Scientists Develop Breakthrough Copper Composite: In a landmark achievement, scientists have unveiled a breakthrough copper composite with superior strength and conductivity, a development set to revolutionize industries ranging from aerospace to electronics. This new class of copper-based materials not only retains copper’s legendary electrical performance but also matches or surpasses the strength of advanced superalloys. Let’s explore how this innovation came to life, why it matters, and what it means for the future of technology and engineering.
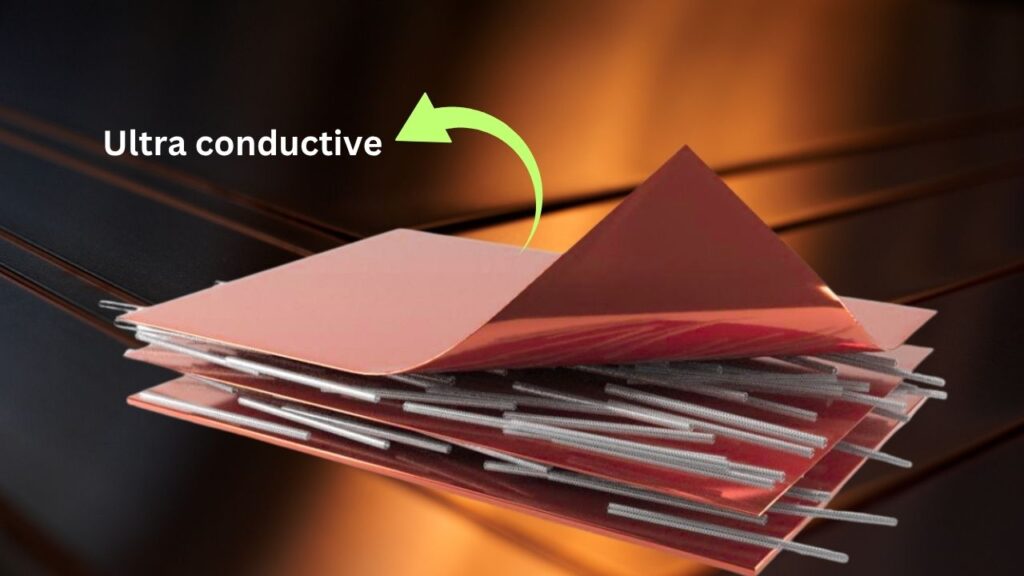
Why Copper Matters—and Its Classic Limitations
Copper is a household name, famous for its reddish shine and its role in everything from electrical wiring to coins. What makes copper so valuable is its exceptional electrical and thermal conductivity—it’s one of the best materials for carrying electricity and heat. That’s why copper is everywhere, from the wires in your walls to the circuits in your phone.
However, copper has a major weakness: it’s relatively soft and loses strength at high temperatures. This limits its use in settings where both high strength and conductivity are essential—like jet engines, military vehicles, or advanced electronics. For decades, scientists have tried to solve this “strength vs. conductivity” dilemma, but boosting one usually meant sacrificing the other.
Scientists Develop Breakthrough Copper Composite
Feature/Statistic | Details |
---|---|
Material Name | Cu-Ta-Li Alloy (Copper-Tantalum-Lithium) |
Strength | Matches/surpasses nickel-based superalloys; withstands extreme heat and stress |
Conductivity | Retains copper’s high electrical/thermal conductivity |
Thermal Stability | Maintains properties after 10,000 hours at 800°C |
Potential Applications | Aerospace, defense, advanced electronics, power grids |
Key Innovation | Nanostructured design with stabilized grain boundaries |
Official Resource | Lehigh University News |
The breakthrough copper composite with superior strength and conductivity marks a new era for materials science. By combining copper’s legendary electrical performance with the toughness of advanced alloys, scientists have opened the door to safer planes, more efficient power grids, and smarter electronics. As this technology moves from the lab to the real world, it promises to make our devices, vehicles, and infrastructure stronger, faster, and more reliable than ever before.
The Breakthrough: Nanostructured Copper Composites
What’s New?
A team of researchers from the US Army Research Laboratory (ARL), Lehigh University, and partner institutions has developed a nanostructured copper alloy—specifically, a copper-tantalum-lithium (Cu-Ta-Li) composite—that overcomes copper’s traditional limits. This material combines the superior conductivity of copper with the mechanical strength and heat resistance of superalloys used in jet turbines and rockets.
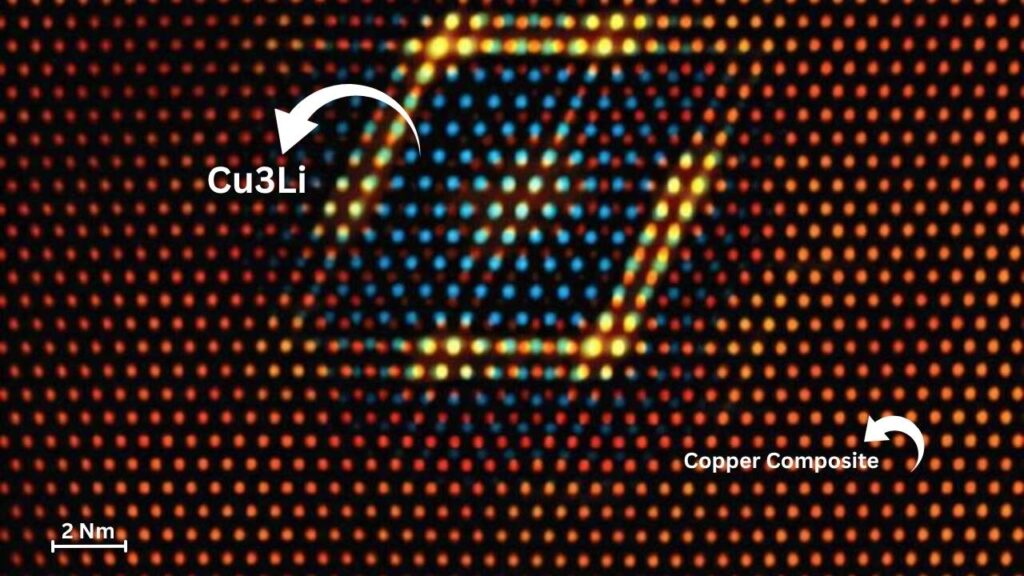
The Science Behind the Strength
- Nanostructured Design: The alloy’s secret lies in its microscopic structure. Scientists engineered the copper matrix to contain tiny, stable precipitates of Cu₃Li, held in place by a tantalum-rich atomic “complexion” (a special layer at the grain boundaries).
- Stabilized Grain Boundaries: Unlike conventional copper, where grains grow and weaken at high temperatures, the tantalum-stabilized boundaries prevent this, keeping the structure strong and stable even after thousands of hours at 800°C.
- No Trade-Off: The result is a material that doesn’t force a choice between strength and conductivity. It delivers both—making it a true game-changer for demanding applications.
Real-World Testing and Results
- Extreme Endurance: The new alloy maintains its high yield strength and resists “creep” (slow deformation under stress) after 10,000 hours at 800°C—conditions that would destroy ordinary copper.
- Superior Performance: Tests show it can withstand stress several times better than the best commercial copper alloys, both at room temperature and in extreme heat.
- Industry-Ready: The US Army has already begun licensing the technology to industry partners, aiming to fast-track its use in next-generation weapons, vehicles, and power systems.
Practical Applications: Where Will This Alloy Make a Difference?
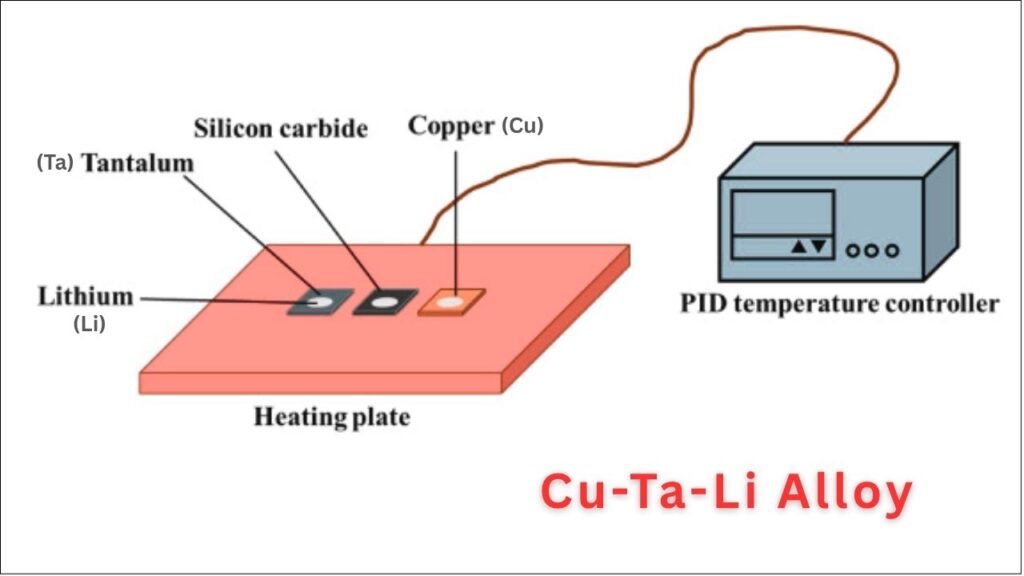
Aerospace and Defense
- Jet Engines and Hypersonics: The alloy’s ability to handle high heat and stress makes it ideal for jet turbines, heat exchangers, and hypersonic vehicle components.
- Military Armor: Its toughness and resilience could lead to lighter, more durable armor that absorbs impacts without weakening.
- Modular Reactors: The alloy’s resistance to radiation and high temperatures is valuable for advanced nuclear power systems on the battlefield.
Energy and Power Grids
- High-Efficiency Wires: With conductivity matching or exceeding pure copper, the new material is perfect for next-generation power transmission lines, reducing energy loss and improving reliability.
- Renewable Integration: Stronger, more conductive wires help integrate renewables like wind and solar into the grid, supporting a cleaner energy future.
Electronics and Everyday Devices
- Smaller, Faster Devices: The alloy’s stability at high temperatures means electronics can run faster and hotter without risk of failure.
- Wear-Resistant Connectors: Connectors and switches made from this material will last longer and perform better, even in harsh environments.
How Do Scientists Make These Super Copper Composites?
Step 1: Choosing the Right Ingredients
- Copper is the main ingredient, prized for its conductivity.
- Tantalum and lithium are added in tiny amounts to create stable, strong structures at the atomic level.
Step 2: Building at the Nanoscale
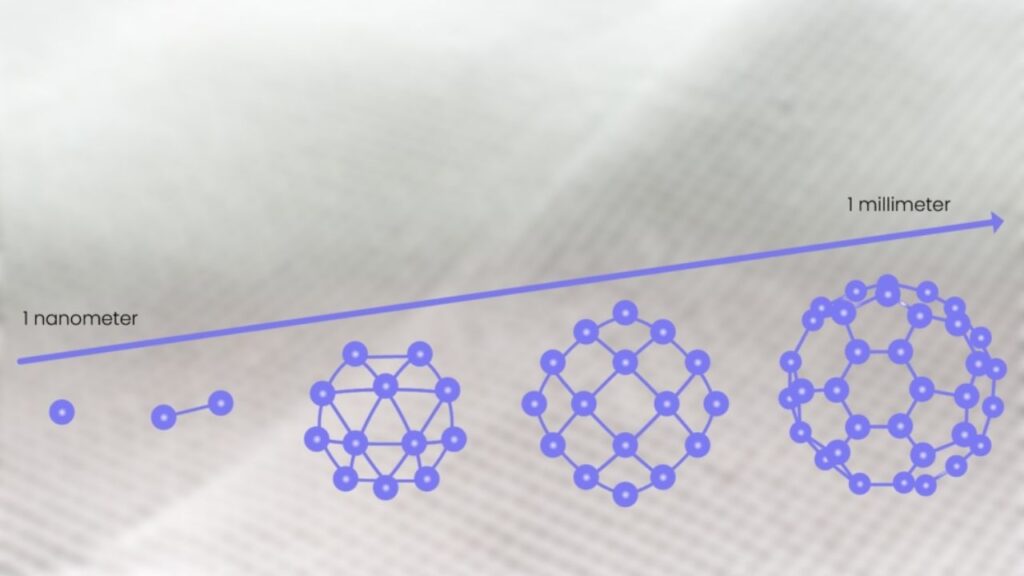
- Scientists use advanced techniques to mix the elements and control the formation of nanostructures—tiny features only a few billionths of a meter wide.
- The key is to create and stabilize special “grain boundaries” that stop the copper from weakening at high temperatures.
Step 3: Testing and Scaling Up
- The new material is rigorously tested for strength, conductivity, and stability.
- Once proven, it’s produced in larger quantities and shaped into wires, sheets, or components for real-world use.
More Innovations: Graphene and Carbon-Enhanced Copper
The copper alloy breakthrough isn’t the only exciting development. Scientists are also enhancing copper with graphene and carbon nanofilms to push performance even further.
Graphene/Copper Composites
- What is Graphene? It’s a single layer of carbon atoms, famous for its strength and conductivity.
- How It Helps: By adding tiny amounts of graphene to copper, researchers have created wires with over 100% of the International Annealed Copper Standard (IACS) conductivity and tensile strengths above 238 MPa.
- Why It Matters: These wires are perfect for power grids and advanced electronics, offering both durability and efficiency.
Copper-Carbon Nanofilms
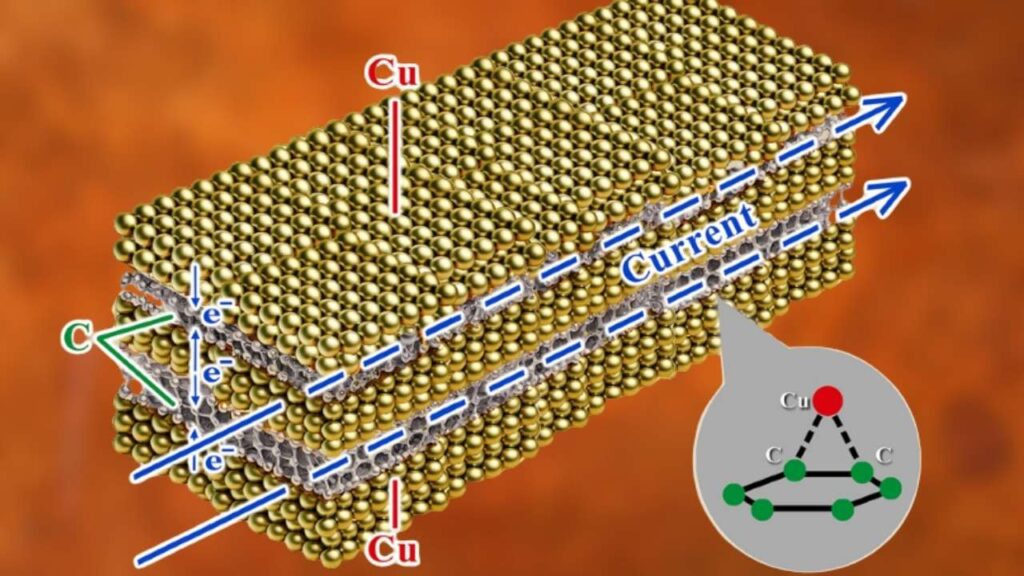
- Layered Design: Scientists use plasma immersion deposition to coat copper with ultra-thin carbon layers.
- Big Results: When carbon nanofilms make up 16% of the total thickness, the composite’s conductivity jumps by over 30% compared to pure copper.
- Industrial Use: This technology is already being adapted for large-scale electrode coatings in electronics and electrical equipment.
AWS Reveals Quantum Chip Ocelot Cutting Error Correction Costs By 90 Percent
Cisco Debuts Prototype Room Temperature Photonic Quantum Networking Chip
FAQs About Scientists Develop Breakthrough Copper Composite
Q1: What makes the new copper alloy different from regular copper?
A: The breakthrough alloy combines copper with tantalum and lithium at the nanoscale, creating a structure that is both extremely strong and highly conductive—even at very high temperatures.
Q2: Will this new material replace all copper wiring?
A: Not immediately. While it’s perfect for demanding applications (like aerospace, defense, and power grids), regular copper is still cost-effective for everyday wiring. Over time, as production scales up, we may see wider adoption.
Q3: Is the new copper alloy safe and environmentally friendly?
A: Yes. The alloy uses small amounts of tantalum and lithium, and its high efficiency can help reduce energy loss and material waste in the long run.
Q4: How soon will we see products using this technology?
A: The US Army is already licensing the technology for defense applications, and industry partners are working to bring it to market. Expect to see it in specialized products within the next few years.
Q5: Can this technology help with renewable energy?
A: Absolutely! Stronger, more conductive wires are crucial for integrating wind and solar power into the grid, making energy transmission more efficient.