Hydrogen and ammonia are essential to modern life—hydrogen as a clean energy carrier, and ammonia as the foundation of fertilizers that feed the world. Producing both at scale, however, has historically demanded massive amounts of energy and emitted substantial greenhouse gases. Now, engineered ruthenium catalysts are poised to change that, making the industrial-scale production of hydrogen and ammonia cleaner, more efficient, and more accessible than ever.
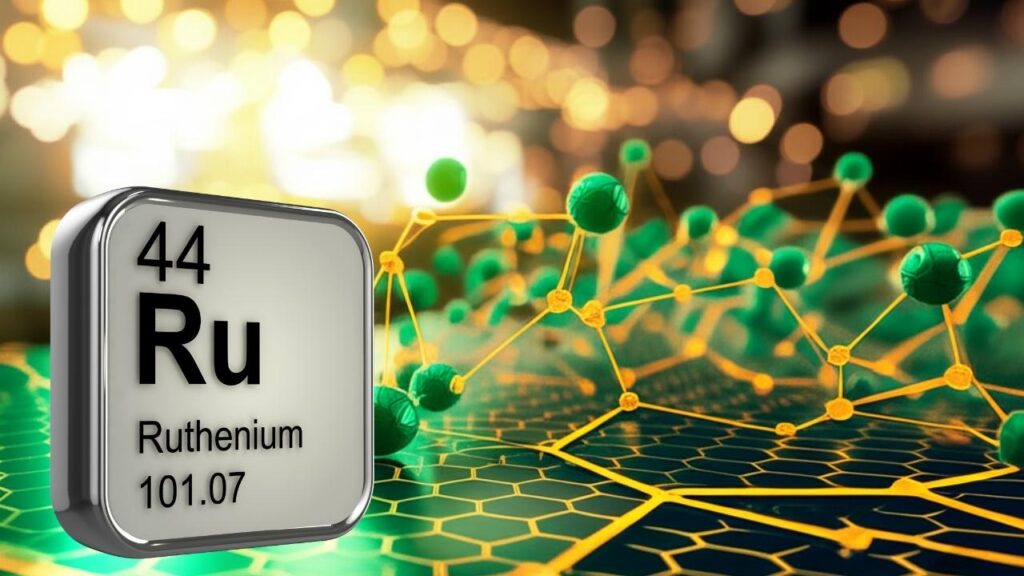
Why This Matters
Hydrogen’s promise lies in its potential to fuel cars, buses, and even entire cities with zero CO₂ emissions—only water vapor comes out of the tailpipe. But producing hydrogen cleanly and affordably remains a global challenge. Green hydrogen—made by splitting water using renewable electricity—is the gold standard, but current methods are still too expensive for widespread use. Meanwhile, ammonia is critical for global food production, but conventional ammonia synthesis accounts for over 1% of the world’s total energy consumption and millions of tons of CO₂ emissions each year (International Energy Agency).
Catalysts—materials that speed up chemical reactions without being consumed—have always been at the heart of these processes. Traditionally, nickel and iron catalysts have been used, but they require high temperatures and pressures, and often suffer from stability problems. Ruthenium, a precious metal with unique catalytic properties, now offers a more efficient, durable, and potentially greener alternative—especially when engineered with precision.
Engineered Ruthenium Catalysts
Topic | Key Points | Data/Stats/Details | Professional Insight |
---|---|---|---|
Ruthenium Catalyst Role | Drives hydrogen and ammonia reactions with higher efficiency and at lower temperatures than traditional catalysts | Up to 10% higher ammonia yield at 400°C | Critical for green energy and sustainable fertilizer production |
Production & Energy Use | Enables ammonia synthesis at reduced temperatures and pressures, lowering energy needs and emissions | 100–200°C lower than classic Haber–Bosch, lower pressure | Reduces operational costs and environmental impact |
Material Cost | Ruthenium is expensive, but advanced engineering and recycling can improve economic viability | 30–100 times higher cost than nickel | Scalability depends on material supply, recycling, and process innovation |
Catalyst Structure | Can be engineered into nanoclusters for maximal active surface area, improving efficiency and reducing metal needed | 2–3 nanometer clusters, high activity-per-atom ratio | Atomic-scale control enables tailored catalysts for specific applications |
Ammonia as H₂ Carrier | Ruthenium enables efficient “cracking” of ammonia into hydrogen on demand, supporting flexible hydrogen distribution | Stable and selective hydrogen release | Enables decentralized and safe hydrogen storage/transport |
Manufacturing Methods | Magnetron sputtering and other clean techniques allow high-precision, low-waste production | Minimal solvent use, scalable, clean process | Supports large-scale, eco-friendly catalyst manufacturing |
Engineered ruthenium catalysts represent a major step forward in the quest for sustainable hydrogen and ammonia production. By enabling lower-temperature, lower-energy processes, reducing greenhouse gas emissions, and supporting flexible, decentralized systems, these materials have the potential to transform both agriculture and energy for the better.
Cost and scalability remain real-world challenges, but ongoing research, smart engineering, and supportive policies are narrowing the gap. In a world hungry for clean energy and sustainable agriculture, ruthenium catalysts—when paired with renewable electricity and smart industrial design—are poised to play a pivotal role.
What Is a Catalyst, and Why Is Ruthenium Special?
A catalyst is a substance that increases the rate of a chemical reaction without being consumed itself. In essence, it lowers the energy barrier for a reaction—making it happen faster, with less energy input. For large-scale industrial processes like making ammonia, catalysts save vast amounts of energy and resources.
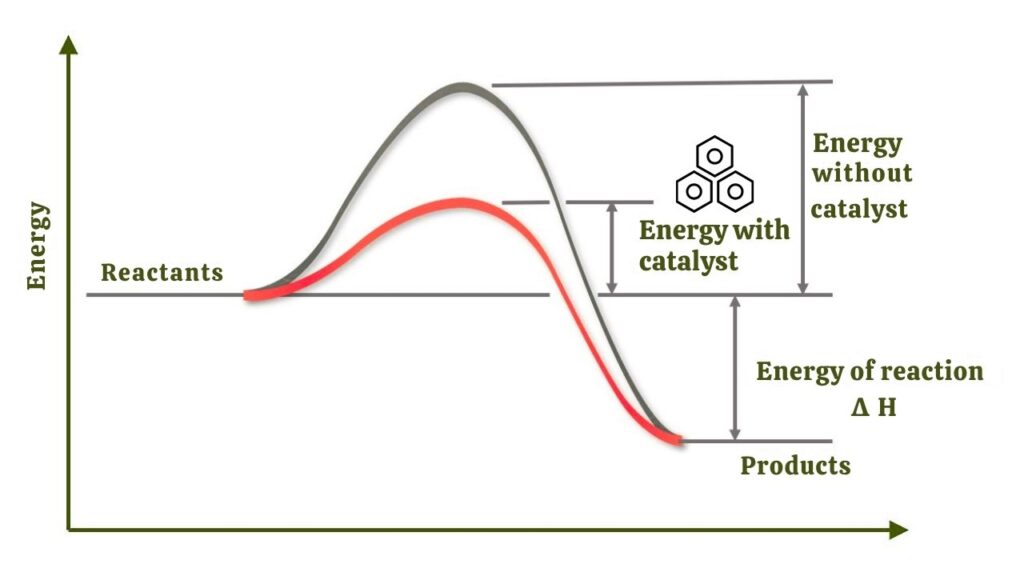
Ruthenium is a member of the platinum group metals, rare and precious but exceptionally good as a catalyst. Its distinguishing features include:
- High activity: Ruthenium facilitates reactions like nitrogen fixation (turning nitrogen gas into ammonia) at rates far faster than iron or nickel.
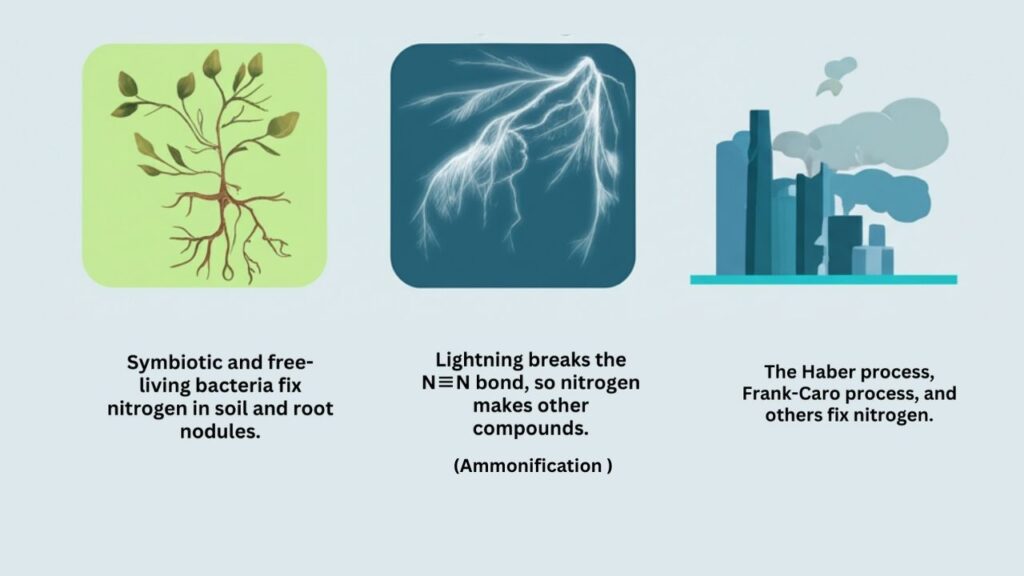
- Lower temperature operation: It can promote ammonia synthesis at temperatures 100–200°C cooler than traditional catalysts, reducing energy costs.
- Selectivity: Ruthenium is less prone to unwanted byproducts, making processes more efficient and less wasteful.
- Stability: It resists poisons—impurities or unwanted side-reactions—better than many alternatives.
However, ruthenium’s rarity and cost have limited its adoption—until now. Engineering at the atomic scale is changing the game, using precise techniques to maximize the effectiveness of every ruthenium atom.
How Are Engineered Ruthenium Catalysts Made?
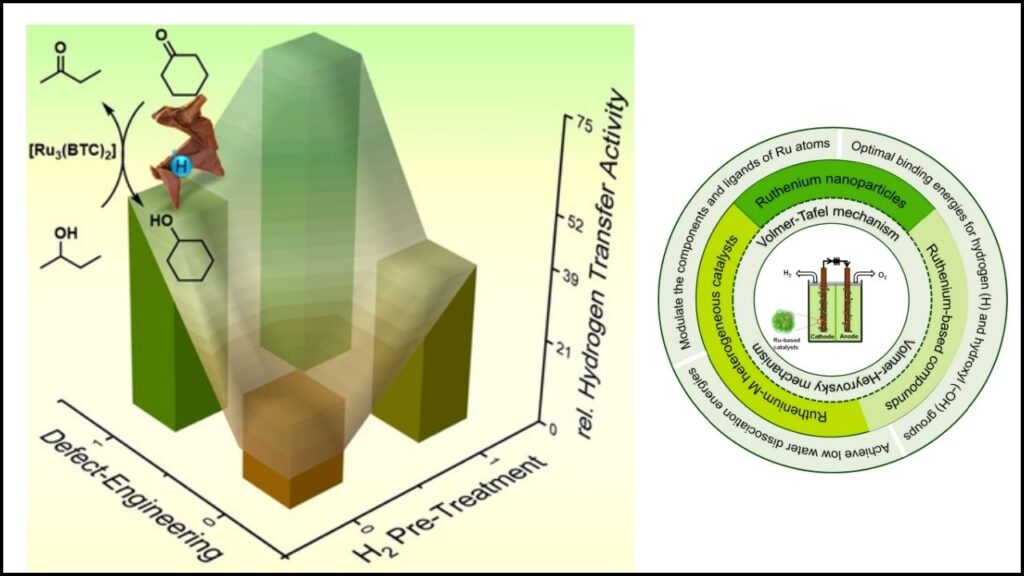
Step 1: Designing Active Surfaces
Older catalysts were often large particles or pellets. Most of the ruthenium was buried inside, unable to participate in the reaction. Modern engineered ruthenium catalysts are built as nanoclusters, tiny particles only a few nanometers wide—so small that most atoms are exposed on the surface, ready to react.
Methods like magnetron sputtering or wet chemistry deposit ruthenium atoms in tightly controlled patterns. This atom-by-atom precision means the catalyst can be optimized for each specific reaction, whether it’s ammonia synthesis or hydrogen extraction.
Step 2: Preventing Catalyst Poisoning
A challenge in catalytic chemistry is “poisoning”—when unwanted molecules (like sulfur or carbon monoxide) stick to the catalyst and block its activity. Ruthenium is already more resistant to poisoning than nickel or iron, but scientists have found that tailoring the support material (the substance that holds the catalyst) can further protect ruthenium.
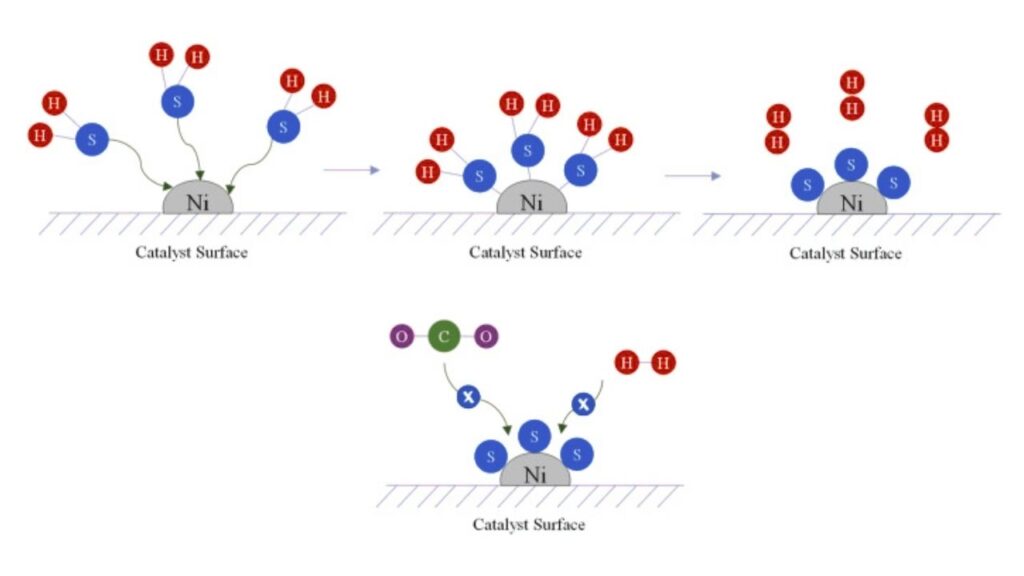
Supports like carbon, lanthanide oxyhydrides, or silicon carbide protect the clusters, promote electron transfer, and prevent unwanted side-reactions. Some supports even help “clean” the catalyst on the fly, keeping it active for longer.
Step 3: Boosting Activity with Promoters
Promoters are elements or compounds added in tiny amounts to boost the catalyst’s performance. For ruthenium catalysts, alkali or alkaline earth metals (like potassium or calcium) are often used. They help regulate the electronic environment, making it easier for nitrogen or hydrogen atoms to bond and react.
Step 4: Durable and Recyclable Catalysts
Ruthenium is expensive—several times more costly than nickel, by weight. To make these catalysts practical for large-scale use, researchers are focusing on durability and recyclability. By making ruthenium particles as small and efficient as possible, less metal is needed. And since ruthenium does not break down during use, the precious metal can be recovered and reused, reducing both cost and environmental impact.
Real-World Applications and Benefits
For Agriculture: Cleaner Fertilizer Production
Ammonia synthesis is the foundation of nitrogen fertilizer, which underpins global food security. The Haber–Bosch process, invented in the early 1900s, has fed billions—but at a steep environmental cost. Engineering ruthenium catalysts offers a path to greener ammonia production: lower temperatures, less energy, fewer emissions, and more efficient resource use.
This could reduce the carbon footprint of agriculture, make fertilizers more affordable, and support more sustainable farming practices worldwide.
For Energy: Green Hydrogen and the Ammonia Economy
Hydrogen is an ideal clean fuel—when burned, it produces only water. But storing and transporting hydrogen is challenging: it’s a gas at room temperature, and it leaks easily. One solution is to convert hydrogen into ammonia, which is easier to transport and store. When hydrogen is needed, ruthenium catalysts can efficiently “crack” ammonia back into hydrogen and nitrogen.
This hydrogen-from-ammonia cycle is promising for decentralized energy systems—local hydrogen fuel stations, backup power, and remote communities. It also offers a bridge between intermittent renewable energy and constant fuel needs.
For Industry: Modular, On-Demand Chemical Production
Traditional hydrogen and ammonia plants are gigantic, centralized, and capital-intensive. Ruthenium’s ability to work at lower temperatures and pressures makes smaller, modular reactors practical. This could allow on-site ammonia synthesis in rural areas, or local hydrogen production for communities, reducing the need for costly infrastructure and long-distance transport.
Challenges and Looking Ahead
Despite these exciting possibilities, ruthenium catalysts are not a silver bullet.
- Cost remains a major hurdle. Ruthenium is rare, and while engineering and recycling help, the metal is still far more expensive than iron or nickel.
- Scale-up is complex. Moving from lab breakthroughs (grams of catalyst) to industrial-scale (tons per year) demands not just material science, but process engineering, supply chain management, and cost control.
- Materials innovation is ongoing. Finding cheaper substrates, optimizing promoters, and improving durability are all active research frontiers.
- Policy and market incentives matter. For green hydrogen and clean ammonia to reach their potential, governments and businesses must align on incentives for investment and adoption.
Researchers are tackling these challenges with a mix of scientific creativity and industrial pragmatism. Progress in nanomaterials, recycling technologies, and process integration continues to bring down costs and expand applications.
New Triple-Layer Catalyst Boosts Green Hydrogen Output by 800%—A Game-Changer for Clean Energy
Breakthrough Catalyst Efficiently Converts CO₂ Into Methanol With High Precision
Cobalt-Based Catalyst Offers an Effective Alternative to Precious Metals
FAQs About Engineered Ruthenium Catalysts
Q: Why are ruthenium-based catalysts more efficient than traditional ones?
A: Ruthenium is inherently more active for certain reactions, especially nitrogen fixation and ammonia decomposition. When engineered into nanoclusters, its entire surface becomes available for catalysis, dramatically increasing efficiency. Additionally, ruthenium is less susceptible to poisoning and can operate at lower temperatures, saving energy and reducing emissions.
Q: Is ruthenium too expensive for large-scale use?
A: Ruthenium is one of the most expensive platinum-group metals, but advanced engineering allows for very small amounts to be used—maximizing activity per atom. Furthermore, ruthenium can be recovered and recycled after use, which improves cost-effectiveness over time.
Q: Can I see these technologies in action today?
A: Some laboratories and pilot plants are testing ruthenium-based catalysts for both hydrogen and ammonia production. Broader industry adoption is not yet widespread but is advancing rapidly as costs fall and performance improves.
Q: What are promoters and supports? Why are they important?
A: Promoters are additives (often alkali or alkaline earth metals) that boost the catalyst’s activity, sometimes by controlling electron transfer or stabilizing reaction intermediates. Supports are materials (like carbon or silicon carbide) that hold the catalyst in place and help maintain its structure and activity. Both are crucial for achieving high performance in real-world conditions.
Q: What are the main barriers to adoption?
A: The biggest challenges are the high cost of ruthenium, the need for industrial-scale production methods, and the development of infrastructure for new fuels like green hydrogen and ammonia. Continued innovation in catalysis, recycling, and process engineering will be key to overcoming these barriers.