The U.S. Army, in partnership with leading academic institutions, has announced a groundbreaking development in materials science: a revolutionary copper alloy known as Cu-Ta-Li (Copper-Tantalum-Lithium) that offers unprecedented strength, durability, and thermal stability while maintaining copper’s excellent electrical and thermal conductivity. Designed specifically for demanding military and aerospace applications, this “super-copper” combines the best properties of copper with advanced nanostructuring to excel in extreme environments where traditional metals fail.
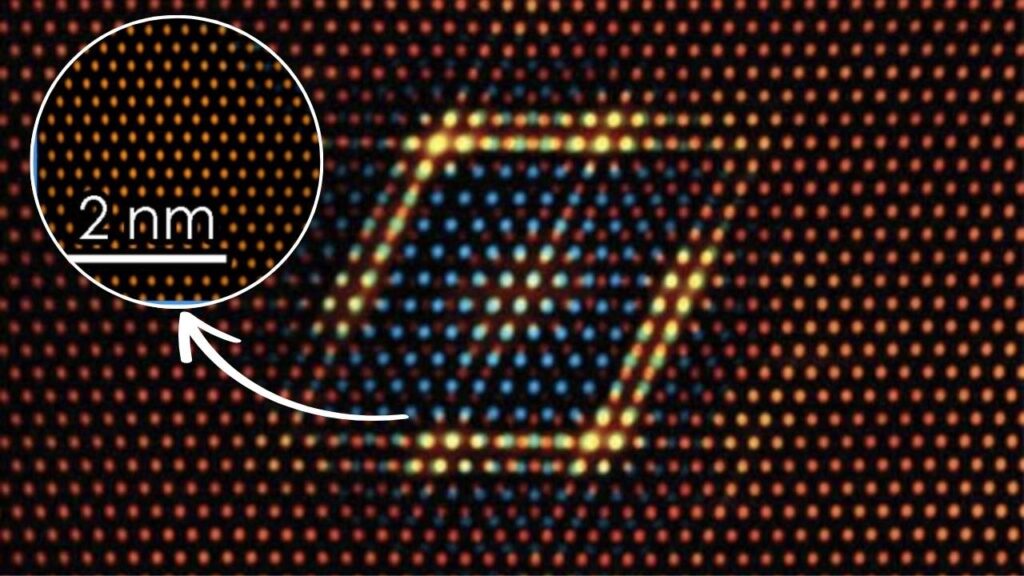
Introduction: Why This Breakthrough Matters
Copper has long been a cornerstone in electrical, thermal, and structural applications due to its superior conductivity and corrosion resistance. However, its mechanical weakness and susceptibility to degradation at high temperatures—typically above 400°C (752°F)—have limited its use in aerospace propulsion systems, advanced weaponry, hypersonic vehicles, and thermal management systems.
Traditional copper alloys sacrifice some conductivity to gain strength but still fall short under extreme heat and mechanical stress. The Cu-Ta-Li alloy disrupts this compromise, combining an ultra-strong nanocrystalline structure stabilized through atomic bilayer interfaces, ensuring exceptional mechanical performance and thermal stability up to 800°C (about 1500°F). This advancement signifies a paradigm shift in metal design and potential uses.
Army and Researchers Create Super-Copper
Key Feature | Details |
---|---|
Alloy Name | Cu-Ta-Li (Copper-Tantalum-Lithium) |
Developed By | U.S. Army Research Laboratory, Arizona State University, Lehigh University, Louisiana State University |
Yield Strength | Approximately 1120 MPa at room temperature, rivaling nickel-based superalloys |
Thermal Stability | Maintains strength after 10,000+ hours exposure at 800°C (1500°F) |
Electrical & Thermal Conductivity | Retains nearly the same conductivity as pure copper, outperforming many other high-strength alloys |
Weight | Lighter than conventional copper alloys and some nickel-based superalloys |
Applications | Military weaponry, hypersonic vehicles, aerospace propulsion, thermal management, modular nuclear reactors |
Funding & Research Duration | Over a decade of research supported by a $25 million cooperative agreement |
Official Reference | Army Research Laboratory (ARL) release |
The Cu-Ta-Li super-copper alloy marks a milestone in material science, demonstrating how nanoscale engineering and atomic interface control can yield metals with exceptional multi-property performance. This innovative material delivers unmatched strength, heat resistance, and conductivity, addressing critical challenges in military, aerospace, and energy technologies.
By protecting structural integrity under extreme conditions while enabling lighter, more efficient designs, super-copper will likely redefine standards in high-performance materials for decades to come. The collaboration between the U.S. Army and leading universities highlights the power of interdisciplinary and applied research in delivering materials that not only fill a technological gap but open new possibilities.
Delving Deeper: The Science Behind Cu-Ta-Li
Nanostructuring and Alloy Composition
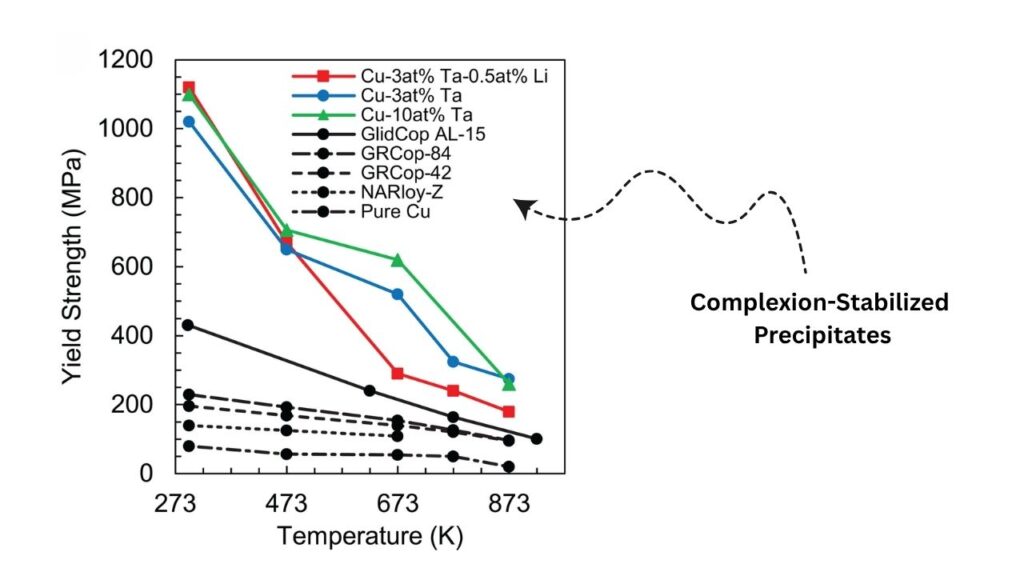
The alloy’s core innovation lies in its nanocrystalline structure—an arrangement where the copper grains are only a few nanometers in size. Smaller grains typically enhance strength (due to grain boundary strengthening) but come with the drawback of grain growth at high temperatures, which weakens metals.
Cu-Ta-Li overcomes this by introducing a specialized atomic bilayer “complexion”, a term in materials science for thermodynamically stable layers that form at grain boundaries. These layers:
- Contain a tantalum-rich interface that bonds tightly to copper grains.
- Host copper-lithium precipitates that prevent grain growth.
This design arrests grain coarsening and keeps the structure stable at high temperatures for exceptionally long durations (over 10,000 hours at 800°C).
Mechanical and Thermal Advantages
- Strength: At room temperature, the alloy achieves a yield strength near 1120 MPa (~162,000 psi), comparable to nickel-based superalloys widely used in jet engines.
- Thermal Stability: Unlike conventional copper, which softens and loses strength at temperatures typically above 400°C (752°F), Cu-Ta-Li maintains its strength at temperatures nearing copper’s melting point, around 1085°C (1985°F).
- Electrical Conductivity: Importantly, the alloy preserves copper’s high electrical and thermal conductivity (greater than 80% IACS, International Annealed Copper Standard), enabling efficient heat dissipation and energy transmission.
This combination of mechanical strength and conductivity is a rare and valuable property that expands copper’s usability.
Why This Matters for Military and Aerospace Technologies
Extreme Operational Environments
Military and aerospace systems often endure:
- Hypersonic flight temperatures, which can reach thousands of degrees Fahrenheit and apply intense thermal shock.
- High mechanical loading and vibration in missile systems or aircraft components.
- Thermal cycling during launches or operational pulses.
Current materials like nickel-based superalloys provide strength but are heavier and less conductive than copper, impacting system efficiency and weight.
Potential Practical Applications
- Hypersonic Missile and Aircraft Components: The alloy can serve in propulsion nozzles, heat exchangers, and thermal shields where high temperature resistance and weight savings are critical.
- Advanced Weapon Systems: Heat dissipation from directed energy weapons or electromagnetic railguns can be improved without compromising structural integrity.
- Thermal Management in Electronics: Copper’s conductivity maintains reliable heat flow, preventing overheating in sensitive electronic components exposed to battle conditions.
- Energy Sector Technologies: The alloy’s stability under irradiation and heat suits modular nuclear reactors for battlefield energy generation.
By enabling lighter, tougher, and more thermally stable components, Cu-Ta-Li can enhance system longevity, safety, and performance.
How This Innovation Was Achieved: Collaborative Research Excellence
This project was spearheaded by the U.S. Army Research Laboratory in close collaboration with:
- Arizona State University (ASU) – specializing in materials characterization and nanotechnology.
- Lehigh University – expert in atomic interface science and complexion design.
- Louisiana State University (LSU) – providing advanced modeling and alloy development.
Funded through a $25 million program, the interdisciplinary work included:
- Synthesis of alloys via powder metallurgy and rapid solidification.
- Detailed microscopy (TEM, SEM) to observe nanoscale structures.
- Mechanical testing under relevant thermal and mechanical loads.
- Computer simulations to optimize interface chemistry and structure stability.
This long-term effort builds on prior research into grain boundary engineering and complexion science pioneered by Lehigh University.
Practical Guide for Industry Professionals
- Material Selection Strategy: Incorporate Cu-Ta-Li into design considerations where competing demands for strength, weight, and conductivity exist, such as aerospace propulsion components and military electronics enclosures.
- Testing and Qualification: Plan rigorous environmental and mechanical testing to validate performance under specific operational conditions, as scaled manufacturing progresses.
- Design Innovation: Utilize the alloy’s reduced weight to improve fuel efficiency in aircraft or increase payload capacity in missile systems.
- Collaborate & Monitor Licensing: Track commercial availability through technology transfer offices and emerging industry partnerships with ARL and university partners.
- Advance Research: Materials scientists should explore further alloy optimizations and hybrid combinations to tailor properties for niche applications.
Scientists Develop Breakthrough Copper Composite With Superior Strength and Conductivity
New Copper Alloy Works in −200 °C Temps — Designed for Space, and It Remembers Its Shape
Breakthrough Turns Sugarcane Waste Into Clean Hydrogen — With Almost Zero Emissions
FAQs About Army and Researchers Create Super-Copper
Q1: How does Cu-Ta-Li differ chemically from traditional copper alloys?
Traditional copper alloys often add elements like zinc (to make brass) or tin (bronze) but sacrifice conductivity for strength. Cu-Ta-Li uniquely integrates tantalum and lithium at nanoscale interfaces without disrupting copper’s electron flow, maintaining conductivity while dramatically increasing strength.
Q2: Can this alloy withstand the radiation environment in nuclear applications?
While specific radiation testing is ongoing, the nanostructured design and stable interfaces suggest high resistance to radiation-induced damage and swelling, essential for modular nuclear reactors on battlefields.
Q3: What manufacturing methods are compatible with Cu-Ta-Li?
Current development employs advanced powder metallurgy and thermo-mechanical processing, but efforts are underway to adapt it to conventional casting and additive manufacturing for scalability.
Q4: Is this super-copper environmentally sustainable?
Copper alloys generally have high recyclability. The added elements (tantalum and lithium) are used in small amounts but are sourced responsibly, aligning with sustainable defense material initiatives.
Q5: When will this alloy be commercially available?
Technology transfer is in progress with partnerships focusing on aerospace and defense sectors. Wider commercial availability is expected over the next 3-5 years as manufacturing matures.