New Laser Trackers Deliver Unmatched Precision: In today’s fast-moving manufacturing world, “New Laser Trackers Deliver Unmatched Precision for Complex Industrial Assembly Lines” is more than just a headline—it’s a revolution. These high-tech devices are transforming how factories build everything from cars to airplanes, ensuring every part fits perfectly.
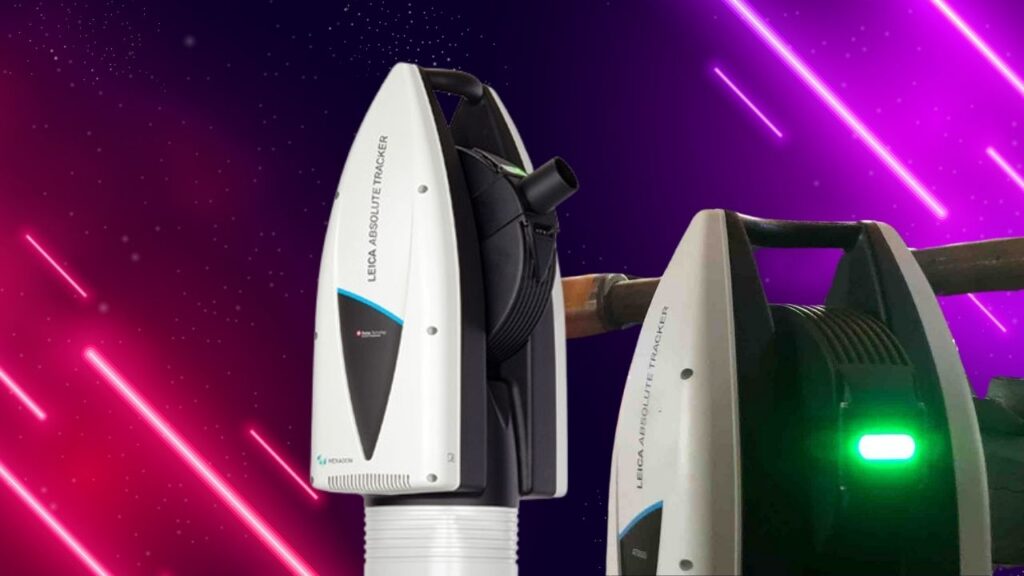
Whether you’re a curious 10-year-old or a seasoned engineer, understanding how laser trackers work—and why they matter—is key to appreciating the future of industry.
New Laser Trackers Deliver Unmatched Precision
Feature/Stat | Details |
---|---|
Market Growth | Laser tracker market projected to reach $250 million by 2033, with a CAGR of 6.2% from 2026–2033. |
Precision | New models achieve sub-millimeter accuracy over large volumes (up to 100 meters). |
Portability | Latest trackers weigh as little as 4.9 kg, enabling easy on-site measurements. |
AI Integration | AI-driven self-calibration and cloud-based analysis boost efficiency and reduce errors. |
Productivity Gains | 82% improvement in robot positional accuracy with laser tracker feedback. |
Industry Adoption | Widely used in automotive, aerospace, shipbuilding, and wind energy sectors. |
Official Resource | Hexagon Manufacturing Intelligence |
New laser trackers are setting a new standard for precision, speed, and flexibility in complex industrial assembly lines. By combining cutting-edge technology with user-friendly features, these devices are helping manufacturers build better products, faster and more sustainably. Whether you’re building cars, airplanes, or wind turbines, investing in a modern laser tracker could be the smartest move for your business.
What Are Laser Trackers and How Do They Work?
Laser trackers are advanced measuring tools that use laser beams to pinpoint the exact position of an object in 3D space. Imagine a super-smart flashlight that can tell you exactly where something is, down to a tiny fraction of a millimeter. Here’s how they work:
- A laser beam is sent from the tracker to a special reflector (usually a shiny ball or prism) placed on the object.
- The tracker measures how long it takes for the light to bounce back and the angles involved.
- This data is used to calculate the exact position of the object in three dimensions.
Think of it like playing a game of laser tag, but instead of scoring points, you’re measuring the size, shape, and position of machine parts with incredible accuracy.
Why Are Laser Trackers a Game-Changer for Industrial Assembly Lines?
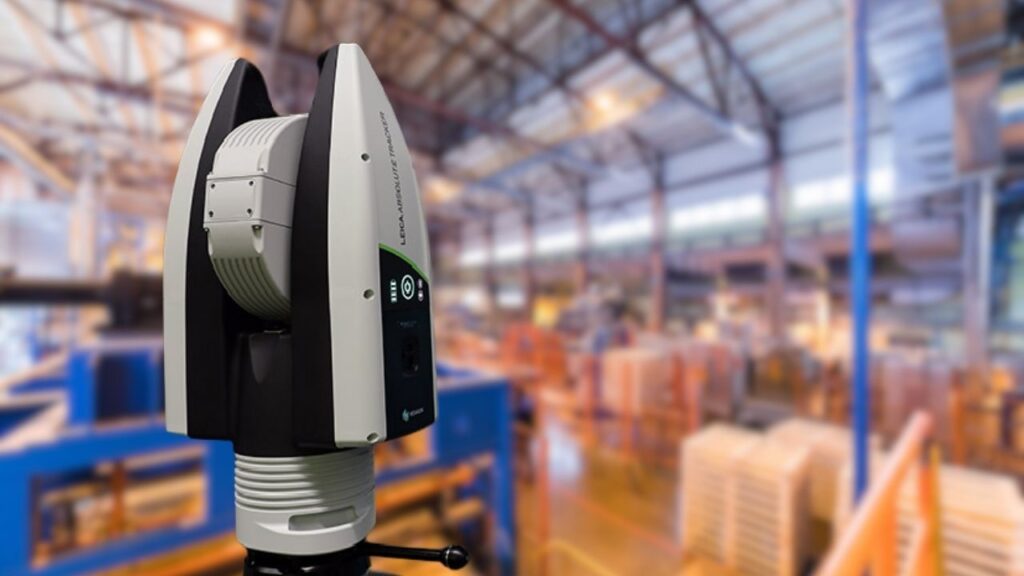
1. Unmatched Precision
Modern factories rely on parts that must fit together perfectly. Even a tiny error can lead to big problems—like a car door that won’t close or an airplane wing that doesn’t align. New laser trackers can measure distances as small as a few microns (that’s smaller than a human hair!) over huge areas, ensuring every part is just right.
2. Portability and Flexibility
Older measurement machines were big and heavy. Today’s laser trackers are compact and light—some weigh less than a small laptop (just 4.9 kg!). This means engineers can carry them right to the assembly line or even out to a construction site, measuring parts wherever they are, instead of moving heavy parts to a fixed machine.
3. Boosting Productivity and Quality
Laser trackers speed up the inspection process. Instead of stopping production to check measurements, workers can quickly verify parts on the spot. This reduces downtime, cuts costs, and helps catch mistakes before they become expensive problems.
4. Integration with Robotics and Automation
Robots are everywhere in modern factories, but they need to know exactly where to move. Laser trackers provide real-time feedback, helping robots place parts with pinpoint accuracy. In one study, using laser trackers improved robot accuracy by 82%, making old robots work like new and saving companies money on replacements.
5. AI and Smart Features
The latest laser trackers use artificial intelligence (AI) to self-calibrate, analyze data, and even guide workers through the measurement process. Some systems offer VR-based training and cloud-based software, making it easier than ever to use these advanced tools.
Real-World Examples: How Laser Trackers Are Used
Automotive Industry
Car makers use laser trackers to inspect and align massive body panels, set up weld lines, and ensure every component fits perfectly. This not only improves quality but also supports green manufacturing by reducing material waste.
Aerospace and Shipbuilding
Building airplanes and ships involves assembling huge parts with tight tolerances. Laser trackers allow workers to measure and align these components from a safe distance, ensuring safety and saving time.
Wind Energy
Wind turbine blades are enormous and must be precisely shaped. Laser trackers help manufacturers inspect these parts quickly and accurately, supporting the growth of renewable energy.
Step-by-Step Guide: Using a Laser Tracker on the Assembly Line
Step 1: Set Up the Tracker
- Place the laser tracker on a stable surface near the part to be measured.
- Power it on and connect to the control software (often wirelessly).
Step 2: Place Reflectors
- Attach special reflectors to key points on the object.
- The tracker will “lock on” to these reflectors using advanced technology.
Step 3: Start Measuring
- The tracker sends out its laser beam and records the position of each reflector.
- Data is displayed in real time on a computer or tablet.
Step 4: Analyze Results
- The software compares measurements to design specifications.
- Any deviations are flagged, allowing immediate corrections.
Step 5: Document and Share
- Results can be saved, shared, or uploaded to cloud-based systems for further analysis or quality records.
Practical Advice: Getting the Most from Laser Trackers
- Train Your Team: While laser trackers are getting easier to use, proper training ensures accurate results and safe operation.
- Integrate with Automation: Connect your tracker to robots and automated guided vehicles (AGVs) for continuous, hands-free inspection.
- Leverage AI: Use AI-powered features for self-calibration and error reduction, saving time and reducing the need for expert oversight.
- Maintain Your Equipment: Regular calibration and maintenance keep your tracker performing at its best.
- Think Green: Accurate measurement reduces material waste and supports sustainable manufacturing practices.
Quantum Photonic Interconnects via Nanofibers Advance Distributed Quantum Architecture
Photonic Nanofabrication Enables Miniaturized Neutral Atom Quantum Networking
DNA Enabled Nanostructures Proposed To Achieve Superradiance For Quantum Light Sources
FAQs About New Laser Trackers Deliver Unmatched Precision
What is a laser tracker?
A laser tracker is a high-precision measuring tool that uses a laser beam to determine the exact 3D position of objects, often used in manufacturing and assembly lines.
How accurate are modern laser trackers?
New models can achieve sub-millimeter accuracy over distances up to 100 meters, making them ideal for large-scale industrial applications.
Which industries use laser trackers the most?
Automotive, aerospace, shipbuilding, and wind energy are leading adopters, but any industry needing precise measurement of large parts can benefit.
Are laser trackers easy to use?
Yes! Thanks to AI, wireless connectivity, and user-friendly software, even non-experts can operate modern laser trackers with minimal training.
What are the main benefits for manufacturers?
Laser trackers improve quality, reduce waste, boost productivity, and support automation—all while saving time and money.