Imagine a piece of fabric that flows like a shirt, bends like a glove, but—when needed—instantly becomes as hard as a shield. This isn’t something from a superhero movie; it’s real science happening right now at the California Institute of Technology (Caltech). Engineers there have invented a 3D-printed chain mail material that can switch between soft, flexible fabric and stiff, protective armor—with a physics principle you might already know from everyday life. This breakthrough could change everything from wearable protection and medical devices to building materials and space exploration.
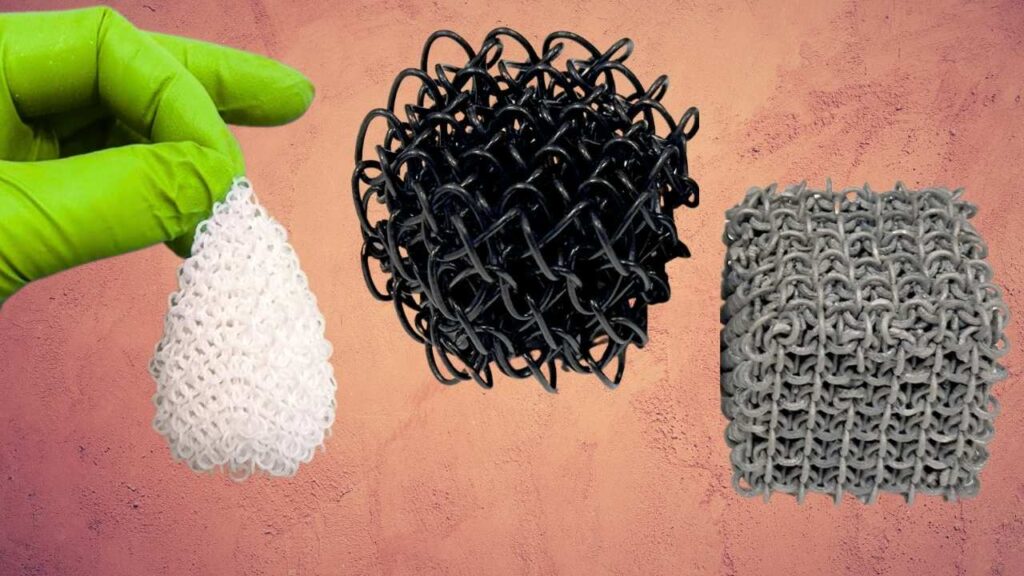
Why Is This Invention So Special?
For centuries, people have dreamed of armor that offers both comfort and protection. Traditional chain mail (think knights) is flexible but not very strong. Modern bulletproof vests are strong, but heavy and rigid. Caltech’s new adaptive material gets around this problem by combining flexibility and strength in a single structure—using 3D printing and advanced geometry. The secret? Thousands of tiny, interlocking hollow octahedron shapes, designed by computer and built layer by layer.
New 3D Chain Mail
Feature | Details | Applications |
---|---|---|
Flexibility | Drapes, bends, flows like fabric; lightweight. | Wearable armor, clothing, medical supports, soft robotics. |
Rigidity (Jammed State) | Up to 25x stiffer (measured in lab tests). | Body armor, helmets, exoskeletons, deployable structures. |
Material Options | Nylon (early prototypes), aluminum (in development for higher strength). | Industrial protective gear, aerospace, construction, robotics. |
Activation | Vacuum sealing (main method), magnets/electricity/temperature changes (under research). | Adaptive clothing, smart textiles, structural reinforcement. |
Weight | Similar to ordinary fabrics; metal versions will be heavier but still innovative. | Lightweight protective gear, portable shelters, space habitats. |
Impact Resistance | Nylon prototype: 3mm deformation (rigid) vs. 26mm (soft) under 30g steel ball at 3 m/s. Less deformation = better protection. | Sports equipment, safety gear, automotive panels. |
Professional Impact | Engineers, designers, scientists, medical device makers, architects could all benefit from adaptable materials. | Next-generation safety, mobility, and infrastructure products. |
Caltech’s 3D-printed chain mail is a major leap in smart materials. By combining flexibility, strength, and adaptability in a single structure, this technology could redefine how we protect, support, and build. While practical applications are still under development, the science is sound and the potential is vast.
Whether you’re a student fascinated by technology, a professional seeking the next big thing, or simply someone interested in the future of safety and comfort, this is a development worth watching. The era of on-demand protection is arriving—not from comic books, but from cutting-edge research labs.
How Does Caltech’s Chain Mail Work?
A Fabric with a Mind of Its Own
At its most basic, Caltech’s 3D-printed chain mail is a mesh of hollow octahedrons—shapes with eight triangular faces—designed to interlock like puzzle pieces. Each particle is hollow, lightweight, and strong. When the fabric is loose, the particles can slide past each other, making the whole material flexible and soft, just like a piece of cloth.
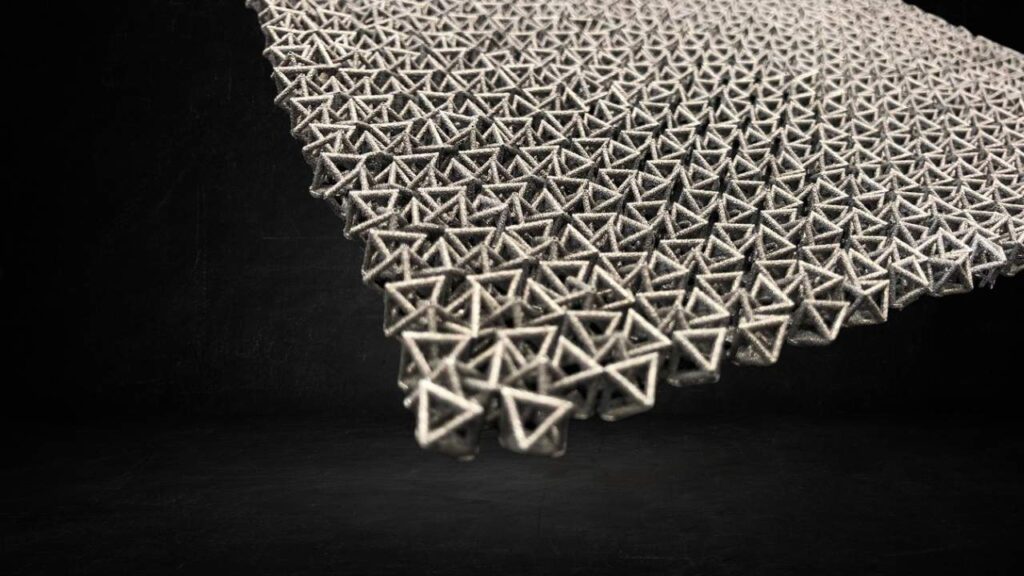
But when the material is compressed—say, by wrapping it in a flexible bag and sucking out the air (a process called vacuum packing)—the particles jam together tightly. This jamming transition is a bit like how coffee grounds in a vacuum-sealed bag become hard: the particles lock in place, transforming the entire fabric into something much stiffer. For Caltech’s material, this means the fabric can become up to 25 times stiffer—strong enough to support many times its own weight and resist impacts that would crumple ordinary textile.
How Do You Tell the Material to Harden?
Right now, vacuum sealing is the most direct way to activate the stiffening effect. But the Caltech team is exploring other ways to trigger this change, such as electrical signals, magnetic fields, temperature shifts, and even mechanical cables threaded through the fabric. Imagine a jacket sleeve with a hidden cable—pull a drawstring, and the sleeve stiffens for extra protection. Or, in the future, using a smartphone app or a voice command to instantly reinforce your safety gear.
Real-World Performance
In laboratory tests, a piece of the nylon prototype—when left soft—deformed 26 millimeters when hit by a small steel ball. When the same material was vacuum-packed and made rigid, the deformation dropped to just 3 millimeters. That’s a huge difference—an 87% reduction in movement under impact, which means much better protection for the wearer. The nylon prototype could hold over 50 times its own weight when rigid, with only minor deformation.
But nylon is just the beginning. Researchers are now working with metals like aluminum, which could make versions of this material that are even stronger and suitable for everything from industrial protective gear to deployable buildings and space habitats.
Practical Applications: Who Could Benefit?
Protective Gear and Sports Equipment
First responders, police, and military personnel could wear vests and helmets that are light and comfortable during patrols, but instantly become rigid in emergencies—absorbing impacts from falls, blows, or even projectiles. Athletes—cyclists, skiers, martial artists—could wear flexible padding that hardens only where and when needed, reducing injury risk without restricting movement.
Medicine and Rehabilitation
Medical casts for broken bones are a perfect example. Today’s casts are heavy, itchy, and often uncomfortable. With this adaptive material, a cast could be soft and comfortable for everyday wear, but stiffen up to support the bone when needed. The same logic applies to braces and supports for people with joint or muscle injuries—offering customizable stiffness for comfort and healing.
Construction and Infrastructure
Deployable shelters for disaster zones, temporary bridges, and even portable flooring or walls for emergency housing could be transported flat, then instantly assembled and made rigid on-site. The lightweight, easy-to-transport nature of these materials could transform how we respond to earthquakes, floods, and other crises.
Aerospace and Space Exploration
In space, weight and adaptability are critical. This material could become the basis for spacesuits that offer both flexibility for movement and on-demand rigidity for protection against micrometeoroids or sharp surfaces. Inflatable habitats on the Moon or Mars could be made from this fabric, providing safety and comfort with minimal launch mass.
Everyday Life: Clothing and Consumer Products
While not yet possible, future smart clothing—jackets, gloves, shoes—could use this technology for safety, comfort, and even style. Imagine shoes that stiffen for better support on rough terrain, or a jacket that hardens in a fall, reducing injury risk for elderly people or children.
From Lab to Reality: How Was This Material Developed?
Step 1: Inspiration from Nature and History
While polycatenated architected materials are new, the concept of interlocking parts is ancient. Traditional chain mail, knotted nets, and some crystal structures in nature all show how strong, flexible networks can be built from simple, repeating units. Caltech’s researchers, led by Professor Chiara Daraio, took this idea and gave it a 21st-century twist.
Step 2: Computer Design and Simulation
Before anything was built, scientists used advanced computer models to test different shapes and arrangements. Octahedrons (eight-sided) proved especially effective—strong, hollow, easy to interlock, and adaptable for different applications.
Step 3: 3D Printing Precision
The material is built layer by layer using precise 3D printers that can create complex, hollow shapes in plastics (like nylon), as well as metals (aluminum in development). This digital manufacturing means every link is perfectly identical and strong.
Step 4: Real-World Testing
Prototypes were tested for flexibility, rigidity, impact absorption, and durability—both in the lab and with help from partners in engineering, medicine, and even architecture. The team compared how rigid and soft versions performed under real-life conditions, making sure the material lived up to its promise.
Step 5: Exploring New Materials and Controls
Future versions could include different metals (steel, titanium), advanced polymers (stronger plastics), or even composite materials. The team is also testing multiple ways to trigger the change, so the material can be customized for different needs—whether that’s a soldier’s vest, a construction panel, or a piece of gym gear.
New 3D Textile Material Designed to Improve Mobility and Comfort in Wearable Tech
Scientists Develop Self-Healing Materials for Electronics and Wearable Devices
The Rise of Wearable Technology: Materials That Make Smart Clothing Possible
FAQs About New 3D Chain Mail
How does this material compare to traditional chain mail?
Traditional chain mail is made of simple, round metal rings and provides flexibility but only moderate protection. Caltech’s 3D-printed version uses engineered, interlocking shapes that can carry more load and be adjusted from soft to stiff—offering both comfort and superior protection in a way that older armors could not.
Is this chain mail material available to buy?
Not yet. While prototypes exist in the lab, commercial products using this technology are still years away. The science is real, but mass production, safety testing, and translating the invention into practical uses will take more time and development.
Could this material be used for everyday clothing?
Potentially, yes. The basic science could, in the future, be used in clothing that adapts to your needs—stiffening in a fall or softening for comfort. But today’s focus is on protective gear, medical supports, and industrial uses—not fashion or everyday wear.
Is it environmentally friendly?
3D printing can use less material and waste than traditional manufacturing, and recyclable metals like aluminum may be used in future versions. The environmental impact will depend on the materials and methods used as the technology evolves.
How expensive will it be?
Currently, 3D printing at this level is costly, but prices are falling as the technology improves. Large-scale production and material optimization will make this more affordable over time. Costs will depend on the final application—simple plastic versions will be less expensive than advanced metal composites.
Who could use this professionally?
Material scientists, engineers, designers, medical device developers, architects, and safety equipment makers all stand to benefit. This material could lead to new careers in adaptive technology, smart manufacturing, and advanced product design.