Reusable Future for Carbon Fibre Composites: The reusable future for carbon fibre composites unlocked by new method is a game-changing development for industries ranging from aerospace to automotive. Traditionally, carbon fibre composites have been celebrated for their incredible strength and lightweight properties, but recycling them has been a major challenge. Now, innovative recycling techniques are making it possible to reclaim and reuse these advanced materials without sacrificing their quality—a breakthrough that promises to make our world both greener and more efficient.
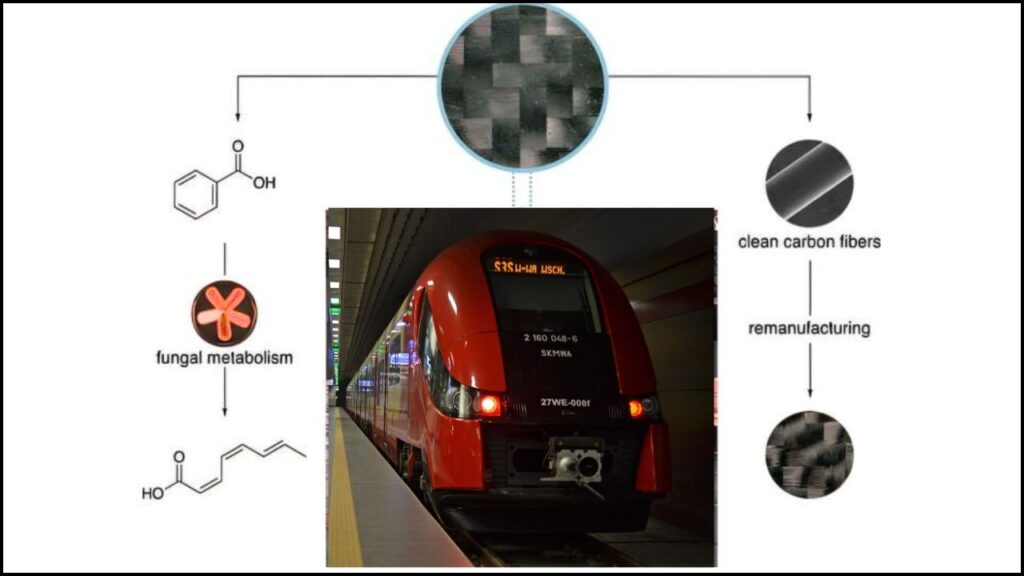
Why Carbon Fibre Composites Matter
Carbon fibre composites are materials made by weaving together thin strands of carbon—thinner than a human hair—and embedding them in a plastic matrix. The result? A material that’s as strong as steel but much lighter. This unique combination makes carbon fibre composites the go-to choice for building airplanes, cars, wind turbines, and even sports equipment.
But there’s a catch: while these composites are tough and durable, they’re not easy to recycle. When products made from carbon fibre reach the end of their life, most of them end up in landfills or are incinerated. This is not only wasteful but also harmful to the environment.
The Recycling Challenge
Until recently, recycling carbon fibre composites meant shredding the material and burning away the plastic, which damaged the valuable fibres and reduced their strength. This process, called “downcycling,” meant the recycled fibres could only be used in low-value products—not in the high-performance parts they originally came from.
With global demand for carbon fibre composites expected to increase by at least 60% in the next decade, and with hundreds of thousands of tonnes of composite waste projected from industries like wind energy and aviation, finding a better recycling solution is urgent.
Reusable Future for Carbon Fibre Composites
Feature/Stat | Details & Data |
---|---|
New Recycling Methods | Laser-assisted, enzyme-based, and solvolysis pretreatment methods preserve fibre strength and quality |
Fibre Strength Retained | Up to 97% (USC enzyme method); up to 90% (Sydney solvolysis) |
Energy Savings | Recycled carbon fibre uses just 1/10th the energy of new production |
Projected Waste by 2050 | 840,300 tonnes (equivalent to 34 stadiums) from wind turbines and aircraft alone |
Major Applications | Automotive, aerospace, wind energy, construction |
Official Resource | Fraunhofer Institute |
The reusable future for carbon fibre composites unlocked by new method is more than just a scientific achievement—it’s a leap forward for sustainability, industry, and the planet. By reclaiming high-quality fibres from old products, we can build a circular economy where nothing goes to waste. These breakthroughs are already making a difference in cars, airplanes, and wind turbines, and their impact will only grow as more industries adopt them.
How the New Recycling Methods Work
1. Laser-Assisted Recycling
Researchers at the Fraunhofer Institute in Germany have developed a high-power laser process that carefully removes the plastic matrix from carbon fibre composites. Here’s how it works:
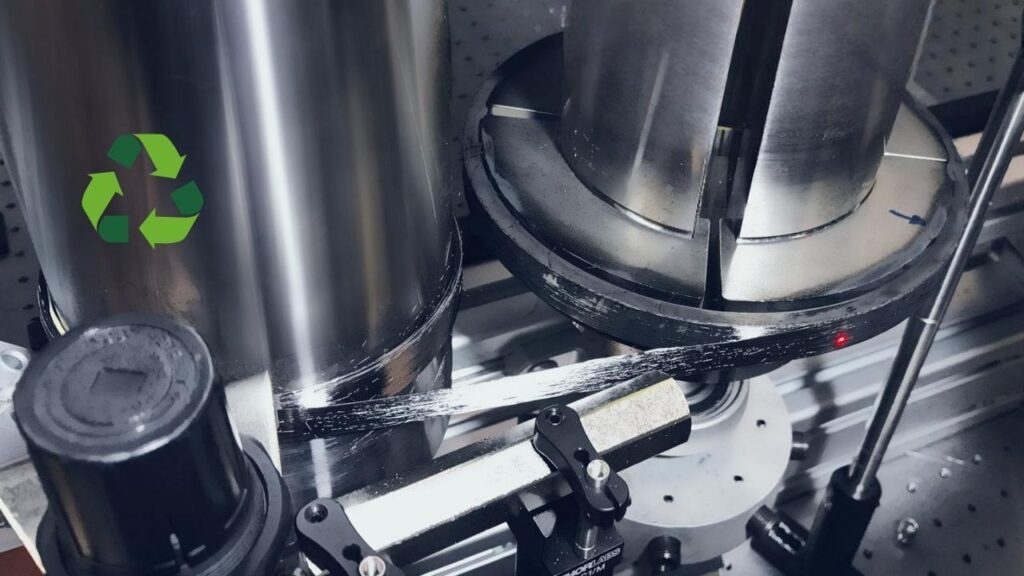
- Laser Degradation: A powerful laser heats the plastic around the fibres, breaking it down without harming the carbon fibres themselves.
- Continuous Fibre Recovery: Unlike old methods that chopped up the fibres, this technique keeps them long and strong—just like new.
- High-Quality Output: The reclaimed fibres are as strong as brand-new ones, making them suitable for demanding uses like hydrogen tanks for vehicles.
Practical Example: Imagine a used hydrogen tank from a bus. With this method, the carbon fibres can be unwound and reused in a new tank, saving both money and resources.
2. Enzyme-Based Recycling (Biocatalytic Upcycling)
At the University of Southern California (USC), scientists have taken inspiration from nature. They use special enzymes—tiny proteins made by fungi—to break down the plastic resin that holds the carbon fibres together.
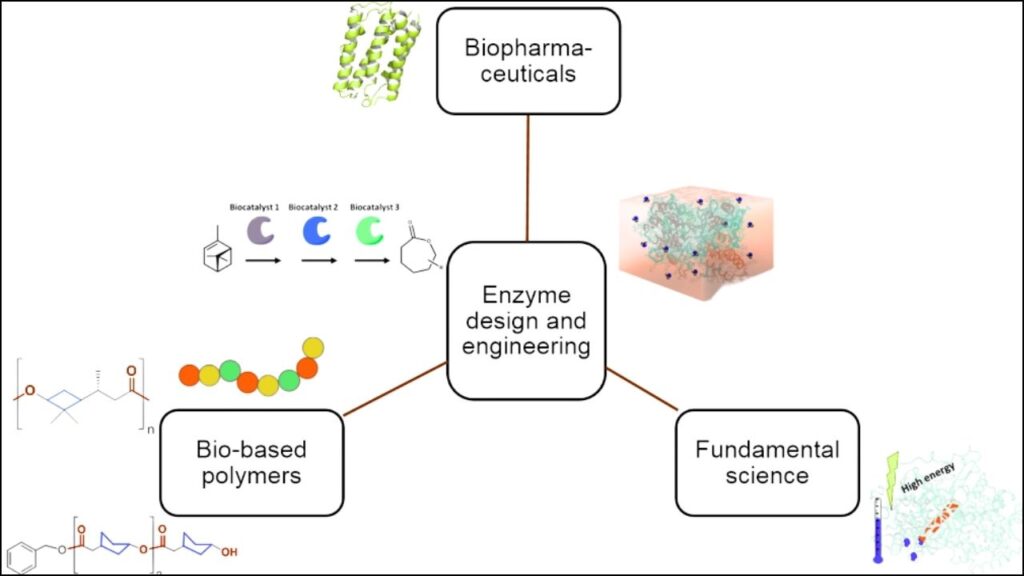
- Fungal Enzymes: Enzymes from fungi like Aspergillus niger digest the resin, freeing the carbon fibres without damaging them.
- High Fibre Strength: This method preserves over 97% of the original fibre strength, allowing the fibres to be reused in high-performance products.
- Circular Economy: Both the fibres and the plastic can be recovered and reused, making the process even more sustainable.
Practical Example: Car manufacturers can now recycle old car panels and use the reclaimed fibres in new vehicles, reducing waste and production costs.
3. Solvolysis Pretreatment
Researchers at the University of Sydney have developed a method called solvolysis pretreatment, which uses special chemicals to break down the plastic at lower temperatures.
- Lower Energy Use: The process needs less heat, which saves energy and reduces emissions.
- High Fibre Quality: Recycled fibres retain up to 90% of their original strength—10% better than traditional thermal recycling.
- Scalable Solution: This method can be applied to waste from wind turbines, airplanes, and more.
Practical Example: Old wind turbine blades, which are made from carbon fibre composites, can be recycled into new construction materials using this method.
Why This Matters: Environmental and Economic Impact
Environmental Benefits
- Less Waste: These new methods could keep hundreds of thousands of tonnes of composite waste out of landfills every year.
- Lower Carbon Footprint: Recycling carbon fibre uses just a tenth of the energy required to make new fibre, slashing greenhouse gas emissions.
- Resource Conservation: By reusing fibres, we reduce the need to extract and process new raw materials.
Economic Advantages
- Cost Savings: Recycled carbon fibre is cheaper to produce than new fibre, helping industries cut costs.
- New Value Chains: High-quality recycled fibres can be used in premium applications, creating new business opportunities.
- Regulatory Compliance: As governments introduce stricter recycling and efficiency standards, these methods help companies stay ahead.
Step-by-Step Guide: How Carbon Fibre Recycling Works
Step 1: Collection
- Gather used carbon fibre composite products (e.g., car parts, airplane wings, wind turbine blades).
Step 2: Preparation
- Clean and sort the materials to ensure they’re ready for recycling.
Step 3: Matrix Removal
- Laser Method: A laser breaks down the plastic matrix without harming the fibres.
- Enzyme Method: Fungal enzymes digest the resin, freeing the fibres.
- Solvolysis: Chemicals dissolve the resin at lower temperatures.
Step 4: Fibre Recovery
- Carefully extract the carbon fibres, keeping them as long and undamaged as possible.
Step 5: Reuse
- The recovered fibres are tested for strength and quality.
- They are then used to make new products—sometimes even better than the originals.
Real-World Applications
- Automotive: Lighter, recycled carbon fibre parts help cars use less fuel and meet efficiency standards.
- Aerospace: Airplanes can be built with recycled materials that are just as strong as new ones.
- Wind Energy: Old turbine blades can be turned into new construction materials or even new turbine parts.
- Construction: Recycled fibres make strong, lightweight panels for buildings and bridges.
Photonic Nanofabrication Enables Miniaturized Neutral Atom Quantum Networking
DNA Enabled Nanostructures Proposed To Achieve Superradiance For Quantum Light Sources
Quantum Powered AI and Weather Prediction Project Clear Sky via Quantum Drones Launches
FAQs About Reusable Future for Carbon Fibre Composites
Q1: Why can’t we just melt down carbon fibre composites like plastic?
A: Carbon fibre composites are made with thermosetting plastics, which don’t melt when heated. This makes them very tough, but also hard to recycle using traditional methods.
Q2: Are recycled carbon fibres as strong as new ones?
A: Yes! With the latest methods, recycled fibres can retain up to 97% of their original strength—sometimes even more.
Q3: Is recycling carbon fibre good for the environment?
A: Absolutely. It reduces landfill waste, saves energy, and cuts down on greenhouse gas emissions.
Q4: What industries benefit most from this technology?
A: Automotive, aerospace, wind energy, and construction are the biggest winners, but any industry using strong, lightweight materials can benefit.