If you’ve ever held a smartphone that felt too hot to touch, or watched your laptop slow down on a summer afternoon, you’ve witnessed a common problem: electronics overheating. For years, engineers and designers have relied on metals—like aluminum and copper—to whisk heat away from sensitive electronic components. Metals are excellent at conducting heat, but they’re also heavy, expensive, and can cause electrical shorts if they accidentally touch the wrong parts. Now, a quiet revolution is changing the game: heat-conductive plastics. These advanced materials promise to keep our gadgets cool, safe, and lightweight—without the drawbacks of metal.
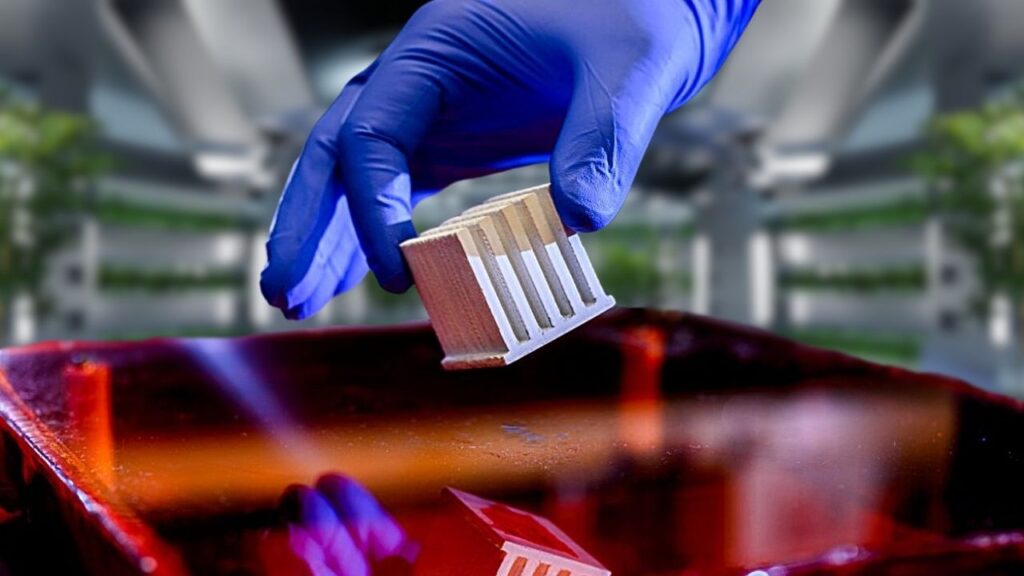
Imagine a plastic that doesn’t just insulate, but actually channels heat away from hotspots. Sounds like science fiction? It’s not. Thanks to breakthroughs in materials science, heat-conductive plastics are already being used in cars, phones, and industrial equipment. In this article, we’ll explore how these plastics work, why they matter, and how they could shape the future of electronics—whether you’re a curious student, a tech enthusiast, or a professional engineer.
Heat-Conductive Plastics
Aspect | Details |
---|---|
Market Growth | Thermal conductive plastics market is growing rapidly, driven by demand in electronics and automotive sectors. |
Top Materials | Polycarbonate, nylon, and other engineering plastics with ceramic or mineral fillers. |
Thermal Conductivity | Advanced composites can reach 1–10 W/m·K, rivaling some metals. |
Lightweight Advantage | Plastic heat sinks can be half the weight of aluminum equivalents. |
Key Applications | LED lighting, battery casings, electronic enclosures, automotive sensors. |
Leading Companies | Covestro, Celanese, Lanxess, SABIC, and others. |
Professional Insight | Enables lighter, cheaper, and more energy-efficient electronic components. |
Heat-conductive plastics are transforming how we keep electronics cool. By combining the best of plastics—light weight, electrical insulation, and design flexibility—with the heat-spreading power of advanced fillers and smart engineering, these materials are solving one of the biggest challenges in modern technology. Whether you’re building the next smartphone, designing a car, or just curious about how stuff works, these innovative plastics are worth watching—and using.
Why Do Electronics Need Cooling?
Electronics, from your smartphone to the computer in your car, generate heat whenever they’re in use. This heat comes from the movement of electrons through circuits—a bit like how rubbing your hands together makes them warm. If this heat isn’t removed, it can cause components to fail, reduce performance, or even start a fire in extreme cases.
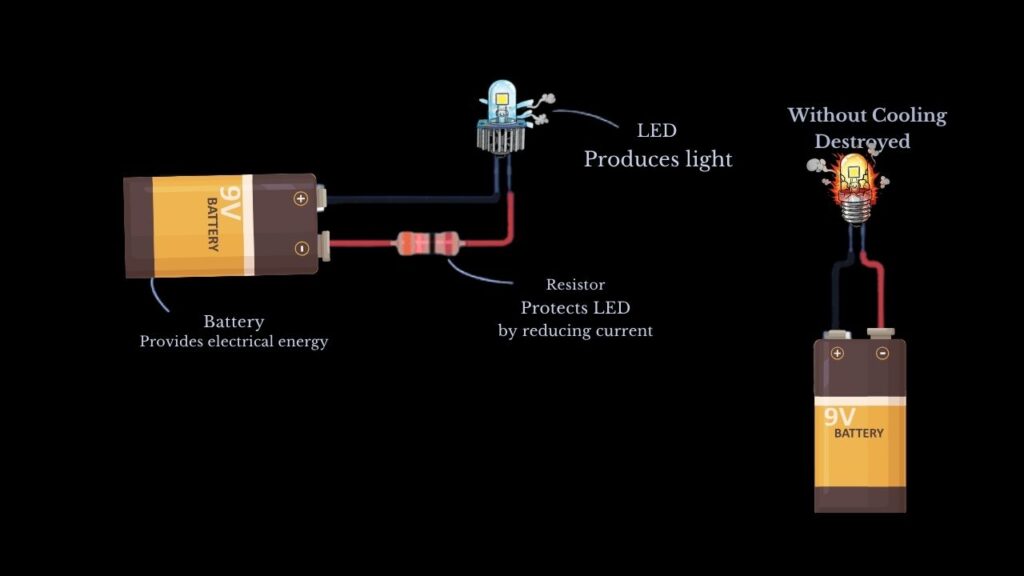
Traditionally, metal heat sinks—chunky pieces of aluminum or copper—are attached to hot components to pull heat away. While effective, these metal parts add weight, cost, and complexity. They can also cause electrical problems if they accidentally touch sensitive circuits. That’s where heat-conductive plastics come in: they promise to solve these problems by being lightweight, electrically insulating, and easy to shape into complex designs.
How Do Heat-Conductive Plastics Work?
At first glance, heat-conductive plastics look and feel like ordinary plastic. The magic is inside: scientists have found ways to make plastic conduct heat almost as well as metal, while keeping its other advantages.
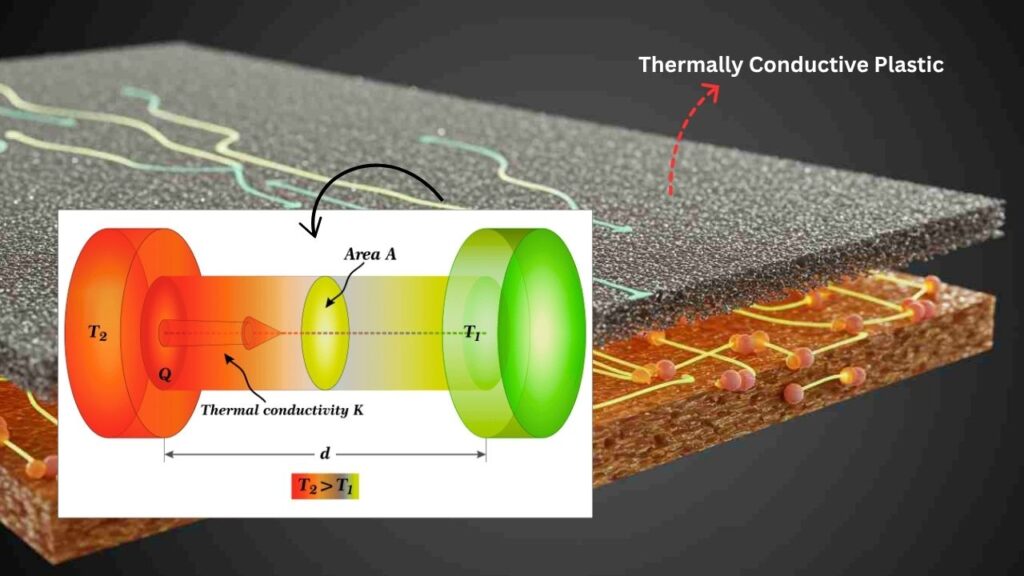
The Science Behind the Magic
Ordinary plastics are thermal insulators—they trap heat. Heat-conductive plastics are engineered to let heat flow through them. Here’s how it’s done:
- Adding Special Fillers: By mixing plastic with tiny particles of ceramics (like boron nitride or aluminum oxide), researchers create a composite material that can channel heat. The right mix is crucial—too much filler makes the plastic brittle; too little, and it stays insulating.
- Engineering the Structure: Some research teams use advanced manufacturing techniques, like 3D printing, to arrange these filler particles in a precise network. This creates “thermal highways” inside the plastic, allowing heat to travel efficiently.
- Modifying the Plastic Itself: In some cases, scientists alter the plastic’s molecular structure to improve heat flow, without adding heavy fillers. This approach can be cheaper and works with many types of plastic.
- Innovative Polymer Films: New types of polymer films, developed by leading universities, can conduct heat much better than traditional plastics. These films are thin, flexible, and can be coated directly onto electronic components.
Real-World Examples
- Automotive Lighting: Heat-conductive plastics are used in LED headlight and fog light housings for cars and trucks. They replace metal parts, reducing weight and cost while keeping the lights cool.
- Electronics Casings: Smartphones, laptops, and tablets can use these plastics in their casings to pull heat away from processors and batteries, improving performance and battery life.
- Battery Packs: Electric vehicles and portable electronics benefit from plastic battery casings that keep cells cool, enhancing safety and lifespan.
- Industrial Sensors: In factories, these plastics protect sensitive electronics from overheating, even in harsh environments.
- Custom 3D-Printed Parts: With 3D printing, engineers can create complex, lightweight cooling structures tailored to specific devices—something that’s difficult or impossible with metal.
Benefits Over Traditional Materials
Let’s compare heat-conductive plastics to traditional metal heat sinks:
Feature | Metal Heat Sinks | Heat-Conductive Plastics |
---|---|---|
Weight | Heavy | Up to 4x lighter |
Electrical Safety | Can cause shorts | Insulating—safe around circuits |
Cost | Expensive to machine | Cheaper, especially with mass production |
Design Flexibility | Limited by machining | Highly customizable, even complex shapes |
Thermal Conductivity | Very high (e.g., aluminum) | Good (approaching stainless steel), improving fast |
Flame Retardancy | Varies | Many formulations are inherently flame-retardant |
Practical Advice: How to Use Heat-Conductive Plastics
If you’re an engineer, designer, maker, or just curious about these materials, here’s how you can get started:
Step 1: Identify the Heat Problem
First, figure out where and how much heat your device generates. Use thermal imaging cameras or simple temperature probes to map hotspots.
Step 2: Choose the Right Material
For most electronics, polycarbonate or nylon with thermal fillers (like boron nitride or aluminum oxide) is a good starting point. These materials balance thermal performance, strength, and cost.
Step 3: Consider Manufacturing Methods
- Injection Molding: Best for mass production of simple or moderately complex parts.
- 3D Printing: Ideal for prototypes or highly customized, complex geometries. Look for filaments with ceramic or mineral fillers.
- Extrusion: Used for creating sheets, tubes, or profiles that can be further machined.
Step 4: Test and Optimize
Build a prototype and test its cooling performance. Small changes in material composition, filler type, or part geometry can have a big impact on heat dissipation.
Step 5: Think Beyond Cooling
These plastics can also provide electrical insulation, flame resistance, and even transparency for applications like LED housings. Consider all these properties when designing your product.
New Gel Polymer Mimics Muscle and Gains Strength With an Innovative Formula
Breakthrough Eco-Friendly Plastic Could Power the Future of Flexible Electronics
FAQs About Heat-Conductive Plastics
Q: Are heat-conductive plastics as good as metal at cooling?
A: The best plastics now approach or even surpass stainless steel in thermal conductivity, but most metals (like copper and aluminum) still conduct heat better. However, plastics win on weight, cost, and electrical safety.
Q: Can I buy heat-conductive plastic for my DIY projects?
A: Yes! Many companies sell thermal conductive polymer compounds for electronics. For 3D printing, look for filaments with ceramic or mineral fillers.
Q: Are these plastics safe for the environment?
A: Like all plastics, disposal and recycling are important. However, because they replace heavier metals, they can reduce energy use in transportation and manufacturing, which is a net positive for the environment.
Q: Will my phone stop overheating if it uses these plastics?
A: It will help! While no material can eliminate overheating entirely, these plastics can significantly improve heat dissipation, leading to better performance and longer device life.
Q: How much do heat-conductive plastics cost compared to metal?
A: They’re generally cheaper to produce, especially when you factor in machining and assembly costs for metal parts. 3D printing also reduces waste and speeds up prototyping.
The Future of Cooling: What’s Next?
The field of heat-conductive plastics is advancing rapidly. Researchers are experimenting with new fillers, better alignment techniques, and even self-healing materials. As manufacturing scales up, expect to see these plastics in more consumer gadgets, electric vehicles, and industrial equipment.
For professionals, this is a chance to rethink thermal management—moving away from clunky metal solutions to sleek, integrated plastic designs. For hobbyists and students, it’s an exciting peek into the future of materials science.