Cold Spray 3D‑Printing Technique: Bridges are a vital part of our daily lives, connecting cities, communities, and people. But did you know that nearly half of the bridges in the United States are in only “fair” condition, and almost 7% are considered “poor”? Repairing these aging structures is a massive challenge, with costs soaring above $191 billion. Enter the “cold spray” 3D‑printing technique, a groundbreaking method that could change how we maintain and repair bridges—making the process faster, cheaper, and much less disruptive.
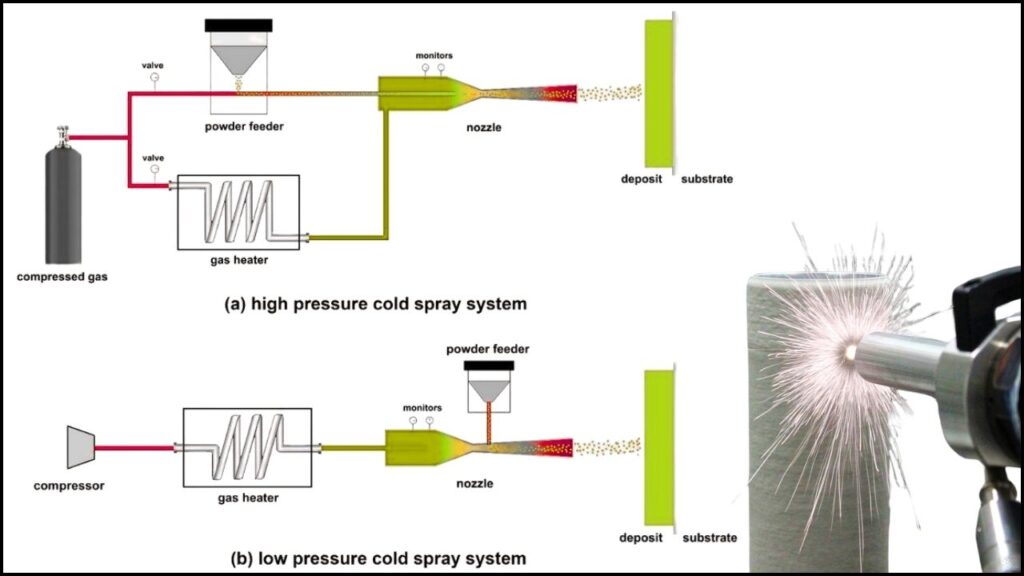
Recently, a team of researchers from the University of Massachusetts Amherst and the Massachusetts Institute of Technology (MIT) made headlines by successfully using this innovative technology to repair a historic bridge in Great Barrington, Massachusetts. Their work could mark the beginning of a new era in infrastructure repair—one that blends cutting-edge science with practical, on-the-ground solutions.
Cold Spray 3D‑Printing Technique
Feature/Stat | Details |
---|---|
Technique | Cold Spray Additive Manufacturing (CSAM) |
First Field Test | Red Bridge (formerly “Brown Bridge”), Great Barrington, MA, May 2025 |
Main Benefit | Fast, cost-effective, and minimally disruptive bridge repair |
US Bridges in “Fair” Condition | 49% (2025 Report Card for America’s Infrastructure) |
US Bridges in “Poor” Condition | 6.8% |
Estimated National Repair Cost | Over $191 billion |
Key Partners | UMass Amherst, MIT, MassDOT, MassTech, US Dept. of Transportation, Federal Highway Administration |
Official Resource | UMass Amherst Civil Engineering |
The cold spray 3D‑printing technique is a game-changer for bridge repair and infrastructure maintenance. By combining advanced scanning, precise material application, and a portable, low-heat process, it offers a safer, faster, and more affordable way to keep our bridges strong and safe for years to come. As the technology matures, expect to see more bridges—and perhaps other structures—benefiting from this innovative approach.
What Is the “Cold Spray” 3D‑Printing Technique?
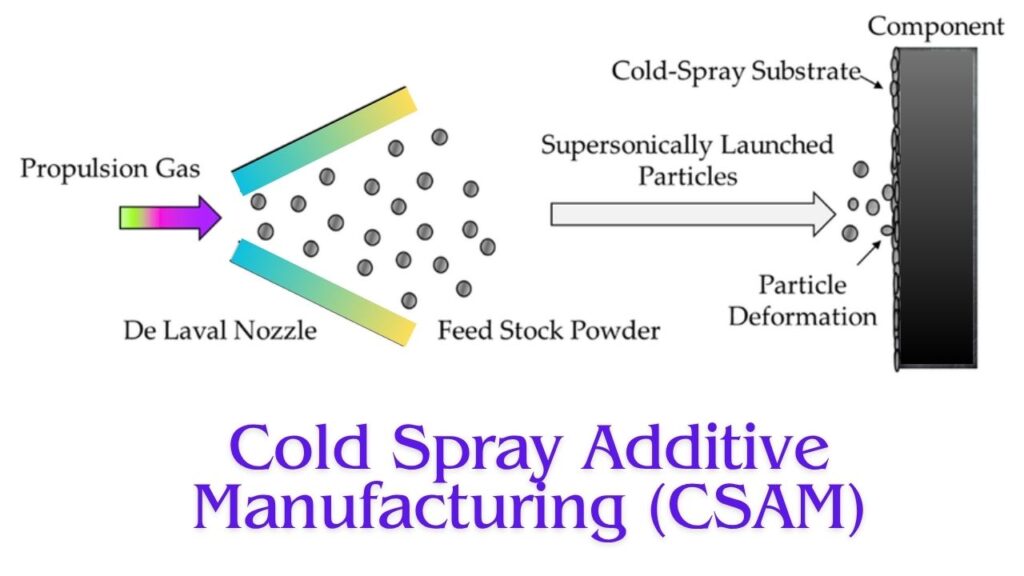
Cold spray additive manufacturing (CSAM) is a special type of 3D printing. Instead of using heat to melt metal, this technique uses compressed gas to shoot tiny metal powder particles at extremely high speeds onto a surface. When these particles hit the damaged area of a bridge, they stick and build up, layer by layer, forming a strong, new metal coating.
How It Works—Step by Step
- Identify the Damaged Area: Engineers use advanced 3D LiDAR scanning to find exactly where the steel has corroded or worn away.
- Prepare the Surface: The area is cleaned and prepped for repair.
- Spray the Metal Powder: Using a handheld applicator, technicians spray the metal powder at supersonic speeds onto the damaged spot.
- Build Up Layers: The process is repeated until the original thickness and strength of the steel are restored.
- Test and Inspect: The repaired section is checked for strength, durability, and corrosion resistance.
This method is called “cold” because it doesn’t use the high temperatures found in traditional welding or thermal spraying. That means there’s less risk of heat damage to the bridge, and repairs can often be made while the bridge is still open to traffic.
Why Is This Technique So Important?
The Scale of the Problem
- Aging Infrastructure: Many US bridges were built decades ago and are now reaching the end of their intended lifespans.
- Corrosion: Steel corrodes over time, especially in harsh weather or when exposed to road salts. This weakens the structure and can lead to dangerous conditions.
- Cost and Disruption: Traditional repairs often require closing bridges, causing traffic jams and economic losses. Full replacement is even more expensive and time-consuming.
The Cold Spray Advantage
- Speed: Repairs can be done quickly, sometimes even while cars are still using the bridge.
- Precision: 3D scanning allows engineers to target only the areas that need fixing, saving time and materials.
- Cost Savings: By repairing instead of replacing, and by minimizing traffic disruptions, communities save money and avoid headaches.
- Safety: The process restores the bridge’s strength and extends its life by up to 10 years or more.
Real-World Example: The Red Bridge Test
In May 2025, the UMass Amherst and MIT team put the cold spray technique to the test on the historic Red Bridge in Great Barrington, Massachusetts. Built in 1949, this bridge was a perfect candidate for a proof-of-concept demonstration.
What Happened?
- 3D LiDAR scans identified the worst corrosion spots.
- Engineers used the cold spray method to rebuild the missing steel, layer by layer.
- The repair was finished with minimal disruption to local traffic.
- The bridge will eventually be dismantled, allowing researchers to take the repaired beams back to the lab for detailed analysis.
Simos Gerasimidis, associate professor at UMass Amherst, called the project “a huge milestone,” saying, “Now that we’ve completed this proof-of-concept repair, we see a clear path to a solution that is much faster, less costly, easier, and less invasive”.
How Does Cold Spray Compare to Traditional Repairs?
Feature | Cold Spray 3D Printing | Traditional Repair/Welding |
---|---|---|
Heat Use | No (cold process) | Yes (high heat/melting) |
Traffic Disruption | Minimal | Often requires full closure |
Precision | High (targeted repairs) | Lower (broader area affected) |
Repair Speed | Fast | Slow |
Cost | Lower | Higher |
Material Waste | Minimal | More waste |
Practical Advice: When and Where to Use Cold Spray 3D Printing
Cold spray 3D printing is not just for bridges! It’s already used in the aerospace, marine, and defense industries to repair airplanes, ships, and submarines. Here’s how you can decide if it’s right for your project:
- Ideal For: Steel structures with localized corrosion or damage.
- Best Locations: Remote or rural areas where traditional repairs are hard to organize.
- When Not to Use: If the entire bridge or structure is beyond repair or if the damage is too extensive.
Steps for Infrastructure Professionals
- Assess the Bridge: Use 3D scanning to map out corrosion.
- Plan the Repair: Target only the areas that need fixing.
- Mobilize the Team: Cold spray equipment is portable and can be brought on-site.
- Monitor the Results: After repair, monitor the bridge for performance and durability.
Quantum Materials: The Discovery of the Year for 2025
PsiQuantum Study Reveals Roadmap For Loss-Tolerant Photonic Quantum Computing
Marvell Says Future of Cloud Computing Depends on Custom-Built Silicon Chips
FAQs About Cold Spray 3D‑Printing Technique
Q: Is cold spray 3D printing safe for all bridges?
A: Yes, it’s safe for most steel bridges with localized corrosion. However, if the structure is severely compromised, a full replacement may still be needed.
Q: How long does a cold spray repair last?
A: Early results suggest repairs can extend a bridge’s life by up to 10 years or more, depending on conditions and maintenance.
Q: Does the process require special training?
A: Technicians need training in both the cold spray equipment and 3D scanning technology, but the learning curve is manageable for skilled professionals.
Q: Can cold spray be used in bad weather?
A: The process is less sensitive to weather than traditional welding, but extreme conditions (heavy rain, snow) may still delay repairs.
Q: Where can I learn more about this technology?
A: The best place to start is the official website listed in the Key Highlights table.
The Future of Bridge Repair: What’s Next?
The successful test in Massachusetts is just the beginning. Researchers plan to monitor the repaired Red Bridge beams after the bridge is dismantled, running tests to ensure the new metal layers are strong and corrosion-resistant. If all goes well, cold spray 3D printing could become a standard tool for bridge maintenance teams across the country.
Collaboration is Key: The project brings together universities, state and federal agencies, and technology partners—showing that innovation happens best when experts work together.