Clean hydrogen stands out among alternative fuels because it produces only water when used, with no harmful emissions. But the vast majority of hydrogen today is still made from fossil fuels, undermining its green credentials. Now, new scientific breakthroughs are allowing industry to convert sugarcane waste—bagasse and furfural—into high-purity hydrogen with almost zero emissions. This is particularly exciting for countries with strong sugarcane sectors, such as India, Brazil, and South Africa, because it could cut pollution, create jobs, and turn agricultural waste into a valuable energy resource.
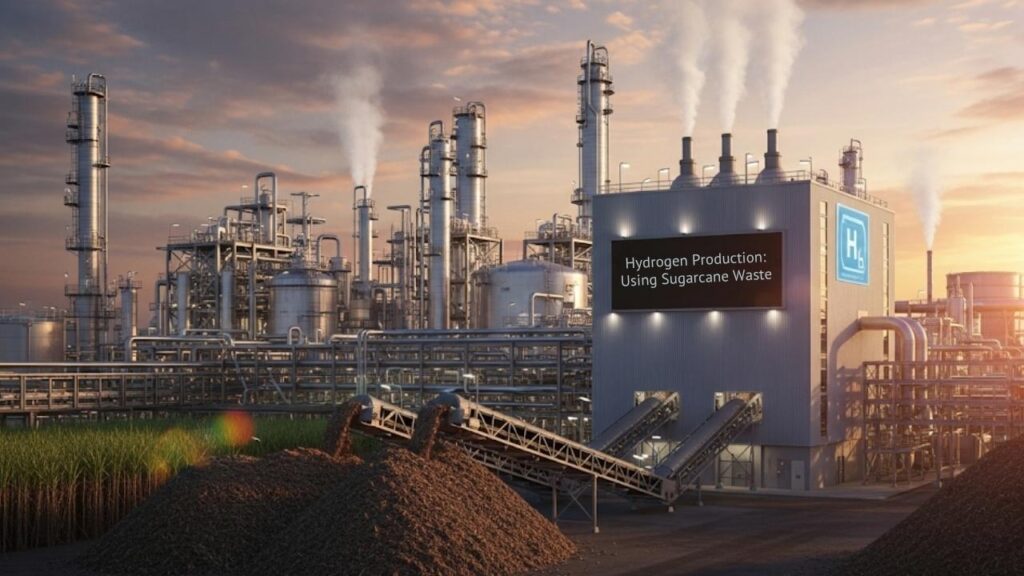
In this article, we’ll explain exactly how these innovative processes work, why they matter for both the environment and the economy, and how you can get involved—whether you’re a farmer, engineer, policymaker, student, or just a curious reader. We’ll break down the science so it’s easy to follow, highlight real-world examples, and offer practical advice for professionals. The goal is clarity and trustworthiness: you’ll find no hype, no misleading shortcuts, and only the most credible details.
Why Clean Hydrogen from Sugarcane Waste Is a Big Deal
Hydrogen has long been hailed as a clean energy carrier—when you burn it, the only byproduct is water. This makes it ideal for powering vehicles, factories, and even airplanes. However, more than 90% of the world’s hydrogen is currently produced from fossil fuels (mostly natural gas), a process that emits large amounts of carbon dioxide (CO₂). For hydrogen to truly help fight climate change, it must come from renewable sources and produce little to no CO₂ in its manufacture.
Sugarcane waste is a goldmine for this purpose. Every year, millions of tons of bagasse (the fibrous residue left after squeezing juice from sugarcane) and other crop residues pile up at sugar mills around the world. Traditionally, this waste is burned (releasing CO₂) or left to rot (releasing methane, another potent greenhouse gas). Capturing this waste and turning it into clean hydrogen instead can therefore reduce air pollution, lower greenhouse gas emissions, and create new income streams for farmers and mills.
Breakthrough Turns Sugarcane Waste Into Clean Hydrogen
Discovery | Who’s Behind It | How It Works | Key Data/Results | Professional Impact |
---|---|---|---|---|
Photoelectrochemical (PEC) Cell | UNIST (Ulsan National Institute of Science and Technology, South Korea) | Uses sunlight and furfural (from sugarcane waste) to split water and produce hydrogen at both electrodes. No CO₂ emissions. | 1.4 mmol/cm²/hr hydrogen (4x DOE benchmark). Byproduct: furoic acid (food/medicine). | Cost-competitive green hydrogen, new chemical markets. |
Sorption-Enhanced Chemical Looping Gasification (SECLG) | University of Johannesburg | Bagasse gasification with built-in CO₂ capture. Produces high-purity hydrogen, low tar/NOx. | Simulation: up to 69% hydrogen yield. No separate CO₂ capture needed. | Scalable, efficient hydrogen for sugar-producing nations. |
Microbial Hydrogen Production | MIT World Peace University | Microbes convert sugarcane juice into hydrogen, plus acetic acid, at room temperature. | Potential cost as low as $1/kg hydrogen. Zero-discharge. | Sustainable, low-tech, rural-friendly hydrogen. |
Sugarcane waste—once a disposal problem—has the potential to become a clean energy goldmine, thanks to breakthroughs in photoelectrochemical, gasification, and microbial hydrogen technologies. These advances can reduce air pollution, cut greenhouse gas emissions, create new jobs, and support rural development—especially in countries with large sugarcane industries.
For professionals, this is a call to action: invest in research, pilot new plants, and prepare for a future where agricultural waste powers the green economy. For everyone, this is proof that science and innovation can turn waste into a valuable, sustainable resource.
How Does It Work? A Step-by-Step Guide
1. The Photoelectrochemical (PEC) Approach
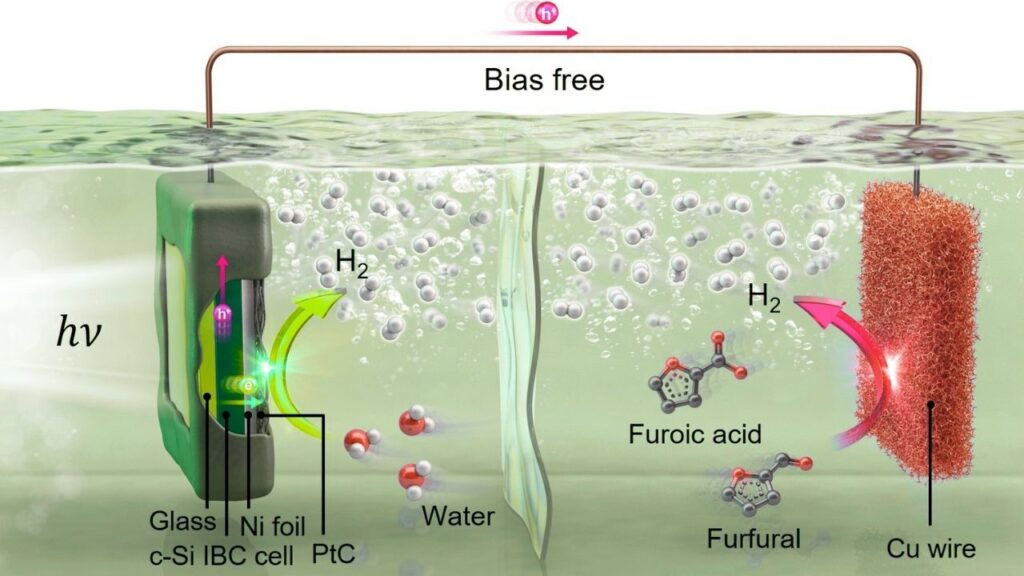
A team at UNIST in South Korea has built a device that generates hydrogen directly from sunlight and sugarcane waste—without electricity from the grid. Here’s a detailed look at how this system works:
- Step 1: Sugarcane Waste Processing
After juice is extracted from sugarcane, the leftover bagasse can be processed further to extract furfural, a valuable chemical compound. Modern mills already have equipment for bagasse processing, so adding furfural extraction is a feasible upgrade. - Step 2: Photoelectrode Design
The heart of the system is a silicon-based photoelectrode—a type of solar panel—coated with a thin layer of protective materials. This electrode absorbs sunlight and generates an electric current. When submerged in water, this current splits water molecules into hydrogen and oxygen. The oxygen is released harmlessly into the air.
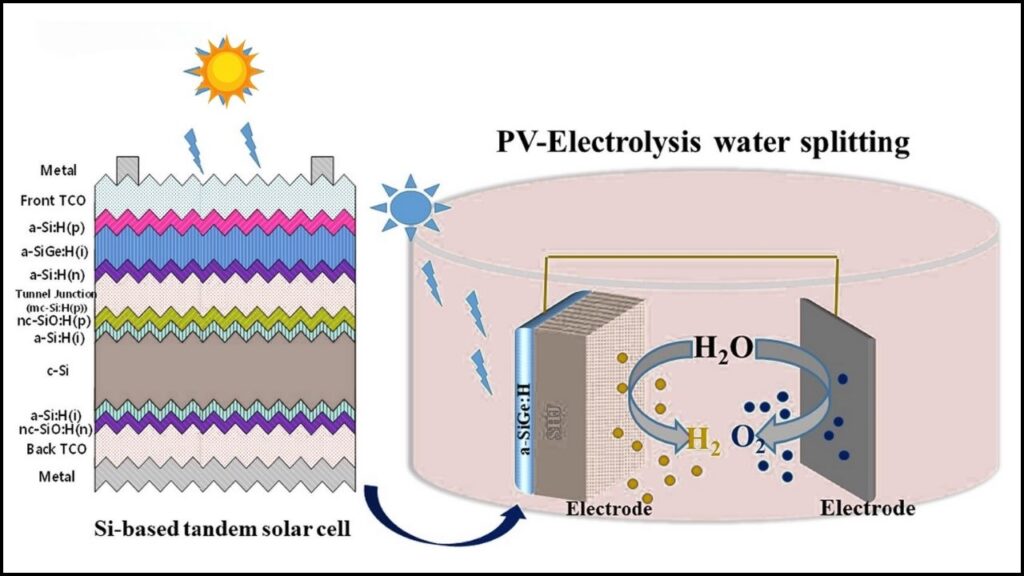
- Step 3: Electrochemical Oxidation of Furfural
On the other side of the device, a copper electrode oxidizes furfural, producing even more hydrogen gas. Importantly, no CO₂ is emitted during this process—the only byproducts are hydrogen and furoic acid, a chemical used in food and pharmaceuticals. - Step 4: Self-Powered, Zero-Emission Operation
The entire process is driven by sunlight, not grid electricity, so it’s genuinely green. The system has demonstrated hydrogen production rates of 1.4 mmol/cm²/hr—much higher than the 0.36 mmol/cm²/hr benchmark set by the US Department of Energy for commercial viability. - Step 5: Durability and Scalability
The team added advanced coatings (like nickel foil and glass) to protect the electrodes from corrosion. Early laboratory results indicate weeks of stable operation, which is promising for real-world applications.
Why this matters for industry:
This technology could allow a single sugarcane mill to become a mini hydrogen factory, using only sunlight and its own waste. Hydrogen’s high energy density makes it suitable for replacing diesel in trucks, buses, and even backup power for factories. If scaled up, this could help tropical countries rapidly decarbonize their transport and industrial sectors.
2. The Gasification Approach: SECLG
Researchers at the University of Johannesburg are exploring another path: gasifying sugarcane bagasse in a way that captures CO₂ as it forms.
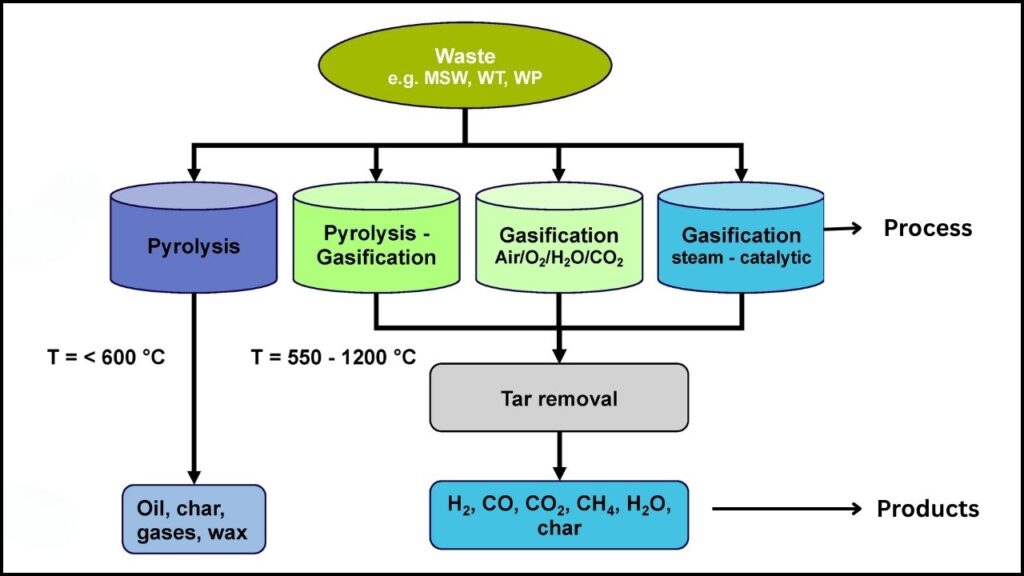
- Step 1: Gasification Basics
Bagasse is first dried and then introduced into a gasifier—a high-temperature reactor where it’s broken down with a limited supply of oxygen. This process produces syngas, a mix of hydrogen, carbon monoxide, and carbon dioxide. - Step 2: Chemical Looping and CO₂ Capture
Here’s where the innovation lies: the process uses metal oxides that react with CO₂ as it forms, capturing it as a solid carbonate. This happens during the reaction itself, so there’s no need for a separate, energy-intensive CO₂ capture step. - Step 3: High-Purity Hydrogen
The result is hydrogen gas with up to 69% purity, according to simulations. By comparison, traditional gasification often yields less than 50% hydrogen, with the rest as various pollutants. - Step 4: Environmental and Economic Benefits
Because CO₂ is captured as a solid, the system significantly reduces greenhouse gas emissions compared to conventional gasification. The process also produces less tar and air pollutants like nitrogen oxides (NOx), making it cleaner for local communities. - Step 5: Current Status and Next Steps
While the technology is still under development and scaling up, early simulations and lab tests show strong promise for industrial deployment. The next challenges will be building pilot plants and integrating them with existing sugar mills.
Why this matters for policy and business:
This system could allow countries like India, Brazil, and South Africa to turn millions of tons of bagasse—a current disposal headache—into valuable hydrogen. This could support clean public transport, green industry, and even hydrogen exports. It’s a win-win for climate, energy security, and rural employment.
3. The Microbial Approach
At MIT World Peace University, researchers are developing a low-cost, low-tech method using microorganisms to convert sugarcane juice directly into hydrogen.
- Step 1: Microbial Fermentation
Special bacteria are cultured with sugarcane juice—the sweet liquid from fresh sugarcane—at room temperature. The microbes digest the sugar, producing hydrogen gas as a byproduct. - Step 2: Environmentally Friendly
The process works without electricity and can use seawater or wastewater as the reaction medium. It’s ideal for rural and off-grid settings. - Step 3: Zero Waste
The bacteria also produce acetic acid, a valuable chemical for food and industry, so nothing is wasted. - Step 4: Cost and Scalability
Early estimates suggest hydrogen could be produced for as little as $1 per kilogram, which is far below the current cost of green hydrogen from electrolysis (typically $4–$7/kg). This low cost is mainly due to minimal energy input and use of low-cost materials. - Step 5: Commercialization
The team is seeking industry partners to scale up the technology. Pilot projects in rural India or Brazil could demonstrate the approach and build local capacity.
Why this matters for rural communities:
This method is simple, sustainable, and scalable for small-scale, local hydrogen production. It’s especially promising for rural electrification, small factories, and clean cooking fuel in villages. If widely adopted, it could also revolutionize agriculture, turning every sugarcane farm into a mini energy hub.
Career and Professional Opportunities
These breakthroughs open up major new career pathways for professionals, students, entrepreneurs, and policymakers.
For Farmers and Mill Owners
- New income streams: Sugarcane mills can sell clean hydrogen, furoic acid, and acetic acid as byproducts.
- Reduced waste disposal costs: Bagasse and other residues become valuable, not a disposal problem.
- Partnership opportunities: Collaborating with universities, startups, and energy companies to pilot these technologies.
For Engineers and Scientists
- Research and development: Careers in bioengineering, chemistry, materials science, and energy systems are booming.
- Pilot plant operation: New jobs in building, maintaining, and improving hydrogen-from-waste plants.
- Process optimization: Engineers can make these systems more efficient and cost-effective, opening the door to global export.
For Policymakers and Agencies
- Climate action: Hydrogen from waste can help countries meet their Paris Agreement targets.
- Energy independence: Reducing reliance on imported oil and gas by developing local, renewable hydrogen.
- Rural development: Supporting small-scale hydrogen for clean cooking, electric pumps, and village industry.
For Students and Educators
- Curriculum development: New courses in renewable hydrogen, waste valorization, and green chemistry.
- Internships and research: Hands-on experience with pilot projects and industry partnerships.
- Entrepreneurship: Startups focused on decentralized hydrogen production for communities and small businesses.
Real-World Examples and Practical Advice
Industrial Scenario: Maharashtra, India
Imagine a sugarcane mill in Maharashtra. Today, the mill burns bagasse to get rid of it, contributing to air pollution. After adopting a SECLG gasifier, the same mill could produce clean hydrogen for local buses and trucks, lowering emissions and fuel costs. The mill might also sell furoic acid to pharmaceutical companies, creating a new revenue stream. This model is scalable—other mills could replicate it, forming a hydrogen supply chain for transport, industry, and even power generation.
Rural Scenario: Minas Gerais, Brazil
A small sugarcane farm in Minas Gerais could partner with a local university to install a microbial hydrogen reactor. The farm could use the hydrogen for clean cooking in homes and fuel for small machines. The byproduct, acetic acid, could be sold to a local food company. This approach empowers rural communities, reduces health risks from indoor air pollution, and boosts local economies.
What’s Next?
All three technologies—PEC, SECLG, and microbial—are at various stages of development. The PEC system is already lab-proven and published in credible journals. SECLG is in advanced simulation and prototyping. Microbial hydrogen is ready for pilot projects and community partnerships.
Scaling up will require investment, government support, and business innovation. Sugar-producing countries should consider special incentives for mills and farmers to adopt these technologies. Industry leaders should explore licensing agreements and joint ventures with research institutions. Students and young professionals should seek out training and internships in these emerging fields.
Engineered Ruthenium Catalysts: A Sustainable Revolution for Hydrogen and Ammonia
Monash Breakthrough Paves the Way for Cheap, Large-Scale Green Hydrogen
Hydrogen Fuel at Half the Cost? New Catalyst from South Korea
FAQs About Sugarcane Waste Into Clean Hydrogen
Q: Is hydrogen from sugarcane really cleaner than from natural gas?
A: Yes, because no fossil fuels are used in the processes described here, and no CO₂ is released during production. When hydrogen is burned, only water is produced. By contrast, hydrogen from natural gas emits significant CO₂ during production.
Q: How much does hydrogen from sugarcane waste cost?
A: Estimates vary. The UNIST PEC system is already cost-competitive with hydrogen from natural gas. Microbial hydrogen could be as cheap as $1/kg, and SECLG is expected to be cheaper than traditional gasification because CO₂ capture is built-in. More precise costs will be known as these systems are scaled up.
Q: Can these technologies work with crops other than sugarcane?
A: Yes. Bagasse, straw, corn stover, and wheat chaff—any crop with cellulose, starch, or sugar—could be adapted. The key is access to agricultural waste and local processing capacity.
Q: How soon can we see these systems in use?
A: The PEC system is ready for pilot projects. SECLG is a few years away from industrial deployment. Microbial hydrogen is ready for small-scale pilots. Commercialization timelines will depend on investment, policy support, and industry partnerships.
Q: What happens to the CO₂ captured in gasification?
A: In SECLG, CO₂ is captured as a solid compound during the reaction. It can be stored safely underground or used in industry (for example, in carbonated drinks or fire extinguishers).