Ultralight 3D-Printed Antennas: Imagine a world where antennas—those essential components that help your phone, satellite, or smartwatch connect to the world—are so light, they barely add any weight at all. Thanks to a new technology called Charge Programmed Deposition (CPD), developed by researchers at the University of California, Berkeley, this is now possible. These ultralight 3D-printed antennas can be up to 94% lighter than traditional designs, opening up exciting new possibilities for everything from space exploration to wearable tech.
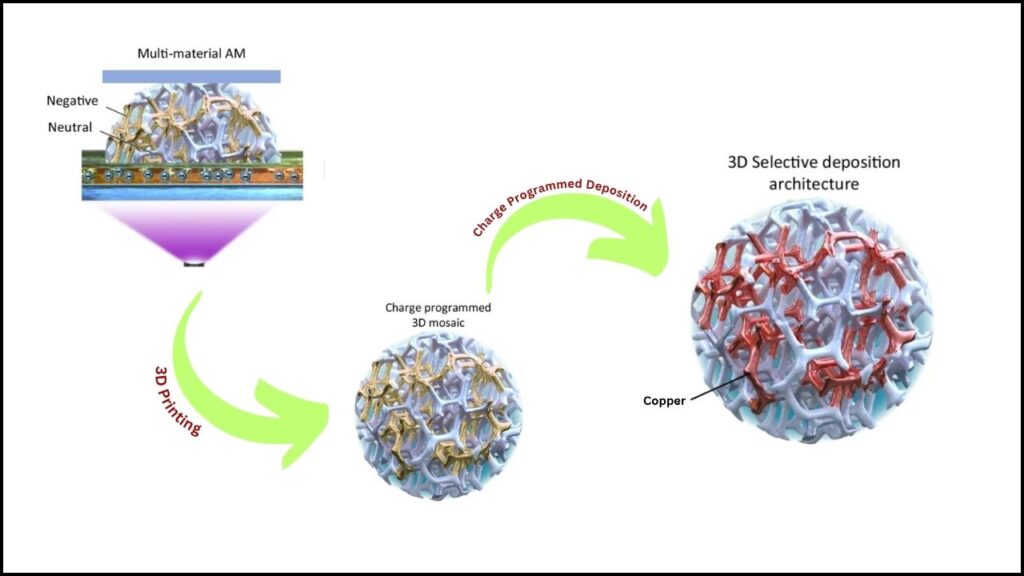
In this article, we’ll break down how this breakthrough works, why it matters, and what it means for professionals and everyday users alike. Whether you’re a curious student, an engineer, or just someone who loves cool science, you’ll find practical advice and clear explanations here.
Ultralight 3D-Printed Antennas
Feature/Stat | Details & Insights |
---|---|
Weight Reduction | Up to 94% lighter than traditional antennas |
Technology Name | Charge Programmed Deposition (CPD) |
Materials | Combines high-conductivity metals (like copper) and dielectrics (insulators) in one process |
Applications | 5G/6G, CubeSats, aerospace, wearables, medical sensors |
Printer Type | Uses desktop digital-light 3D printers—no expensive metal powders or lasers needed |
Complexity | Enables intricate 3D structures (e.g., lattices, transmitarrays) previously impossible to manufacture |
Source/Official Info | UC Berkeley Engineering |
The development of ultralight 3D-printed antennas using Charge Programmed Deposition (CPD) is a game-changer for engineers, scientists, and tech enthusiasts alike. By slashing antenna weight by up to 94% and enabling complex, multi-material designs, CPD opens new frontiers in aerospace, medicine, and next-generation wireless technology. With affordable desktop printers and a flexible, rapid prototyping process, the future of antenna design has never looked brighter.
What Are Ultralight 3D-Printed Antennas?
Antennas are everywhere: in your phone, your car, satellites, and even inside medical devices. Traditionally, making antennas required heavy, rigid materials and complex manufacturing steps. This made them bulky and limited where they could be used, especially in weight-sensitive applications like satellites and tiny wearable devices.
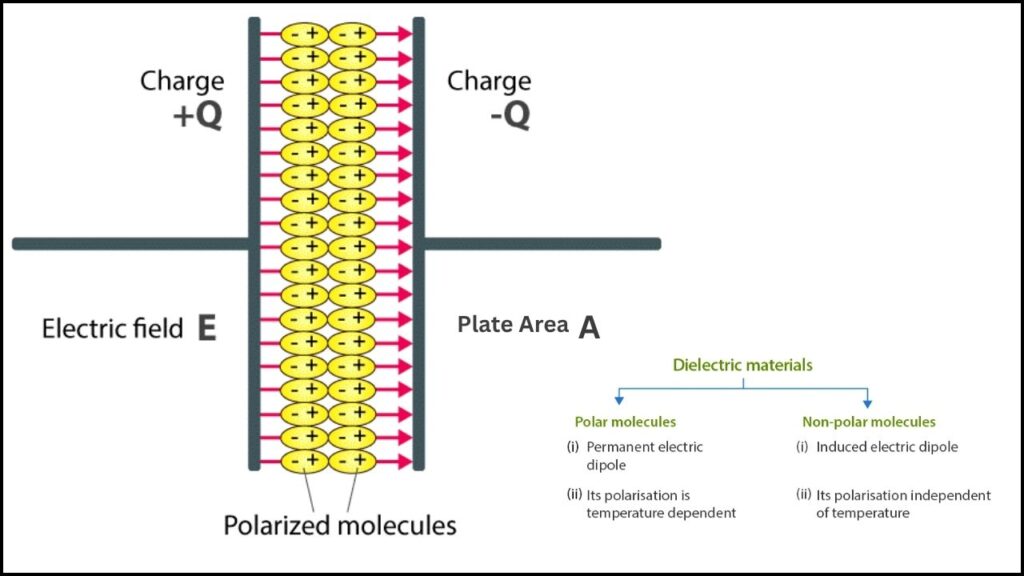
Ultralight 3D-printed antennas are made using a new process that allows engineers to build antennas out of both metals and plastics (called dielectrics) in one go. The result? Antennas that are not just lighter, but also more complex and customizable than ever before.
How Does the Breakthrough Multi-Material Design Work?
The Magic of Charge Programmed Deposition (CPD)
At the heart of this innovation is Charge Programmed Deposition (CPD). Here’s how it works, step by step:
- Designing the Antenna: Engineers use computer models to design the perfect antenna for a specific job, whether it’s for a satellite or a smartwatch.
- 3D Printing the Base: A desktop digital-light 3D printer creates a base structure using special polymers (plastics). These polymers are chosen for their ability to handle heat, cold, or other challenging conditions.
- Programming Charges: During printing, different areas of the base are given positive, negative, or neutral electrical charges. This “charge mosaic” acts like a secret map, telling metals where to stick later.
- Selective Metal Plating: The printed base is dipped into a solution containing metal ions (like copper). Only the charged areas attract the metal, forming precise, conductive pathways—no need for expensive lasers or metal powders.
- Building Up Layers: The process can be repeated to add more layers, combine different materials (like semiconductors or magnetic materials), or create complex 3D shapes.
Why is this special? Until now, no technology could directly pattern both the conductor (metal) and the dielectric (insulator) together in such intricate 3D forms. CPD makes this possible, opening the door to antennas with shapes and features never seen before.
Why Does Weight Matter for Antennas?
Weight is a critical factor in many industries:
- Spacecraft and Satellites: Every gram counts. Lighter antennas mean more room for scientific instruments or longer missions.
- Wearable Devices: Lighter, flexible antennas make smartwatches, fitness trackers, and medical sensors more comfortable and reliable.
- 5G/6G Networks: As networks get faster and devices get smaller, antennas must be efficient, lightweight, and easy to customize.
By cutting antenna weight by up to 94%, CPD technology allows engineers to push the boundaries of what’s possible—whether that means launching more satellites or designing sleeker gadgets.
Real-World Applications and Examples
Aerospace and CubeSats
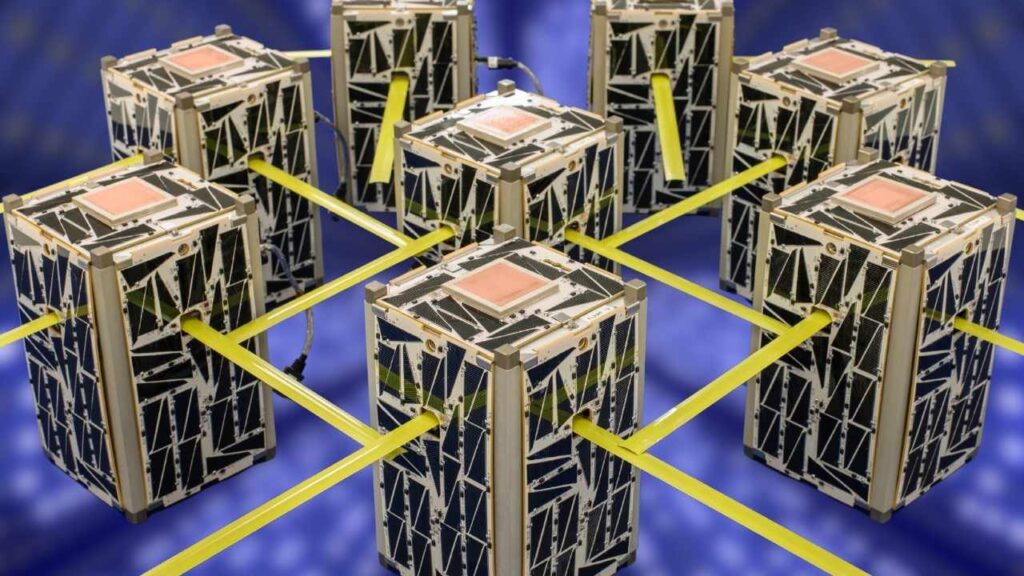
CubeSats are tiny satellites used for research, weather monitoring, and even internet services. Their size and weight are strictly limited. With CPD, engineers can print antennas that fit perfectly inside these small satellites, using high-temperature polymers like Kapton that can survive the harsh conditions of space.
Medical Sensors
Flexible, ultralight antennas can be printed directly onto medical devices that wrap around a patient’s arm or hand. This makes for more comfortable, accurate health monitoring—improving patient care and opening new possibilities for remote diagnostics.
Next-Gen Wireless Devices
Phones, tablets, and wearables are getting thinner and smarter. CPD allows for antennas that are not only lighter but also shaped to fit into tight spaces or even curved surfaces, improving signal strength and device performance.
How Does CPD Compare to Traditional Antenna Manufacturing?
Feature | Traditional Antennas | CPD 3D-Printed Antennas |
---|---|---|
Weight | Heavy, rigid | Up to 94% lighter, flexible |
Manufacturing Steps | Multiple, complex | Fewer, streamlined |
Material Integration | Limited (one at a time) | Multi-material (metal + dielectric) |
Design Complexity | Limited by tools | Intricate 3D shapes possible |
Cost | High (special tools needed) | Lower (desktop printers, no lasers) |
Customization | Slow, expensive | Rapid, easy, on-demand |
Step-by-Step Guide: How Professionals Can Use CPD Technology
1. Choose the Right Printer and Materials
- Use a desktop digital-light 3D printer compatible with CPD.
- Select polymers and metals suitable for your application (e.g., copper for conductivity, Kapton for heat resistance).
2. Design Your Antenna
- Use CAD software to design the antenna’s shape and internal structure.
- Plan where you want conductive (metal) and non-conductive (dielectric) regions.
3. Program the Charges
- Assign positive, negative, or neutral charges to different regions in your design file.
- This determines where metals will attach during plating.
4. Print and Plate
- Print the structure layer by layer.
- Dip the printed object into a metal ion solution; only charged regions will attract metal, forming the antenna’s conductive paths.
5. Test and Iterate
- Test the antenna’s performance in real-world conditions.
- Adjust the design as needed—3D printing makes rapid prototyping easy and affordable.
NTT Docomo Uses Quantum Optimizer to Boost 5G Resource Efficiency by 15%
IonQ To Acquire Oxford Ionics For ~$1.1 B, Expanding Trapped‑Ion Leadership
Quantum Sensor Tracks 3D Movement Without GPS Using Ultracold Atoms
FAQs About Ultralight 3D-Printed Antennas
Q: What makes CPD antennas so much lighter than traditional ones?
A: CPD allows for intricate, hollow, or lattice structures that use less material without sacrificing strength or performance. By combining metals and dielectrics in one process, unnecessary bulk is eliminated.
Q: Can CPD antennas be used in space?
A: Yes! By printing with high-temperature polymers like Kapton, CPD antennas can withstand the extreme heat and cold of space, making them ideal for satellites and space probes.
Q: Is this technology expensive?
A: Not at all. CPD works with desktop-friendly 3D printers and doesn’t require costly metal powders or lasers, making it accessible for research labs and startups.
Q: What kinds of devices can benefit from ultralight 3D-printed antennas?
A: Everything from smartphones and wearables to CubeSats, drones, and medical sensors can use these antennas for improved performance and lower weight.
Q: Where can I learn more or see the official research?
A: Visit the official UC Berkeley Engineering website linked in the Key Highlights table.