Imagine a piece of metal so smart that, after being bent or twisted in the icy coldness of outer space, it snaps right back to its original shape—all by itself. Now imagine it doing this at a temperature so cold, water is frozen stronger than steel—−200 °C. That’s not science fiction. Thanks to breakthrough research, a new copper-based shape memory alloy (SMA) is ready to change the future of space exploration, energy infrastructure, and advanced engineering here on Earth.
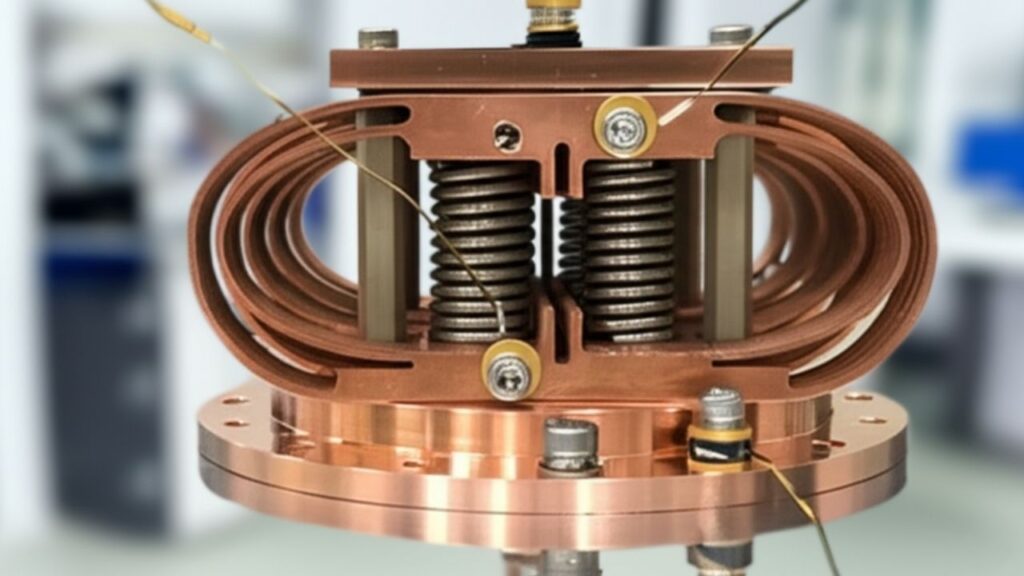
The Breakthrough: Shape Memory at Extreme Cold
Traditional metal parts have always had a weakness—the colder it gets, the weaker or more brittle they become. Shape Memory Alloys (SMAs), which can “remember” and return to a set shape, have revolutionized things like medical devices and robots. But until now, nearly all SMAs lost this memory at very low temperatures.
This new discovery—a blend of copper, aluminum, and manganese (Cu-Al-Mn)—is the world’s first alloy of its type proven to remain fully functional at the lowest of the low: deep cryogenic temperatures.
New Copper Alloy Works in −200 °C Temps
Aspect | Details |
---|---|
Main Breakthrough | Cu-Al-Mn shape memory alloy returning to original shape at −200 °C |
Unique Advantages | Maintains work output and memory effect far into cryogenic range; robust against mechanical stress |
Key Applications | Spacecraft actuators, telescope heat switches, hydrogen storage technology, LNG transport, robotics |
Supersedes | Nickel-Titanium (NiTi) shape memory alloys, which fail below −20 °C |
Professional Impact | First practical material for mechanical actuation at deep cryogenic temps, offering new design freedom |
Research Leaders | Pioneered by teams at Tohoku University and the Japan Aerospace Exploration Agency (JAXA) |
Peer-Reviewed Publication | Results published in 2025, Communications Engineering Journal |
Official Resource | JAXA – Japan Aerospace Exploration Agency |
The Cu-Al-Mn shape memory alloy is more than just a new metal—it is a technological disruptor, enabling active mechanical systems in the coldest places imaginable. By surviving and staying functional at −200 °C, it drastically expands the designer’s toolkit for space, energy, robotics, and critical infrastructure. Expect to see these alloys powering tomorrow’s astronauts, hydrogen plants, and even the climate sensors tracking our changing world—wherever reliable action in the deep cold matters most.
What Are Shape Memory Alloys, and Why Do They Matter?
The Magic of Memory Metals
A Shape Memory Alloy (SMA) is a metal that can seem almost alive: bend it, stretch it, or squeeze it out of shape—and it springs back to its original form when exposed to a certain temperature. SMAs do this because of a reversible change inside their crystal structure, known as a phase transformation. The two main “phases” are called martensite (soft, easily reshaped) and austenite (strong, snaps back).
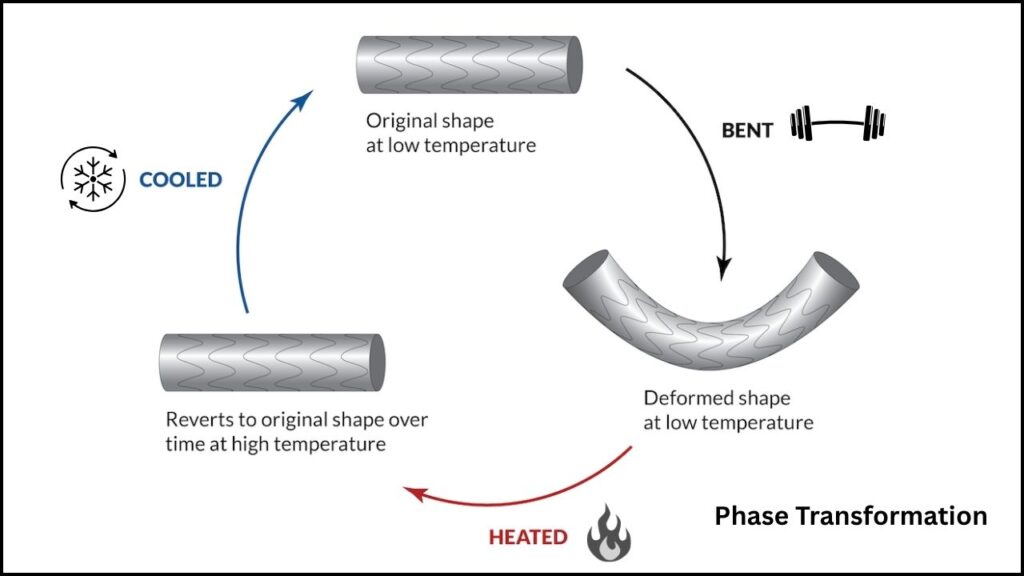
SMAs are already used all over the world: dental wires, self-tightening fasteners, robot arms, and more. But their Achilles’ heel? Cold. Existing alloys like nickel-titanium work well above freezing but lose their magic as temperatures drop much below −20 °C. That’s a severe limitation for space operations, deep-sea exploration, and cryogenic energy tech.
Why Outer Space and Cryogenics Demand More
Space, the Moon, Mars, or the outer planets experience temperatures so cold that most machines become brittle or outright fail. In the growing hydrogen economy, safe storage depends on ultra-cold valves, switches, and controls. Having a reliable actuator or switch that works at temperatures below −150 °C was simply not possible—until the discovery of this new copper alloy.
Deep Dive: How the New Cu-Al-Mn Alloy Works
A Revolution at the Atomic Level
The Cu-Al-Mn alloy achieves its astonishing performance through clever control over which phases of the metal appear and when they change. Researchers adjusted the amounts of aluminum and manganese to finely tune the transition temperature—pushing the “memory effect” deep into cryogenic territory.
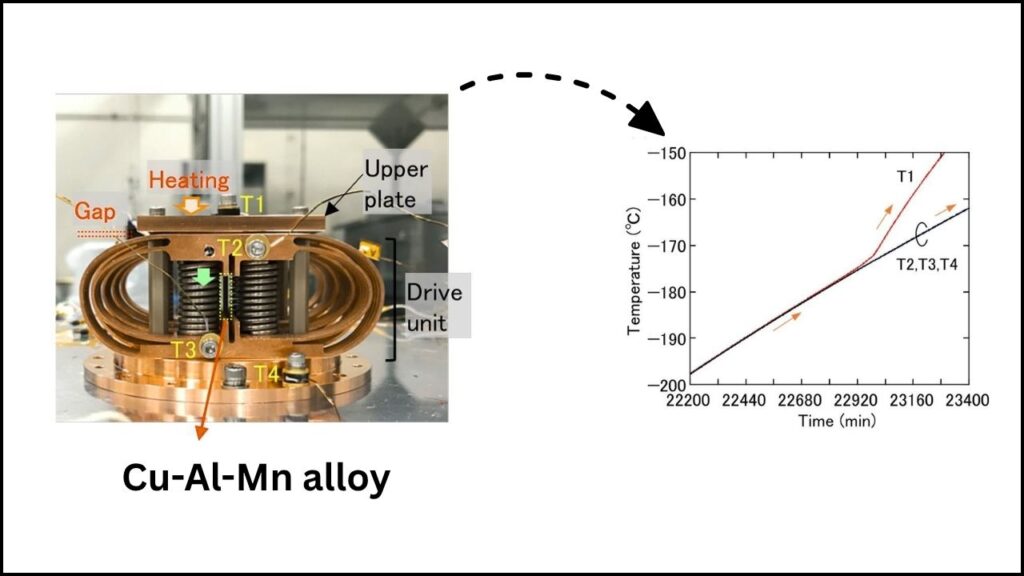
- Martensitic transformation at ultra-low temperatures enables the alloy to “switch” back to its original form even when severely deformed at −200 °C.
- The alloy’s grain structures and density are engineered for increased resistance to fatigue and mechanical failure, critical for long-term space or energy mission reliability.
Successful Real-World Tests
Researchers have already made prototype mechanical heat switches—devices essential for controlling temperatures aboard satellites and telescopes. At −170 °C, the Cu-Al-Mn actuator could reliably open and close the heat switch simply by changing temperature, all without electronics or outside force. Such performance represents a first for shape memory devices.
Tunability for Every Mission
By changing the ratio of copper, aluminum, and manganese, design teams can tune the operating window for each specific task. Whether the job needs the alloy to move at −150 °C, −180 °C, or colder, the alloy can be tailored with high precision—offering flexibility for everything from Mars rovers to liquid hydrogen fuel plants.
Why Is This Discovery Important? Practical Impacts
Spacecraft and Satellite Technology
- Reliable Mechanisms: Space vehicles need mechanisms that won’t seize up or shatter in the cold. The new copper alloy gives engineers a tool to build latches, shutters, antenna releases, and other parts that must operate reliably after years of exposure to chilling vacuum.
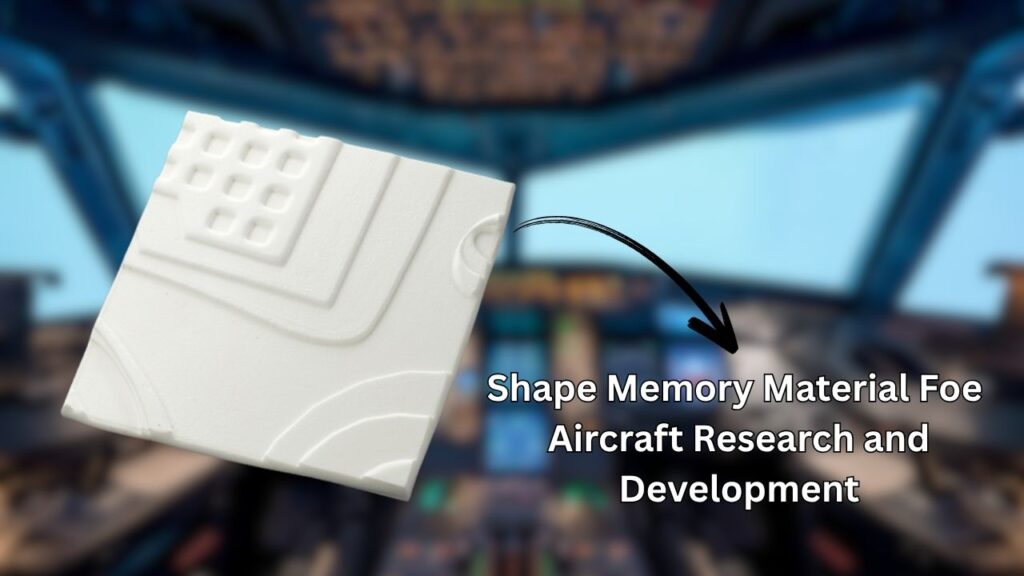
- Thermal Control: Systems aboard satellites, telescopes, and planetary probes depend on heat switches to balance internal temperature. Cu-Al-Mn actuators enable more compact and dependable devices.
Hydrogen and Cryogenic Infrastructure
- Safe Storage: The transport and storage of hydrogen as a fuel demands parts that do not fail at −250 °C. The new alloy means more reliable fail-safe valves and switches for the growing green hydrogen economy.
- Efficient Design: By replacing bulky motors and electronic controls with slim memory metal actuators, cryogenic hardware becomes lighter, simpler, and more energy-efficient.
Carbon-Neutral Energy and Environmental Monitoring
- LNG & Clean Fuel: In the liquefied natural gas (LNG) industry, operating in sub-zero environments is normal. Cu-Al-Mn SMAs offer new, passive solutions for critical operations where electronics won’t work.
- Climate Sensors and Autonomous Devices: More reliable mechanisms at low temperatures enable better long-term monitoring in polar or deep ocean environments.
How Does Cu-Al-Mn Outperform Previous Alloys?
Feature | NiTi Alloys (Old) | Cu-Al-Mn Alloy (New) |
---|---|---|
Lowest Working Temp | −20 °C (often higher) | −200 °C and below |
Cost & Availability | NiTi is expensive, import-restricted | Copper-based: more affordable, scalable |
Mechanical Output at Cryo Temps | None | High |
Fatigue Resistance | High at moderate temps | Designed for low temp cycling |
Professional Uses | Medical, robotics, warm aerospace | Deep space, hydrogen, polar operations |
Tuneability | Moderate, limited composition range | Wide adjustability via chemistry |
Real Stories: Potential Uses Across Industries
Space Exploration
Japan’s leading space agency, JAXA, is testing Cu-Al-Mn SMAs for future lunar rovers and deep space probes. The aim: build deployable systems that survive multi-year journeys in the coldest corners of our solar system.
Cryogenic Energy
With energy security a priority, large-scale hydrogen and LNG operations are seeking passive, reliable switching systems. Early pilot projects in Japan and Europe are reporting lower maintenance and improved safety margins using memory alloy technology.
Medical and Scientific Research
Low temperature and reliability also appeal to research labs working on superconducting magnets, quantum computers, and cryo-biological storage—opening up more precise and less failure-prone instrumentation.
Step-by-Step Guide: How Engineers and Designers Can Use This Alloy
1. Assess the Environment:
Determine the temperature and operating stresses your application will face. For anything down to −200 °C (and potentially even colder in the future), your requirements are within the capabilities of Cu-Al-Mn SMAs.
2. Select the Alloy Composition:
Work with suppliers or refer to published transition temperature tables to identify the right balance of copper, aluminum, and manganese for your critical point.
3. Prototype and Test:
Design your actuator, switch, or mechanism. Simulate the operation in thermal chambers. The new alloy has shown minimal performance loss over many thousands of cycles.
4. Integrate Into Devices:
Build the actuator into your system. Because the transformation relies only on temperature—not electronics—it can operate in extreme vacuums, high-radiation environments, and where electric circuitry is impractical.
5. Monitor and Maintain:
While these materials are engineered for exceptional fatigue life, implement regular checks for mission-critical components, especially in the early adoption phase.
Professions and Industries Affected
- Aerospace Engineers: New options for deep space and planetary missions.
- Energy Sector Professionals: Reliable actuation in hydrogen or LNG supply chains.
- Robotics Designers: Passive actuation for robots in extreme cold.
- Cryogenics Experts: Fail-safe mechanical switches for research and industrial equipment.
- Environmental Scientists: Polar and deep-sea sensor systems with long lifespans.
Scientists Develop Breakthrough Copper Composite With Superior Strength and Conductivity
Scientists Discover Hidden Aluminum Sites That Supercharge Zeolite Catalysis
Physicist Resolves Long-Standing Thermodynamics Question and Refines Einstein’s Model
FAQs About New Copper Alloy Works in −200 °C Temps
What is a Shape Memory Alloy?
A shape memory alloy is a metal that can be twisted, bent, or even compressed, but when heated or cooled to a certain temperature, it returns to its original “memorized” shape due to a reversible change in its internal structure.
Why is the new copper alloy so significant?
It’s the first memory metal proven to operate at −200 °C, unlocking new levels of reliability for space, energy, and research sectors that depend on mechanical action in extreme cold.
How is this material used in space?
Deployed as thermal switches, actuator elements, or locking mechanisms, especially where traditional electronics or hydraulics would freeze or fail.
Does it have advantages for Earth applications?
Yes! It’s an excellent option for hydrogen storage valves, LNG plants, arctic equipment, polar research tools, and even medical refrigeration systems.
Is it more affordable than nickel-titanium alloys?
Because copper is a major component, this new alloy is typically less expensive and easier to produce at scale than many nickel-based “memory metals.”
Who led the research?
The initial development and demonstration were carried out by collaborative teams at Tohoku University and the Japan Aerospace Exploration Agency (JAXA), published in 2025.