3D printing technology has dramatically evolved with a game-changing breakthrough that enables the combination of multiple materials—including vastly different plastics and metals—in a single seamless print. This advance overcomes long-standing hurdles in manufacturing and opens the door to innovation across various industries like medicine, automotive, aerospace, and electronics. Whether you’re new to 3D printing or an industry expert, this detailed article unpacks the science, practical uses, and future potential of multi-material printing in an easy-to-understand yet authoritative manner.
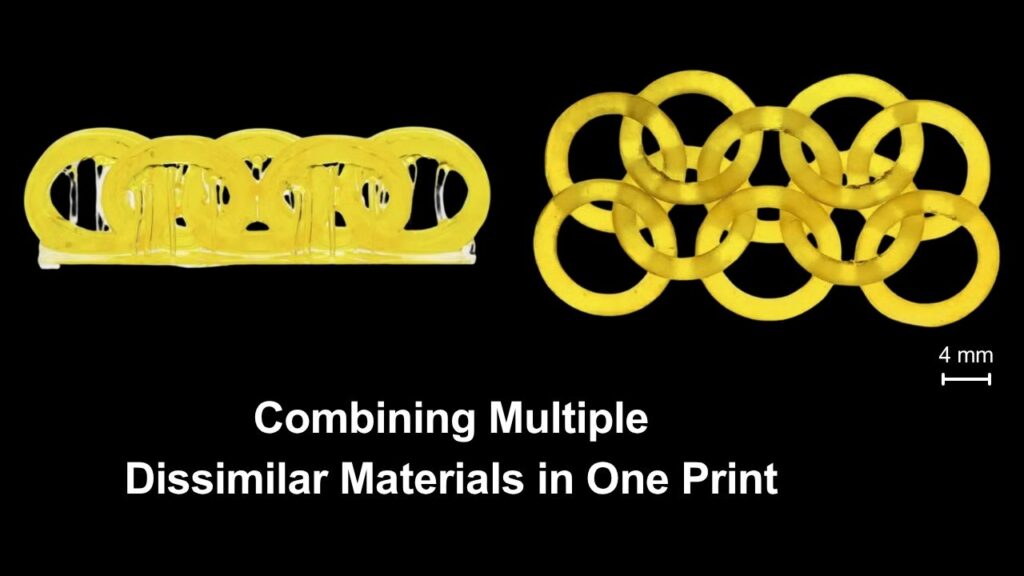
You’ll also find a helpful Key Highlights table, a step-by-step guide, practical examples, and FAQs to provide clarity and actionable insights on this transformative technology.
Game-Changing 3D Printing Breakthrough
Topic | Details |
---|---|
Breakthrough Focus | Combining multiple, dissimilar materials (flexible polymers, metals, hard plastics) in one print |
Leading Institutions | University of Texas at Austin, Tohoku University, Lawrence Livermore National Laboratory |
Key Materials | Flexible rubber-like resins, hard plastics, aluminum, steel, bronze, advanced polymers |
Applications | Medical devices, automotive parts, aerospace components, wearable electronics |
Challenges Solved | Stronger bonding at material interfaces, reduced brittleness of mixed metals |
Production Benefits | Reduced assembly steps, complex geometries, enhanced customization, material efficiency |
Future Outlook | Wider industrial adoption, smarter lightweight materials, self-healing structures |
Official Reference | University of Texas 3D Printing Research |
Multi-material 3D printing represents a major leap in manufacturing, allowing the seamless integration of diverse materials—flexible and rigid, metals and polymers—in one build. This breakthrough holds promise for transforming industries by enabling complex, durable, and multifunctional products with fewer steps and new design freedoms. As the technology matures, expect lighter, stronger, smarter, and more personalized products emerging from 3D printers worldwide, shaping the future of manufacturing.
What Is Multi-Material 3D Printing?
Traditional 3D printing typically uses one material per print—like a plastic or a metal—limiting the functional complexity of the final piece. Multi-material 3D printing integrates different materials with unique properties, such as flexibility, hardness, and conductivity, into a single printed object without assembly. This capability allows manufacturers to create parts that combine softness and rigidity, lightweight and strength, or insulation and conductivity, all in one build.
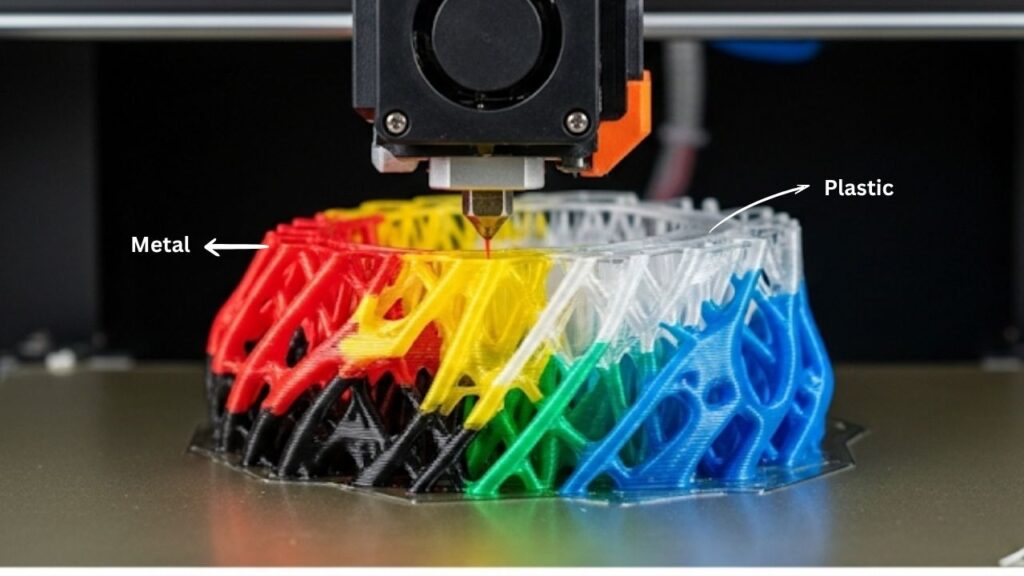
Picture printing a robotic hand where the bones are rigid but enveloped by soft, stretchable skin; or an automotive part combining aluminum’s lightness with steel’s strength—both produced in one seamless, efficient process. This is the future unlocked by this breakthrough.
The Science Behind Multi-Material 3D Printing Breakthroughs
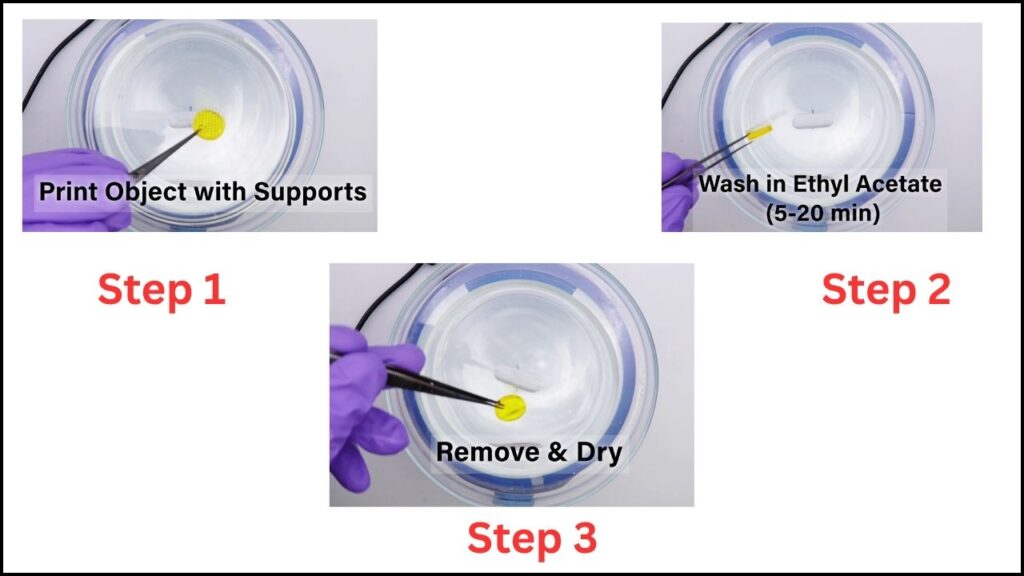
Multiple cutting-edge innovations have converged to enable this technology:
1. Dual-Function Resins Controlled by Light Color
At the University of Texas at Austin, researchers developed a single liquid resin that responds differently to various light wavelengths. Under violet light, the resin cures into a soft, rubbery material; ultraviolet light turns it into a hard, durable plastic. This dual-light photopolymerization technique creates strong chemical bonds between soft and hard parts, eliminating weak interfaces and enabling smooth material transitions.
Example: They 3D printed a knee joint with flexible ligaments and hard bones that articulate naturally. Another prototype was a stretchable electronic device with rigid sections protecting circuits without compromising flexibility.
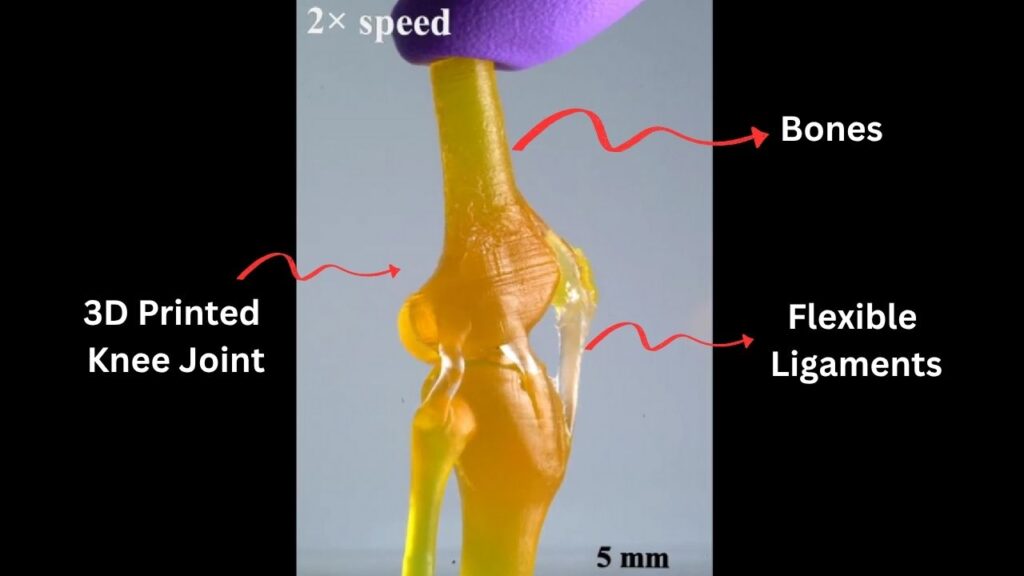
2. Multi-Material Metal Printing with Controlled Interfaces
Scientists at Tohoku University advanced laser powder bed fusion (L-PBF) by optimizing laser parameters to print dissimilar metals like aluminum and steel in one part while controlling the formation of brittle intermetallic compounds that traditionally weaken metal interfaces. This method produces lightweight yet durable parts, such as automotive suspension components, by leveraging the strengths of each metal.

3. Cellular Fluidics for Hybrid Structures
Researchers at Lawrence Livermore National Laboratory (LLNL) created a cellular fluidics technique using small lattice structures that guide different liquids by capillary action during printing. After solidification, this forms parts that combine soft and hard materials, enabling applications like self-healing structures, advanced biomedical implants, and lightweight aerospace components.
4. Combinatorial Nanomaterial Printing
High-throughput printing systems can mix multiple nanomaterial inks during fabrication, enabling microscopic control over material properties within a single object. This technique accelerates materials discovery, allows fine-tuned gradations of flexibility or conductivity, and speeds up prototyping of multifunctional parts.
Practical Applications of Multi-Material 3D Printing
The technology impacts many industries in concrete ways:
Medical Devices and Prosthetics
- Custom implants with flexible joints and rigid bones for better comfort and durability.
- Stretchable electronic sensors embedded directly into prosthetic limbs.
- One-piece dentures simulating hard enamel and soft gums, speeding production and improving fit.
Automotive and Aerospace
- Parts combining lightweight aluminum with tough steel for improved performance and fuel efficiency.
- Components with mixed polymers and metal alloys designed for thermal resilience and strength.
- Reduction in assembly steps, enabling more complex, integrated multi-material systems.
Electronics and Wearables
- Embedded circuit boards printed with plastic housings and metal contacts simultaneously.
- Flexible wearable gadgets that conform to skin while maintaining reliable circuits.
Emerging Applications
- Self-healing materials for infrastructure that repair cracks automatically.
- Carbon capture devices optimized through hybrid material design.
How Multi-Material 3D Printing Works: A Step-By-Step Guide
- Design the Object: Engineers use specialized CAD software to assign different materials to specific parts of a model, defining the zones for flexibility, hardness, or conductivity.
- Prepare Materials and Setup: Select compatible resins, metal powders, or inks. Multi-material printers may have multiple print heads or specialized light sources to cure different materials selectively.
- Printing Process:
- For resin printing, varying light wavelengths cure different materials in one continuous print.
- Metal printing uses distinct laser parameters to selectively melt and bond different metal powders.
- Cellular fluidics creates micro-lattice scaffolds that guide material placement through surface tension.
- Post-Processing: Minimal cleaning might be needed; some prints require dissolving temporary supports or heat treatment to strengthen bonds.
- Testing and Validation: Mechanical and functional tests confirm interface strength and overall part performance.
Challenges and How They Are Overcome
- Interface Weakness: The main issue is bond failure where materials meet. Dual-light curing resins and chemically compatible monomers create strong, gradual bonds rather than brittle junctions.
- Brittle Metal Interfaces: Multi-metal parts traditionally suffer brittleness due to unwanted compounds. Precise laser melting and rapid solidification suppress these formations, increasing durability.
- Material Compatibility: Not all materials mix easily; new tailored resins and inks are expanding compatibility, enabling more combinations.
- Scalability and Cost: High-tech multi-material printers and materials can be costly, but automation and recycling strategies are helping reduce costs and improve production scale.
MIT Engineers Develop New 3D Printing Method to Reduce Waste and Enable Complex Designs
Advancements in 3D Printing: How New Materials Are Expanding Possibilities
Cold Spray 3D‑Printing Technique Proves Effective For On‑Site Bridge Repair
FAQs About Game-Changing 3D Printing Breakthrough
Q1: What industries benefit most from multi-material 3D printing?
A1: Medical, aerospace, automotive, electronics, and advanced manufacturing sectors benefit greatly due to customized complex parts with multiple functionalities.
Q2: Can multi-material 3D printed parts match traditional manufacturing strength?
A2: Yes, especially with improved interface bonding techniques, many printed parts meet or exceed the mechanical properties of conventionally manufactured components.
Q3: How is flexibility controlled in a single printed object?
A3: Through use of resins that cure differently under specific light colors or by mixing materials with distinct mechanical properties in defined areas.
Q4: When will multi-material 3D printing be widely available?
A4: Many commercial systems already exist in medical and aerospace fields; wider industrial adoption is expected within the next few years.
Q5: What skills are needed to operate advanced multi-material 3D printers?
A5: Knowledge of materials science, digital design (CAD), and additive manufacturing processes is crucial for optimal use.