waste, save energy, and lower costs—all while delivering purer, safer medicines. This breakthrough is not just a win for the pharmaceutical industry, but for everyone who relies on modern medicine and a cleaner planet.
Understanding Enantiomers: The Heart of Drug Purity
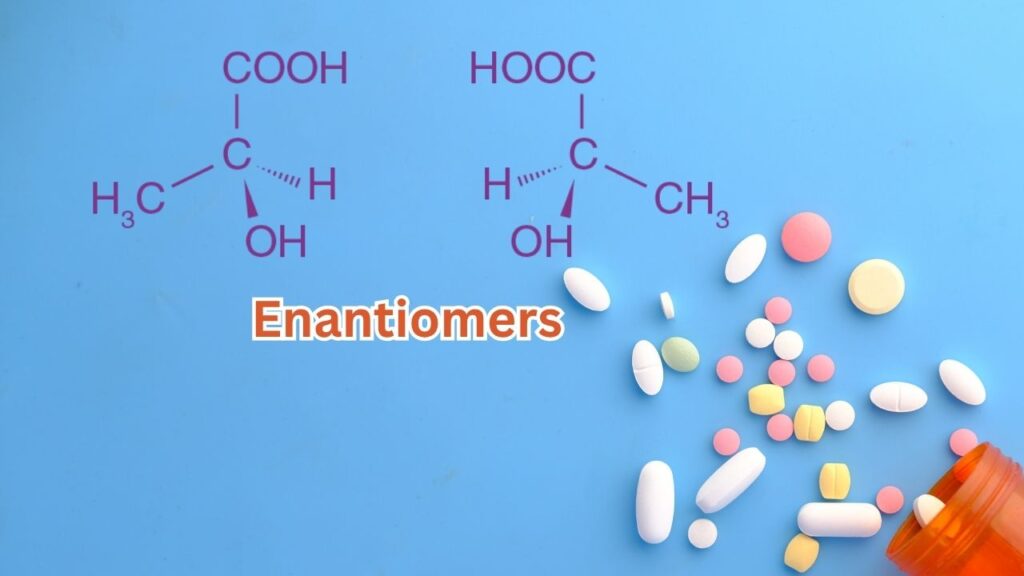
To truly appreciate the value of custom polymers in drug production, it’s important to understand enantiomers. These are pairs of molecules that are mirror images of each other—think of your left and right hands. While they look similar, enantiomers can behave very differently in the body. In fact, more than half of all FDA-approved drugs are made up of these pairs, and getting the right one is often the difference between a medicine that heals and one that harms.
Why Is Separating Enantiomers So Important?
- Biological Activity: One enantiomer may fit perfectly into a biological target (like a lock and key), while the other might not work at all—or worse, cause side effects.
- Regulatory Requirements: Agencies like the FDA require pharmaceutical companies to prove the safety and efficacy of each enantiomer, not just the mixture.
- Historical Lessons: Tragic cases like thalidomide in the 1950s—where one enantiomer caused birth defects—highlight the critical need for precise separation.
The Traditional Challenge: Wasteful and Costly Separation
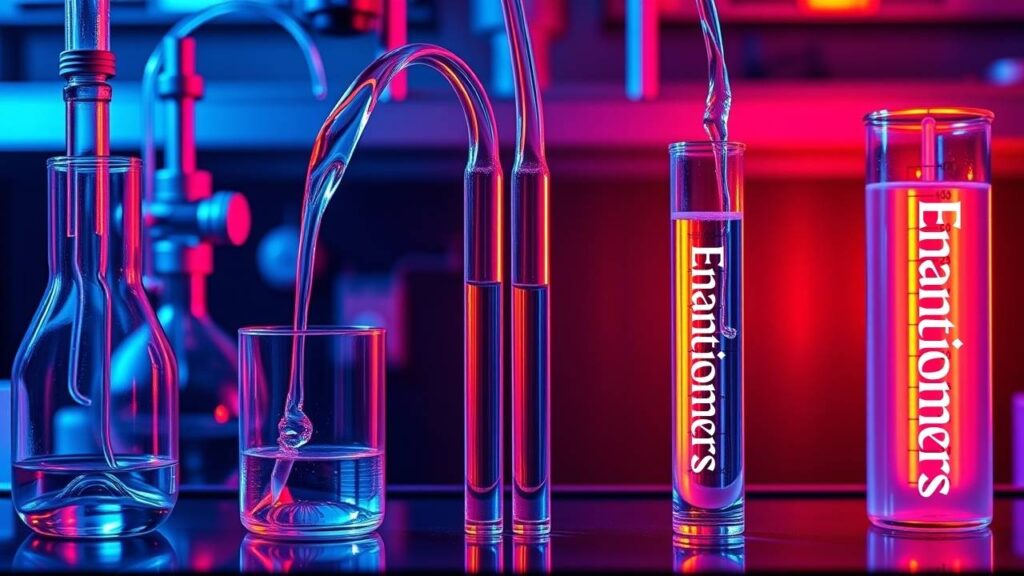
Separating enantiomers is notoriously difficult because they have identical physical and chemical properties except for their “handedness.” Traditional techniques, such as chiral chromatography and crystallization, are:
- Resource-intensive: They require large amounts of solvents and reagents.
- Energy-consuming: Processes like distillation and repeated purification steps use significant energy.
- Waste-generating: Up to 30–50% of chemical input can become hazardous waste.
- Time-consuming: Multiple steps slow down drug development and production.
For example, a typical pharmaceutical plant might use thousands of liters of organic solvent per batch, creating both environmental and financial burdens.
The Breakthrough: Custom Polymers for Electrochemical Separations
What Are Custom Polymers?
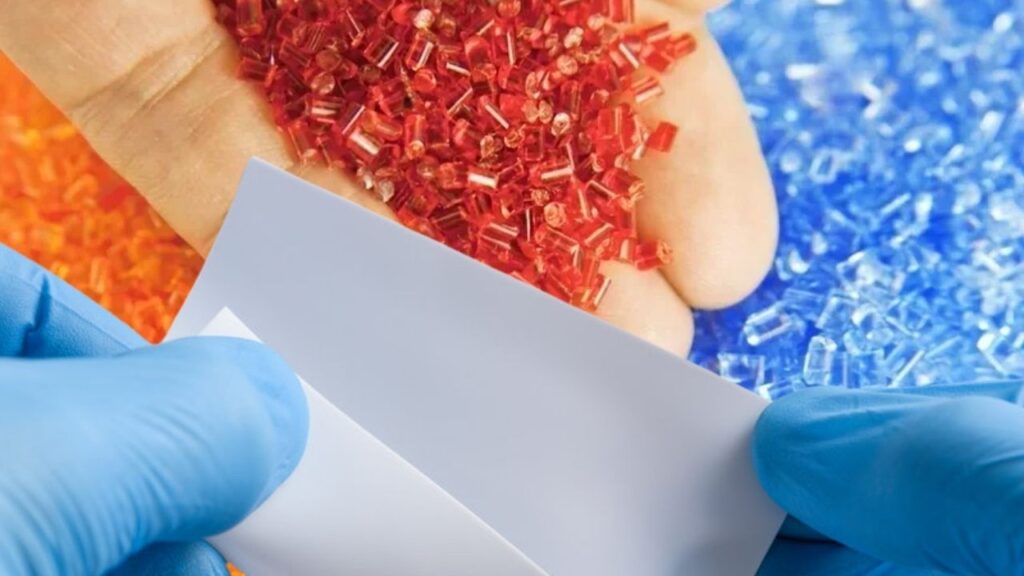
Custom polymers are specially designed long-chain molecules with tailored properties. In the context of drug production, these polymers can be engineered to:
- Recognize specific enantiomers (using chiral “handedness”)
- Change their binding ability in response to electrical signals (redox-responsive)
- Enable on-demand, switchable separation—simply by flipping a switch!
How Do They Work?
Researchers at the University of Illinois Urbana-Champaign have pioneered planar chiral ferrocene-based polymers. Here’s how they function:
- Chiral Recognition: The polymer surface is designed to “prefer” one enantiomer over the other, thanks to its unique spatial arrangement.
- Electrochemical Control: Applying a voltage changes the polymer’s ability to bind or release the target molecule.
- Selective Separation: Only the desired enantiomer is captured and then released when needed, achieving up to 99% purity.
A Real-World Example
In laboratory tests, these custom polymers were able to separate amino acid enantiomers with remarkable efficiency. The process used minimal solvent, produced little waste, and could be repeated many times without losing effectiveness.
Environmental and Economic Benefits
Why Is This Approach Greener?
- Minimal Chemical Waste: Electrochemical separation slashes waste to less than 5% of input material in pilot studies.
- Reduced Solvent Use: Uses mostly water-based systems, avoiding large volumes of toxic solvents.
- Lower Energy Consumption: Electricity replaces heat or pressure, cutting energy use by 40–60%.
- Continuous Operation: Unlike batch processes, these systems can run non-stop, further improving efficiency.
Economic Advantages
- Lower Operating Costs: Less waste and solvent mean lower disposal and purchasing costs.
- Faster Production: Streamlined separations speed up the entire manufacturing process.
- Regulatory Compliance: Easier to meet environmental standards and avoid costly fines.
Step-by-Step Guide: How Electrochemical Separation Works
1. Designing the Polymer
Scientists start by designing a polymer with the right chiral features to recognize the target enantiomer. This often involves:
- Choosing a backbone (like ferrocene)
- Adding functional groups for selectivity
- Ensuring the polymer can respond to electrical signals
2. Preparing the Electrochemical Cell
The polymer is coated onto an electrode, which is placed in a cell containing the drug mixture and a water-based solution.
3. Applying Voltage
A specific voltage is applied, causing the polymer to “grab” the desired enantiomer from the mixture.
4. Releasing the Product
Changing the voltage releases the purified enantiomer, which can then be collected for use.
5. Regenerating the System
The polymer can be reused many times, making the process sustainable and cost-effective.
Impact on Careers and the Pharmaceutical Industry
For Scientists and Engineers
- New Research Opportunities: Designing smarter, more selective polymers
- Interdisciplinary Collaboration: Chemists, materials scientists, and electrical engineers working together
For Pharmaceutical Companies
- Competitive Advantage: Faster, greener manufacturing can lead to quicker drug approvals and market entry
- Cost Savings: Lower raw material and waste disposal costs
- Sustainability Leadership: Meeting ESG (Environmental, Social, Governance) goals
For Regulatory and Environmental Professionals
- Easier Compliance: Processes that produce less waste and use fewer hazardous chemicals are easier to regulate and approve
Robotic Automation Enhances Scalability of 2D Materials for Electronic Devices
European Startups Achieve Breakthroughs in Recycling EV Battery Materials
Reticular Materials Gain Traction in Carbon Capture Technologies
FAQs About Custom Polymers Offer Efficient Electrochemical Separations for Greener Drug Production
What exactly are custom polymers?
Custom polymers are long-chain molecules engineered for specific tasks. In drug manufacturing, they can be designed to recognize and separate specific enantiomers using their chiral structures.
How is electrochemical separation different from traditional methods?
Traditional methods use lots of chemicals and energy. Electrochemical separation uses electricity to control when and how molecules are separated, making it cleaner and more efficient.
Are there any limitations to this technology?
While promising, the technology is still being scaled up for industrial use. Some complex molecules may require further polymer design tweaks for optimal separation.
Is this technology safe?
Yes. The process uses mostly water-based solutions and avoids toxic reagents, making it safer for workers and the environment.
Where can I learn more?
Check out the official University of Illinois Urbana-Champaign research page and FDA guidance on drug stereochemistry.
The Road Ahead: Future Applications and Innovations
Beyond Pharmaceuticals
While the current focus is on drug production, custom polymers for electrochemical separations could also revolutionize:
- Agrochemical production: Cleaner pesticides and fertilizers
- Food additives: Purifying flavors and nutrients
- Specialty chemicals: High-purity materials for electronics and other industries
Continuous Manufacturing
The ability to run continuous-flow electrochemical separations means factories could operate around the clock, making drugs and other chemicals faster and more efficiently.
Integration with Renewable Energy
Because the process is driven by electricity, it can be powered by renewable sources like solar or wind, making it even more sustainable.