Nike Unveils FlyWeb: Nike has once again raised the bar in sports innovation with the launch of Nike FlyWeb, a 3D-printed material designed for elite athletic performance. This groundbreaking textile is not just another fabric—it’s a technological leap that could change how athletes experience support, comfort, and speed. Whether you’re a professional runner, a weekend athlete, or simply curious about the future of sports apparel, FlyWeb’s debut is a story worth knowing.
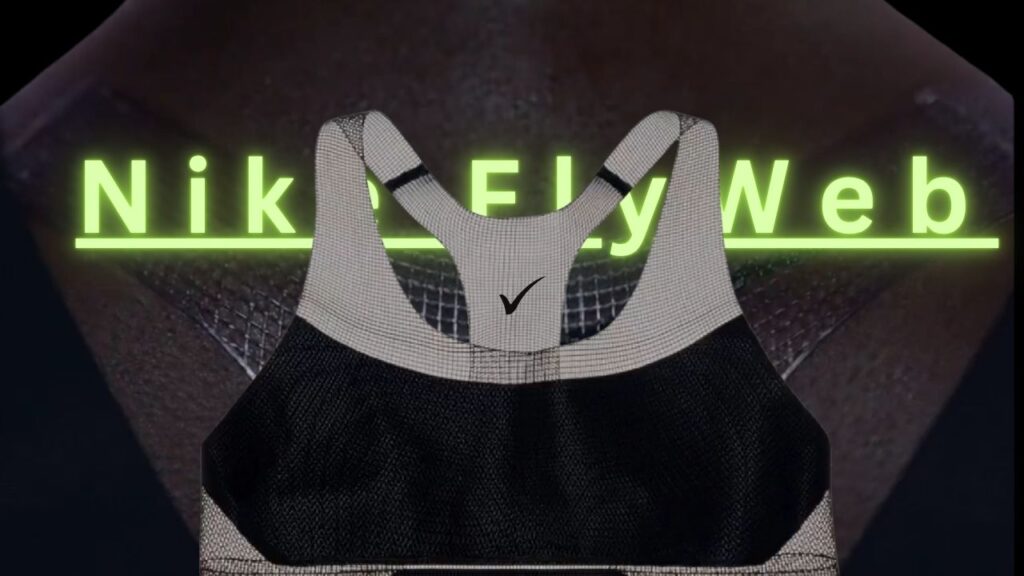
Nike has always been at the forefront of sports technology, from the iconic Air soles to Flyknit uppers. With FlyWeb, the company is taking a bold step into the world of 3D printing, aiming to create sportswear that feels almost invisible yet delivers unmatched support and breathability.
Nike Unveils FlyWeb
Feature/Stat | Details |
---|---|
Product Name | Nike FlyWeb |
Technology | 3D-printed thermoplastic polyurethane (TPU) |
Key Benefits | Ultra-lightweight, seamless support, exceptional breathability, moisture management |
First Application | Custom sports bra and aerodynamic “Fly Suit” for elite runner Faith Kipyegon |
Unique Attribute | Feels like “wearing nothing,” yet offers strong support |
Sustainability | Reduces material waste, enables on-demand customization |
Professional Impact | Enhances speed, comfort, and performance for elite athletes |
Official Website | Nike.com |
Nike FlyWeb is more than just a new material—it’s a glimpse into the future of sportswear. By combining advanced 3D printing with athlete-driven design, Nike is creating gear that’s lighter, more comfortable, and more sustainable than ever before. Whether you’re an elite competitor or a casual athlete, the innovations behind FlyWeb promise to make sports more enjoyable and accessible for everyone.
What Is Nike FlyWeb?
Nike FlyWeb is a first-of-its-kind, 3D-printed textile made from thermoplastic polyurethane (TPU). Unlike traditional fabrics, FlyWeb is created using advanced additive manufacturing—meaning the material is built layer by layer, allowing for precise control over its structure and performance. This process results in a fabric that is:
- Featherweight: Testers say it “disappears on your body” while still offering robust support.
- Seamless: No extra straps or bulky seams, reducing chafing and discomfort.
- Highly Breathable: The open lattice design lets air flow directly to the skin, keeping athletes cool and dry.
Why Is This Important?
Most sportswear is made by weaving or knitting yarns together, which can create pressure points, seams, and areas that trap heat or moisture. FlyWeb’s 3D-printed construction eliminates these issues, giving athletes a second-skin feel and performance advantages that traditional materials can’t match.
How Was Nike FlyWeb Developed?
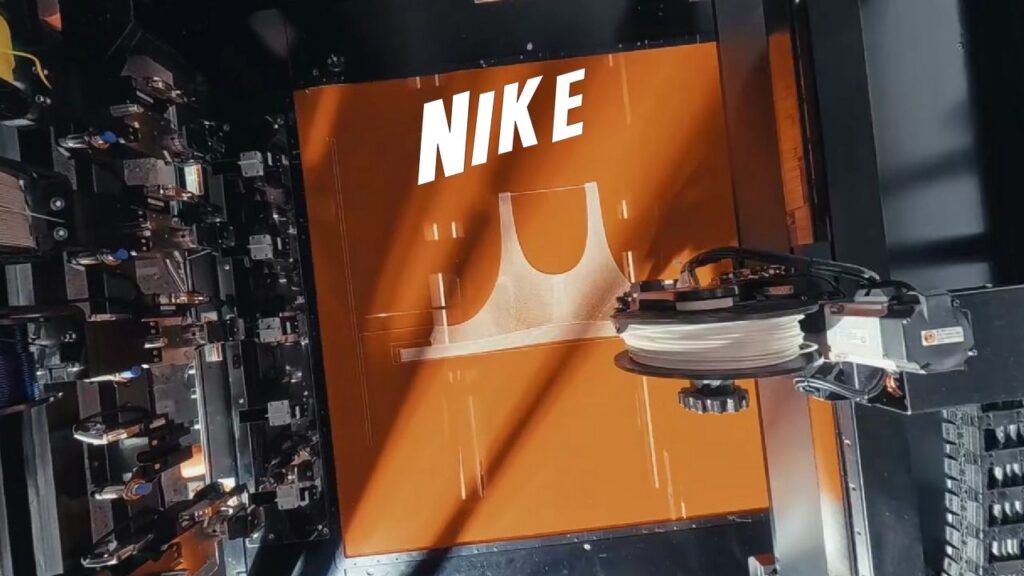
Nike’s innovation team spent years researching and testing FlyWeb with input from elite athletes. The goal was to create a material that could deliver both support and comfort—two things that are often at odds in sports apparel, especially for women’s sports bras.
The breakthrough came when Nike engineers realized that 3D printing allowed them to:
- Customize support zones: By varying the thickness and density of the TPU lattice, FlyWeb can provide more support where it’s needed and more stretch where it’s not.
- Integrate features directly into the fabric: For example, moisture-wicking channels and aerodynamic “aeronodes” can be printed right into the garment.
- Reduce waste: Because the material is printed to shape, there’s less leftover fabric and fewer offcuts, making the process more sustainable.
Real-World Example: Faith Kipyegon’s Breaking4 Speed Kit
FlyWeb made its debut on the world stage when Olympic champion Faith Kipyegon wore a custom FlyWeb sports bra and aerodynamic suit during her historic sub-four-minute mile attempt. The kit was designed specifically for her body and running style, featuring:
- Targeted support to minimize bounce and maximize comfort.
- Aeronodes—tiny bumps that help reduce air resistance and improve speed.
- Moisture management to keep her cool during intense exertion.
Kipyegon described the experience as “wearing nothing at all,” yet she felt fully supported—a testament to the power of FlyWeb’s design.
How Does Nike FlyWeb Work? A Step-by-Step Guide
1. Digital Design
Nike’s engineers use computer-aided design (CAD) software to map out the exact structure of the FlyWeb lattice. This allows them to:
- Adjust support and stretch in different areas.
- Integrate features like ventilation holes or moisture channels.
- Customize the fit for individual athletes.
2. 3D Printing
The design is sent to a state-of-the-art 3D printer, which uses thermoplastic polyurethane (TPU) as the raw material. The printer builds the fabric layer by layer, creating a seamless, flexible, and durable textile.
3. Testing and Refinement
Each prototype is tested by athletes in real-world conditions. Feedback is used to tweak the design, ensuring the final product meets the highest standards for comfort, support, and performance.
4. Final Product
The finished FlyWeb garment is ready to wear—no sewing, gluing, or extra assembly required. This streamlined process not only saves time but also reduces waste, making it a win for both athletes and the environment.
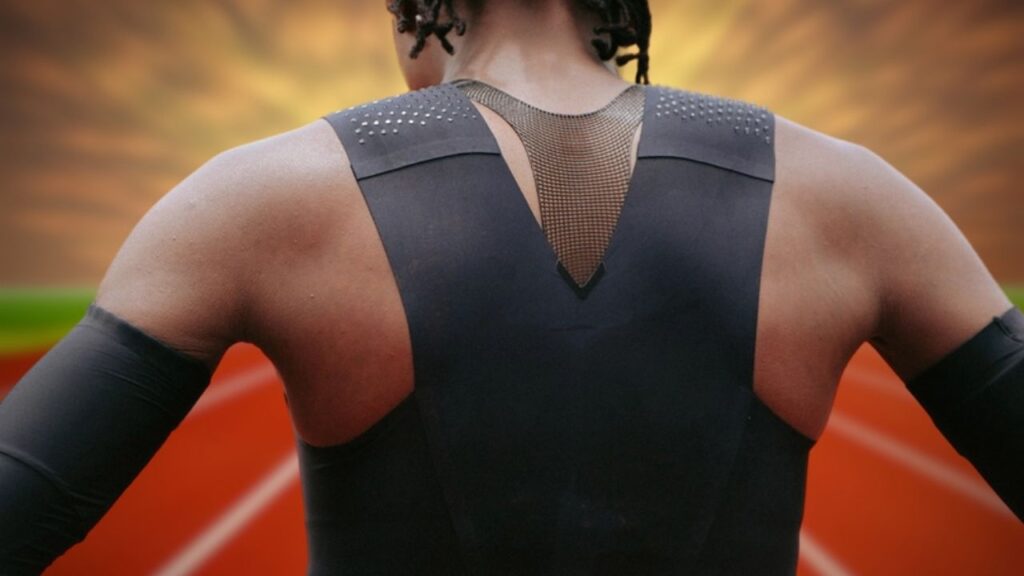
Practical Advice: What Does FlyWeb Mean for Athletes and Consumers?
For Elite Athletes
- Performance Edge: FlyWeb’s aerodynamic and supportive design can help shave precious seconds off race times.
- Custom Fit: Garments can be tailored to each athlete’s body, maximizing comfort and minimizing distractions.
- Innovation Pipeline: Expect to see FlyWeb technology expand into more sports and apparel categories in the coming years.
For Everyday Consumers
- Future Availability: While FlyWeb is currently focused on elite athletes, Nike plans to bring this technology to retail products in the future.
- Sustainability: The 3D printing process reduces waste and allows for more eco-friendly production methods.
- Comfort Revolution: Imagine running, training, or playing sports in gear that feels like a second skin—no bulky seams, no chafing, just pure performance.
The Science Behind 3D-Printed Sportswear
3D printing, also known as additive manufacturing, is transforming industries from aerospace to medicine. In sportswear, it offers several unique advantages:
- Precision Engineering: Designers can fine-tune every millimeter of the garment for optimal fit and function.
- Material Efficiency: Only the necessary material is used, reducing waste and environmental impact.
- Rapid Prototyping: New designs can be tested and improved quickly, speeding up innovation cycles.
Nike’s FlyWeb is at the forefront of this trend, setting new standards for what’s possible in athletic apparel.
New Framework Offers Microscopic, Highly Precise Energy Control for Advanced Nanoscale Devices
World’s Thinnest Silicon-Based Material Unveiled, Opening New Frontiers for Next-Gen 2D Electronics
FAQs About Nike Unveils FlyWeb
What is Nike FlyWeb made of?
Nike FlyWeb is made from 3D-printed thermoplastic polyurethane (TPU), a strong, flexible, and lightweight material.
Is FlyWeb available for purchase?
Currently, FlyWeb is being used for elite athletes and special projects, but Nike plans to expand its availability to consumers in the future.
How does FlyWeb compare to traditional sportswear?
FlyWeb offers superior breathability, support, and comfort, with a seamless design that reduces chafing and bulk.
Is FlyWeb sustainable?
Yes, the 3D printing process minimizes waste and allows for more efficient use of materials, making it a more sustainable option than traditional manufacturing.
Where can I learn more about Nike FlyWeb?
Visit the official Nike website for the latest updates, news, and product releases.