Simple Technique Improves CO₂ Conversion Efficiency: Turning carbon dioxide (CO₂) from a climate problem into a valuable resource is one of the most exciting frontiers in science today. In a world facing rising temperatures and mounting emissions, researchers are racing to find ways to not just capture CO₂, but to transform it into useful fuels and chemicals. The good news? A new study has revealed a simple technique that improves CO₂ conversion efficiency, making this vision more practical and affordable than ever before.
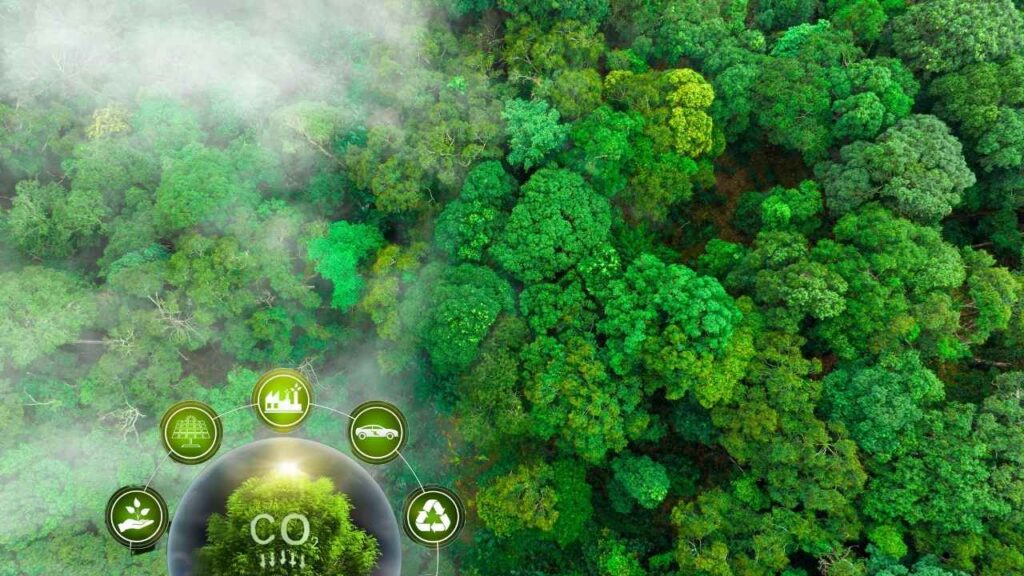
This article will guide you through the latest breakthrough, explain why it matters, and show how these advances could shape the future of clean energy and sustainable industry. Whether you’re a curious student, a concerned citizen, or a professional in the field, you’ll find clear explanations, practical advice, and expert insights to help you understand this important topic.
Simple Technique Improves CO₂ Conversion Efficiency
Feature/Stat | Details |
---|---|
Breakthrough Technique | Encapsulated cobalt-nickel (Co-Ni) alloy catalyst |
Efficiency Achieved | 90% energy efficiency at 800°C |
Product Selectivity | 100% (all CO₂ converted to carbon monoxide, CO) |
Durability | Maintained performance over 2,000 hours |
Cost Impact | Reduces need for precious metals, lowering costs |
Environmental Benefit | Enables carbon recycling, supports climate goals |
Official Source | EPFL/ScienceDaily |
The discovery of a simple technique that improves CO₂ conversion efficiency is a beacon of hope in the fight against climate change. By making it easier, cheaper, and more reliable to turn waste CO₂ into valuable products, this innovation could transform industries and help build a cleaner, greener world. The journey from lab to factory floor is just beginning, but the path forward is clearer than ever.
Why CO₂ Conversion Matters
Carbon dioxide is a greenhouse gas that traps heat in our atmosphere, driving climate change. Every year, human activities like burning fossil fuels and manufacturing release billions of tons of CO₂. Traditionally, efforts have focused on capturing and storing this gas underground. But what if, instead, we could turn it into something useful?
CO₂ conversion is the process of transforming carbon dioxide into valuable products such as fuels (like methane or methanol), chemicals (like carbon monoxide or formic acid), or even building materials. This approach not only reduces emissions but also creates new resources for industry. It’s a win-win for the planet and the economy.
The Challenge: Efficiency and Cost
While the idea of CO₂ conversion is promising, putting it into practice has been tough. Most existing methods fall short in three key areas:
- Low Efficiency: Many systems waste a lot of energy, making them impractical for large-scale use.
- Short Lifespan: Catalysts (the materials that speed up the conversion) often degrade quickly, especially at high temperatures.
- High Cost: Many rely on expensive precious metals like platinum or ruthenium, limiting their real-world application.
To make CO₂ conversion a real solution for climate change, scientists have been searching for ways to overcome these hurdles.
The Breakthrough: A Simple Yet Powerful Technique
A team led by Professor Xile Hu at the Swiss Federal Institute of Technology Lausanne (EPFL) has developed a new type of catalyst that tackles these challenges head-on.
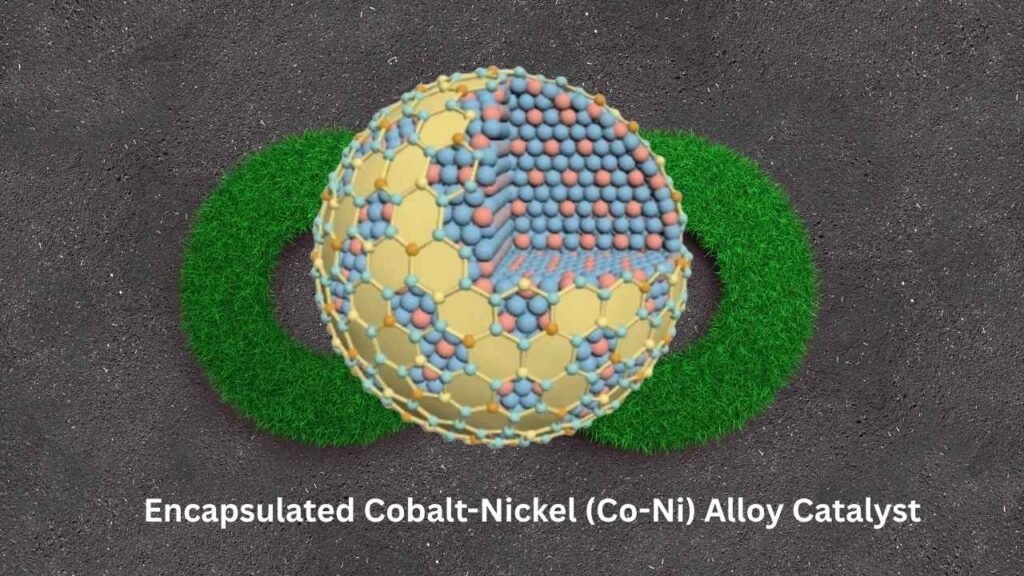
How Does It Work?
- Encapsulated Alloy Catalyst: The team created a catalyst from a mix of cobalt and nickel (two common metals), then wrapped it in a ceramic shell made from doped cerium oxide.
- Why Encapsulation Matters: This ceramic shell prevents the metals from clumping together (a process called agglomeration), which is a common reason catalysts stop working. It also protects the catalyst from harsh conditions inside the reactor.
- Easy Production: The catalyst is made using a straightforward “sol-gel” method, which mixes metal salts with organic molecules to form tiny clusters, then coats them with ceramic. This process is simple and scalable for industry.
Record-Breaking Results
- 90% Energy Efficiency: At 800°C, the catalyst converts CO₂ into carbon monoxide (CO) with almost no wasted energy.
- 100% Selectivity: Every molecule of CO₂ is turned into CO, with no unwanted byproducts.
- 2,000 Hours of Operation: The catalyst keeps working for over 2,000 hours—more than 80 days—without losing effectiveness. This is a huge leap from previous technologies, which often failed after just 100 hours.
- No Precious Metals Needed: By using cobalt and nickel instead of rare metals, the cost drops dramatically.
Why Is This a Game-Changer?
1. Industrial Impact
Industries like steel, cement, and chemicals are some of the biggest emitters of CO₂. They also use huge amounts of carbon monoxide in their processes. With this new catalyst, factories could recycle their waste CO₂ into CO, creating a closed-loop system that reduces emissions and saves money.
2. Clean Energy Future
CO₂ conversion technologies can be paired with renewable energy sources (like solar or wind) to store excess electricity as chemical fuels. This helps balance the grid and supports the shift to cleaner energy.
3. Environmental Benefits
By turning a waste product into a resource, this technique supports the circular economy and helps combat climate change. It also reduces the need for fossil fuels, since the CO produced can be used to make synthetic fuels and chemicals.
Step-by-Step Guide: How CO₂ Conversion Works
Step 1: Capture the CO₂
CO₂ is collected from industrial exhaust or even directly from the air using special filters or chemical solutions.
Step 2: Prepare the Catalyst
The new catalyst is made by mixing cobalt and nickel salts with organic molecules, then coating them with a ceramic shell using the sol-gel method.
Step 3: Heat and React
The captured CO₂ is passed over the catalyst at high temperatures (around 800°C). Thanks to the encapsulated alloy, the reaction is fast, efficient, and stable.
Step 4: Collect the Product
The CO₂ is converted into carbon monoxide (CO), which can be used directly in industry or as a building block for making fuels and chemicals.
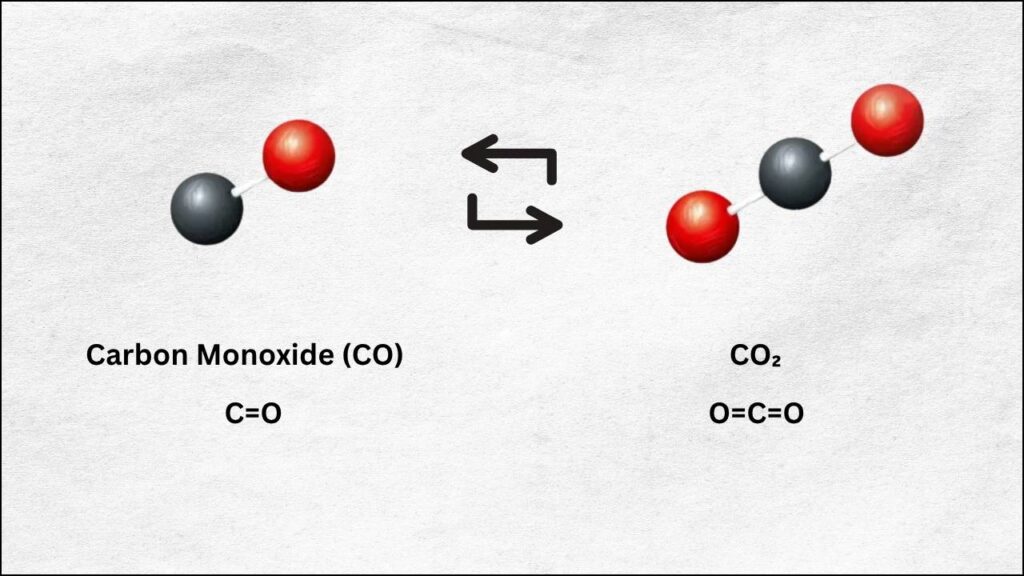
Step 5: Recycle and Repeat
The system can run continuously for thousands of hours, making it practical for real-world use.
Practical Advice for Industry and Researchers
- For Industry: Consider pilot projects to test the new catalyst in your existing CO₂ streams. The technology is compatible with current high-temperature processes and could lower both emissions and costs.
- For Policymakers: Support research and development in CO₂ conversion technologies. Incentives for adopting these systems could accelerate progress toward climate goals.
- For Researchers: Focus on optimizing catalyst design, reactor configurations, and integration with renewable energy sources. Collaboration between academia, industry, and government is key.
Researchers Discover New Method to Stabilize Ultra-Thin Materials for Next-Gen Electronics
Frontier Supercomputer Runs 5 Million Simulations to Unlock Stronger, Lighter Carbon Fiber
Amazon Unveils Project Rainier—Massive AI Chip Cluster to Train the Future of Machine Learning
FAQs About Simple Technique Improves CO₂ Conversion Efficiency
Q1: What is CO₂ conversion?
A: It’s the process of turning carbon dioxide into useful products like fuels or chemicals, helping reduce greenhouse gas emissions.
Q2: How efficient is the new technique?
A: The latest catalyst achieves 90% energy efficiency and 100% selectivity, meaning almost all the energy goes into making the desired product, with no waste.
Q3: What makes this technique “simple”?
A: The catalyst is made from common metals using a straightforward production method, and it doesn’t require rare or expensive materials.
Q4: Can this technology be used in existing factories?
A: Yes, especially in industries that already operate at high temperatures and use CO in their processes.
Q5: How does this help fight climate change?
A: By recycling CO₂ into valuable products, it reduces emissions and supports a circular economy.
The Future of CO₂ Conversion: What’s Next?
The breakthrough in catalyst design marks a major step forward, but the journey isn’t over. Future research will focus on:
- Scaling Up: Moving from lab experiments to large-scale industrial systems.
- Expanding Product Range: Developing catalysts that can make other valuable chemicals and fuels from CO₂.
- Integration with Renewables: Pairing CO₂ conversion with solar, wind, or other green energy sources for maximum impact.
- Policy and Investment: Encouraging governments and companies to invest in these technologies for a sustainable future.